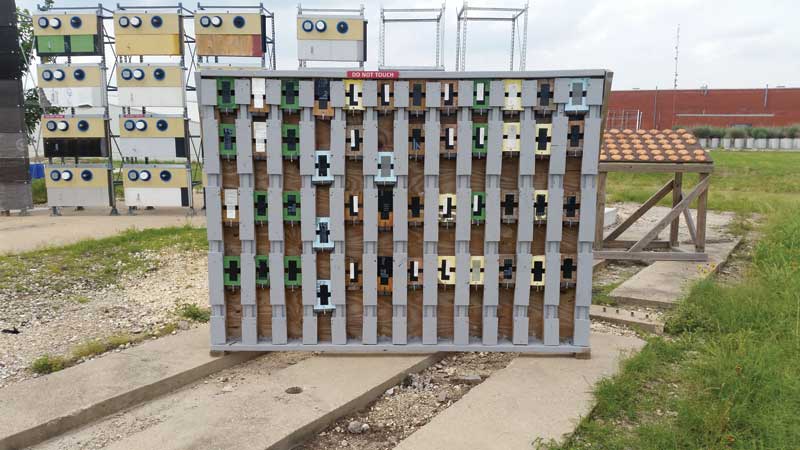
by Anthony M. Garcia, PE, and Jorge M. Blanco
Construction tapes and flashings are used to span joints and gaps, typically in conjunction with a primary water-resistive barrier (WRB) or air barrier. Since they are concealed behind cladding, it is important tapes and flashings are durable. Will they remain adhered in harsh conditions? Can they accommodate movement for the design life of the building? This article’s authors performed hundreds of tests to evaluate different tape adhesive chemistries and durability on a variety of substrates.
Most construction professionals are familiar with traditional rubberized asphalt self-adhered flashing (i.e. peel and stick), but acrylic and butyl tapes are increasingly popular. Construction tapes and self-adhered membrane flashings (collectively referred to as ‘tapes’ in this article) are used to span gaps and transitions in materials, such as at window perimeters, sheathing joints, and other complex geometries.
Tapes are common accessories in WRBs and air barriers such as sheet membranes, liquid membranes, and building wraps. These assemblies are crucial to a building’s performance and durability. Since tapes are used at junctions critical for keeping the exterior out, proper selection and installation are paramount to avoid water infiltration and air leakage that may lead to tenant discomfort—or worse.
Defining the tapes
To define ‘tape’ and its function in construction, the authors reviewed numerous codes and standards, including the 2015 International Building Code (IBC) and 2015 International Energy Conservation Code (IECC).
Regarding WRBs, IBC requires:
[n]ot fewer than one layer of No. 15 asphalt felt, complying with ASTM D226 [Standard Specification for Asphalt-Saturated Organic Felt Used in Roofing and Waterproofing] for Type 1 felt or other approved materials, shall be attached to the studs or sheathing, with flashing as described in Section 1405.4, in such a manner as to provide a continuous water-resistive barrier behind the exterior wall veneer.(This comes from the 2015 IBC Chapter 14, Section 1404, Paragraph 1404.2.)
Flashings, as defined by IBC:
prevent moisture from entering the wall or to redirect that moisture to the exterior”, and “shall be installed at the perimeters of exterior door and window assemblies, penetrations and terminations of exterior wall assemblies… (See 2015 IBC Chapter 14, Section 1404, Paragraph 1454.4.)
IBC does not require or define an air barrier. However, IECC calls for an air barrier to be “continuous” and “provided throughout the building thermal envelope.” (Excerpted from 2015 IECC Chapter 4, Section C402, Paragraph C402.5.1.) For the air barrier, IECC also requires:
joints and seams shall be sealed, including sealing transitions in places and change in materials…Joints and seals associated with penetrations shall be sealed in the same manner or taped or covered with moisture vapor-permeable wrapping material.(See 2015 IECC Chapter 4, Section C402, Paragraph C402.5.1.1.3.)
(The code specifically mentions “tapes” as part of the air barrier.)
As IECC recognizes tapes will be stressed during their service life, it requires sealing materials to be “securely installed around the penetration so as not to dislodge, loosen, or otherwise impair the penetrations’ ability to resist positive and negative pressure from wind, stack effect, and mechanical ventilation.”
In addition to codes and standards, previous research and laboratory testing on WRBs informed the study discussed in this article. (For more information, see the February 2015 issue of The Construction Specifier for the article, “Durability of Water-resistive Barriers,” by Beth Anne Feero, EIT, and David H. Nicastro, PE. Visit www.constructionspecifier.com/durability-of-water-resistive-barriers.) During the construction of the WRB specimens for testing, manufacturers’ accessory tapes were installed at many details; this experience helped develop tape testing methodology and provided a basis for product selection. Ongoing WRB testing will continue to inform future tape testing.
For this study, tapes were defined as broadly as possible, while keeping IBC, IECC, and colloquial definitions in mind. The requirements for inclusion in the testing were purposely flexible.
Tapes typically consist of similar components, including a carrier sheet (i.e. facer or scrim)—often made of polyethylene, polypropylene, or aluminum—and an adhesive layer. A release paper (protective liner) is used on some products; one of the most challenging aspects of engineering a sticky tape is keeping it from adhering to itself on the roll.
The adhesives used in tapes consist of long-chain polymers that interact with substrates under pressure. The polymers create physical bonds that must be very strong in the dynamic and critical applications of building tapes.(The Scientific American article, “What Exactly is the Physical or Chemical Process that Makes Adhesive Tape Sticky?,” can be read online at www.scientificamerican.com/article/what-exactly-is-the-physi.)
Generally, the market is dominated by a few adhesives and their specific uses:
- traditional modified asphalt self-adhered flashings (i.e. peel-and-stick);
- thick butyl tapes that typically complete with modified asphalt as flashings; and
- thin acrylic ‘seam’ tapes, which are often used to bridge gaps or cover seams and laps in WRB, and are thus less flexible but very sticky.
I really like the subject matter, but I feel like I just watched Star Wars Return of the Jedi (I left with more questions than before). I need names folks. Which products should I use and which should I avoid? I want to do a great job for my clients, but what is the point of this article if the results and conclusions are not published? -Frustrated and annoyed
Which flashing tape worked best on OSB. My home is in Ontario with temperatures ranging from -40 F to 100F. I have cedar shiplap siding. I am replacing an exterior, west facing door and window.
I also am interested in the results, would like to avoid building failure into my next project. How can we get the results of the tests?
I’m also interested in the results.
“Only 95 specimens (26 percent) reached the cutoff time of 30 days without failure” and we won’t even name one for you. What’s the point of this experiment if you don’t share your results?
Which products worked best on OSB?
I really would like to review the results. What is the point of doing the experiment if you aren’t going to share the results? I’ve tried over 10 different types of tapes trying to learn what tape sticks to rough side osb with no luck. All fishmouth or fall off. Which tapes did you get to last 30 days?
I’m going to join in with everyone else… this doesn’t make any f sense what the, where are the results?