Design amnesia with mold and modular construction
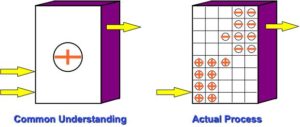
Image courtesy Liberty Building Forensics Group
You can’t fake the funk
The case study on the previous page was specific to modular construction, but the general principles and challenges involved are common to today’s design and construction industry. So how can designers and contractors avoid these problems? To help avoid catastrophic mold and moisture building failures, here are four points of which every architect and contractor must be aware.
Buildings should not be designed in silos.
Despite advances in technical understanding and higher standards for building performance (e.g. enclosure airtightness), tasks like designing building envelopes are still being completed in a vacuum of other critical disciplines. On a recent project, the façade consultant was asked how the design interfaced with the overall building pressurization requirements established by the HVAC design. The answer: “We don’t consider that in our design—they do their thing and we do ours.”
Keeping silo design from happening on a project means more than using tools like building information modeling (BIM). While BIM is good for preventing field conflicts, there is much more to address concerning multidisciplinary building performance. Careful coordination between disciplines, such as the architect and HVAC designer, must occur to ensure problems like compromised wall systems, building air infiltration, and dehumidification do not become catastrophic.
Design and construction guidelines must be specific to the project.
If pertinent, one should include each problem that has been analyzed and the solutions that were provided. This step helps avoid corporate amnesia by allowing for lessons learned to be pushed forward to new team members, and for a transfer of knowledge from past expertise to become part of future decisions. Get the right information to the right person at the right time—it does no good for lessons learned to stay among only those who attended expert depositions. This information needs to be passed on to the design and construction teams.
Experts should be brought on early in the process.
Periodic peer reviews should be used to ensure the information provided to the design and construction teams is passed along at the right time. These critical project pressure points can virtually guarantee success or failure, depending on what decision is made.
When problems arise, minimize occupant outrage as quickly as possible.
This becomes one of the greatest influencers on the cost of fixing a building. J. David Odom, a senior consultant with Liberty Building Forensics Group (LBFG), and a colleague of this article’s authors, found this out in the early 1990s with projects like the Martin County Courthouse. In this case, the occupants of the buildings lost confidence in the fix and ultimately drove a much larger ‘repair’ than was necessary. The final costs increased from $2.5 million to more than $24 million because of this ‘occupant outrage factor.’ (For more on the impact of occupant outrage on a project, see Peter Sandman’s work.)
Handling occupant confidence (or lack thereof) is one of the key areas any designer or contractor must master. If they do not, they will encounter costs that are multiples of what the repair should be.
Conclusion
Building performance can be highly predictable. Design professionals should use this to their advantage by being wise about how all endeavors are approached and managed. ‘Hope’ is important for many aspects of life, but in the design and construction business, hoping for something to work is never a good premise.
Further reading |
Liberty Building Forensics Group (LBFG), the firm at which this article’s authors work, has published a series of e-books for free download: |
George DuBose, CGC, president of Liberty Building Forensics Group, brings more than 25 years of experience in building forensics, with a focus on failures related to mold and moisture issues. He is co-author of three manuals on indoor air quality (IAQ) and mold prevention, and has consulted on ductwork remediation projects, large-scale resort and hotel properties, multifamily residential buildings, and educational campuses. DuBose can be contacted at g.dubose@libertybuilding.com.
Steven Gleason, PE, has over 25 years of experience in construction consulting, including evaluation, design, project management, and expert testimony services related to moisture intrusion and building envelope failures. He provides consulting services related to a wide variety of construction materials and building envelope components including masonry, concrete, glazing, stone, stucco, exterior insulation and finish systems (EIFS), sealants, coatings, and roofing and waterproofing systems. Gleason has consulted on more than 500 projects, ranging from residences to over 70-story high rises. He can be e-mailed at s.gleason@libertybuilding.com.
Nathan Sanders, CIH, LEED AP, is a forensic Certified Industrial Hygienist, with more than a dozen years of professional experience in occupational & environmental health and safety. He has conducted hundreds of evaluations to evaluate physical, biological, and chemical hazards in occupational, residential, and community environments. Sanders develops and implements proactive pre-occupancy IAQ testing protocols, leads administrative duties for LEED-certified projects, and assists in commissioning activities in newly constructed buildings and renovated buildings. He has provided expert opinions for microbial and chemical IAQ litigation efforts. Sanders can be reached at n.sanders@libertybuilding.com.