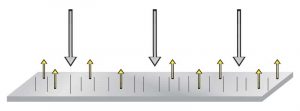
AAMA 2604
This is an ‘intermediate’ specification. A paint meeting this specification would be a 50-percent fluoropolymer resin-based coating. An application for this paint would be storefronts, doors, or other high-traffic areas. This finish will provide good color and gloss retention. It will also provide adequate hardness and abrasion resistance.
For color uniformity of solid paint colors, both performance specifications recommend a maximum deviation of 2 Delta E from an agreed upon color standard. Delta E is the standard unit of measure for color variation measured typically with a digital spectaphotometer. With metallic coatings, it can be challenging for this tool to register a proper color reading. For this reason, AAMA specifications note paints containing mica and metallic flake reflect and scatter light in random patterns, therefore, exact color uniformity should not be expected. Color shifting should be anticipated when viewing from varying angles and distances.
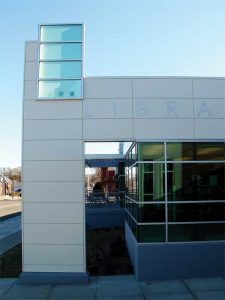
Photos courtesy Dri-Design and Linetec
Per the AAMA-recommended guide specifications, coatings should be visibly free from flow lines, streaks, blisters, or any other surface imperfections in the dry-film state on exposed surfaces when observed at a distance of 3 m (10 ft) from the metal surface and inspected at an angle of 90 degrees to the surface. For applicators following AAMA guidelines, the quality assurance team inspects material as it exits the paint line at a distance of 3 m, looking for objectionable defects to the surface of the part, such as blisters, pops, paint sags, inconsistent coverage, etc.
Due to the metallic coatings’ translucent nature, having to rework panels will result in heavier paint thickness and will alter the appearance and color of the panel, causing it to look different than the other panels on the project. For small defects, it might be in the best interest of the building team to choose aesthetic uniformity over reworked, noticeable inconsistencies. These small defects seen at 3 m will not affect the performance of the coating.
Metallic painted aluminum panels can also appear to have a different color if they are not all installed on the same plane, or are allowed to billow or to oil can. Panels could measure an identical Delta-E color match, but will appear completely different due to the slight variance in installation.
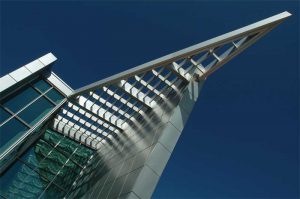
To inform and reassure the entire building team about the expectations of these finished products, consider advising the owner, architect, general contractor (GC), and installer that some degree of variation is acceptable and should be expected.
Additional considerations
Supporting projects with sustainability goals, metallic coatings can be applied to recycled aluminum. At the end of its useful life on the building, the finished aluminum can be recycled or mechanically or chemically stripped and reused.
Factory-applied finishes also can contribute to the project’s indoor air quality (IAQ) and the installing contractors’ wellness because the volatile organic compounds (VOCs) associated with some liquid coatings’ solvents have dissipated prior to reaching the jobsite. Environmentally responsible finishers safely capture and destroy the VOCs in their facilities. Some of these finishers use a 100 percent air capture system and destroy the VOCs with a regenerative thermal oxidizer, so there is no adverse environmental impact.
Installers should also be advised that most metallic coatings are not intended for field touch-up. If the finished material is reworked in the field, a small blemish can become a larger issue. Touch-ups also add thickness to the paint, which can change the perceived color and reflection.
Architectural aluminum building products finished to AAMA’s performance guidelines with metallic coatings can remain durable and attractive for many years. Some finishers offer warranties up to 20 years.