SBWTC
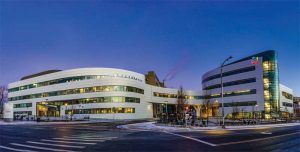
For SBWTC’s parking garage, the design-assist process was different, illustrating the flexibility of this method. Here, the material supplier was responsible for a highly customized, vertically oriented louver fin for the exterior of a parking garage. The louver fins were custom-fabricated from 5-mm (3/16-in.) thick solid aluminum plate fins cantilevered 1 m (4 ft) off the face of the precast structure.
There are 650 louver fin assemblies coated in 12 different custom colors. Due to these unique and specific details, the design-assist process was very structured and daily conference calls were scheduled over a two-month period until the design was finalized. Discussion topics ranged from establishing the custom colors, design and coordination details, schedule impacts, and budget.
From the beginning, the project architect (Fennick McCredie Architecture) understood the importance of collaborating with a manufacturer to help make the design a reality. As the architect, GC, installer, and manufacturer were able to communicate continuously with one another on this project, the shop drawings were developed simultaneously by the manufacturer and the architect, who was responsible for issuing the construction documents. Subsequently, each team was also familiar with these documents, thereby making the approval process seamless. The fabrication process was also able to begin months earlier when compared to the timeline of the traditional bid schedule. Much of the tasks that occurred during the design-assist phase, such as structural analysis and coordination with adjacent trades, occurred prior to submission of shop drawings. These tasks typically require additional rounds of revisions to shop drawings and re-submissions when operating under the traditional design-build processes.
“When expectations are properly set, design assist can be a good process that allows designs to be quickly and cost-efficiently tailored to the particular strengths of a selected subcontractor or manufacturer,” Noblett adds. “As an inherently collaborative process, you can build a lot of goodwill and a cooperative spirit solving issues early on with the entire team.”
Hartford Hospital Bone and Joint Institute
Unique challenges were present with the Hartford Hospital building. The edifice has a free-flowing curved design with few flat exterior walls. As was the case with PSU and SBWTC, the architect for the Hartford project, Perkins + Will, first prepared their design concept of the façade and then shared it will the rest of the team. Solid 3 mm (118 mils) aluminum plate possesses the ability to maintain a consistent curve, making it the obvious choice to achieve the specified undulations. A rainscreen wall system with dry joinery and a drained and vented cavity behind the wall was also specified. The cut edges of the face plate material in this system are the panels’ edges, and this capability is only achievable with metal plate. Since the hardware is concealed from view, a ‘floating’ visual effect is created.
As with other projects that employed design assist, each had team developed, modified, and coordinated specific details regarding the Hartford Hospital building. Early on in the process, panel system details were developed such that they could be incorporated into contract drawings. To meet design needs, custom aluminum extrusions were created and integrated into the panel design at all of the curtain wall coordination details. Working with the design-assist process meant special tooling could start earlier on these one-of-a-kind elements, such as the extrusion panels that typically have long lead times. Consequently, the manufacturer was able to begin the material procurement and production process earlier, saving time and money.
Results
Each of these three projects was a success as a result of the design-assist process. Information was exchanged efficiently and in a timely fashion. Every team member understood and had budget, design, and schedule goals at their fingertips, and at all stages, details were shared and discussed amongst those involved. There was consistent sharing of information and transmission of ideas. This meant all the stakeholders could quickly determine how each idea had the potential to affect the project either positively or negatively and make informed, well-rounded decisions to everyone’s benefit.
John Scorsone is a sales engineer with Metalwërks, a manufacturer of precision, high-performance metal plate exterior façade systems, integrated curtain wall components, and custom architectural features. Scorsone holds an associate’s degree in architecture from Delaware County Community College. He can be reached at jscorsone@metalwerksusa.com.
Very informative article John! I’m happy to see the Hartford Bone and Joint Institute still making news. We at SBG digitally printed, bent and insulated much of the facade glass. We worked closely with the architect to perfect the graphics and desired transparency levels of the printed frit. The outcome of an award winning project would not have been possible without the collaborative mindset of the design assist process.