Post pockets should not explode
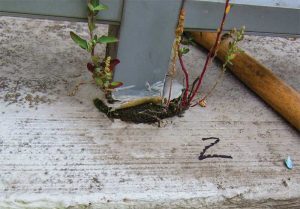
This is, unfortunately, quite common. The concrete around a rail post pocket cracks, then spalls, quite spectacularly in some cases (Figure 1), creating falling hazards and rendering the post connection worthless. Not all post pockets fail this way. In some cases, the grout within the post pocket just simply weathers or turns to rubble (Figure 6).
The detail is deceptively simple: Set the post into a hole sleeved or core-drilled into the concrete and then fill the hole with grout.
As explained, the ‘explosion,’ or expansion of the contents of the pocket, can crack and spall the surrounding concrete, and sometimes thrust the rail post out of the pocket (Figure 7). There are three general mechanisms by which this expansion can occur:
- use of expansive grout in a wet environment;
- freezing and expansion of water in the pore structure of the grout; and
- corrosion of embedded metal, such as reinforcement steel, post sleeve, or the post itself.
All three mechanisms result from the use of inappropriate grout, and it is common for all three to occur within the same pocket. Exposure to the chlorides from de-icing agents and marine environments can significantly exacerbate the problem. In the authors’ view, a lot has been written about ‘non-shrink’ grout and its use for setting rail posts and stone cladding anchorage, yet it continues to be used largely because many of these products are marketed as being appropriate for outdoor use. Though the great product may be advertised for outdoor use there are several conditions listed in the fine print that must be met, and above all, the grout must not become wet—a highly suspect requirement for a material intended for the outdoors. If compliance with ASTM C1107, Standard Specification For Packaged Dry, Hydraulic-Cement Grout (Nonshrink), is specified, it should be with the caveat that the grout be demonstrably appropriate for outdoor, exposed, wet, and freeze-thaw conditions.
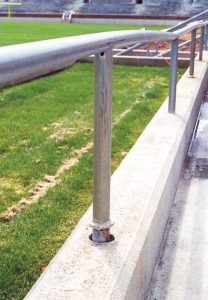
Non-shrink grout, as the name implies, typically incorporates shrinkage compensators to offset the normal dry shrinkage of cementitious grout during initial cure. Gypsum or hydrated calcium sulfate is often used as an expansive additive (or in some cases as the primary binder) to balance the shrinkage of the grout during curing, thereby making it non-shrinkable. Gypsum is mildly water soluble and tends to be unstable under prolonged exposure to moisture. The transformation of the sulfate mineral to a chemical structure with higher water content results in volume instability of the grout, thus creating an expansive force. Gypsum can also re-crystalize on drying, but in a weaker, less-compact form, and causes expansion. Over time, this cycling turns the grout into rubble. The problem worsens in freeze-thaw environments where water penetrates the grout and freezes, providing another expansion mechanism. Worse still, with gypsum in the pore solution, the pH is approximately neutral and not high enough to provide passive resistance to the corrosion of the embedded steel, another expansion mechanism. Even a small amount of inappropriate grout can be problematic, as shown in Figure 8 where not all of the material had been removed from a post pocket. The small amount left at the bottom of the pocket expanded and blew out the side of the wall.
Absolute avoidance of gypsum is impossible, as it naturally occurs in trace amounts in Portland cement and some mix aggregates. Even though the product literature may say “no added gypsum,” it is not necessarily gypsum-free (it should be noted ASTM C1107 does not preclude grouts with added gypsum). Cementitious grouts without added gypsum and tolerable to wet environments and freeze-thaw cycles are available. Epoxy-based grouts are effective and qualify as non-shrink, but can also be relatively expensive. The designer should decide whether non-shrink grout is really needed for the application. Shrinkage cracking within the grout is unacceptable but avoidable if it is properly mixed and cured. Many grouts are very specific about the degree of mixing and the required amount of water. It is recommended to stick with a proven, commercially available product, and avoid mixing and matching grouts, even from the same manufacturer.
Taking measures to reduce the exposure of the grout to moisture is also desirable. It is advisable to fully fill the post holes so water cannot pond (and freeze and thaw) in incompletely filled post holes. Crowning the grout to shed water is an option, as is installing a sealant bead around the base of the post to cover the grout. Sealant, however, is fallible and a regular maintenance item.
When aluminum base plates have welded attachment flanges, or are to be welded to the post, the welding process reduces the allowable strength and may not be structurally adequate to transfer loads from the post to the plate.
Additionally, aluminum railings should be kept from contact with cementitious materials or dissimilar metals by the use of appropriate separation materials or specified coatings, such as a heavy-bodied bituminous paint, methacrylate lacquer, zinc chromate, or other coatings to prevent an aluminum-concrete reaction or an electrolytic action between aluminum and dissimilar metals. The design team needs to run the numbers and check compatibility of the specified materials.. |
Most railing systems are hollow, and condensation within the system should be weeped out at the post base. The weeps should be set such that the post base does not hold water. A pourable sealer can be used within the post to fill the hollow portion of the post up to the level of the weep. Some railing systems have condensation sleeves or diverters.
I would love to post this story on my website. Is that possible?