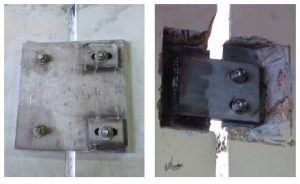
Problem #1: Inappropriately constrained building materials and a lack of consideration for internal forces and stresses induced by volume change
When a structural engineer inappropriately constrains concrete structural members, preventing building movements associated with volume change, connection distress is an inevitable result.
At a parking garage in a northern climate, the exterior wall was made up of multiple precast concrete shear wall panels. The structural engineer did not consider volume change of the individual panels or the building as a whole when they selected rigid panel-to-panel connections. Even though they designed each wall panel to act separately when resisting lateral loads, linking the panels together with rigid panel-to-panel connections created one continuous wall. The connections consisted of embed angles cast flush with the edge of two adjacent panels and a steel plate welded across the vertical panel joint to the embed angle in each panel. The embed angles were recessed into the panel face, creating a pocket, which was grouted after panel installation. See Figure 1 for the original embed angle detail. Shortly after construction, volume changes caused by a combination of creep, shrinkage, and thermal effects led to a buildup of stress at the connections. This culminated in prying at the embed angle connections, delamination and spalling of the surrounding concrete, and tension/shear failure of the embeds (tension/shear failures of embed angles similar to the ones discussed in this article were studied by H.S. Lew, et. al. and reported on in their article “Performance of precast concrete moment frames subject to column removal: Part 1, experimental study”). Typical connection distress is shown in Figure 2. A more appropriate connection design (and the eventual repair design) would consist of horizontal slotted bolt connections, which allow for volume change movements across the vertical joint after construction and prevent stress concentration at the connections. The repaired connection types are shown in Figure 3.
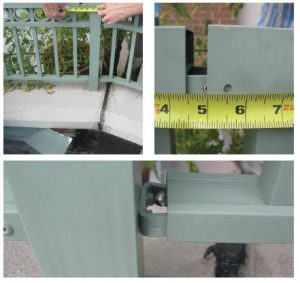
For best practice, when designing a concrete structure, it is imperative the structural engineer consider and calculate expected movements due to temperature change, creep, and shrinkage. It is their responsibility to communicate the expected magnitude to the rest of the design team. The expected movement should be accommodated by appropriately designed expansion joints and connections. If a concrete member must be constrained in a way that inhibits volumetric expansion and/or contraction, the member and its connections should be designed to resist anticipated induced stresses.
Problem #2: Lack of design team coordination for building expansion joint locations
Building expansion joints can effectively alleviate forces and stresses caused by volume change, but it is important the design team coordinates structural and architectural expansion joint locations.
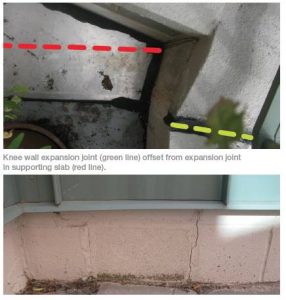
Poor coordination of expansion joint location became particularly problematic at a building in a northern climate. The first floor plan of the structure was larger than the remaining stories. Above the first floor, concrete framing and exterior masonry walls were inset to create terraces at the second floor. At one terrace, aluminum railings located on top of a masonry knee wall spanned across a building expansion joint. Figure 4 depicts gaps and damage at the railing connections caused by movement at the expansion joint, pulling the railing apart. Further, Figure 5 shows masonry knee walls that were installed with expansion joints either missing or offset from the expansion joint in the terrace concrete slab. Different expansion joint seal types, the lack of appropriate seal transitions and movement at offset joints eventually lead to water infiltration into the space below.
Damage to the railings and masonry knee walls and water infiltration into the space below could have been avoided if the design team had properly coordinated expansion joint locations and worked with the expansion joint seal manufacturers to provide proper expansion joint transitions—instead, their lack of communication and poor detailing led to an expensive problem.