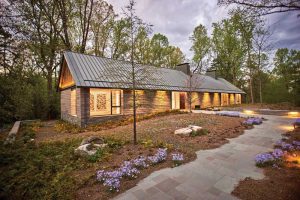
While the basis of the patina is alkaline zinc carbonate, additional substances are incorporated from the local humidity, rainfall, snowfall, and air pollution levels. Therefore, the color of the patina can vary. Natural patina will appear lighter when used in marine locations because the air contains chlorides. In environments where sulfur levels are higher, the patina may appear somewhat darker.
White deposits from salt in the atmosphere can develop on all metal roofing materials. In marine environments, lighter colors of architectural zinc will not show salt deposits as much as darker surfaces. For aesthetic reasons, lighter surfaces are often chosen for coastal applications.
After the true patina has fully formed, the process will slow down but never stop. Natural patina will form to a soft blue-gray or graphite-gray color, depending on the alloy type. To achieve a vintage look at the time of installation, some architectural zinc manufacturers can accelerate the patination process under factory-controlled conditions before they fabricate the material into roofing.
Additional color and coating options for zinc roofing include:
- Pickling—a pre-treatment process which chemically etches the metal and derives the color from the alloy. The resulting appearance brings out the metal’s natural gray color and subtle grain texture.
- Phosphating—a treatment where phosphate crystals are deposited on the surface to create a darker color. The resulting color is produced by the durable phosphate coating, which looks like the zinc structure of natural patina.
- Color coating—a finish applied to the zinc, which seals the metal with a selected color during its manufacturing process. The resulting color is imparted by the coating.
While coating the zinc surface will delay the visible patination process longer, all these coloring techniques will eventually fade and give way as the material continues to naturally weather and form its patina.
Selection criteria and considerations
The architect can evaluate and qualify zinc manufacturers based on material quality, flatness, finish color, texture, selected panel profile, application system, availability, customer service, and technical support. The specifications should stipulate a zinc manufacturer who certifies its material to ASTM B69-20 and has demonstrated its experience in similar climates and applications to help ensure successful projects. As appropriate, designating one zinc manufacturer as the basis of design will further minimize opportunities for variations in material performance.
At the onset of construction, the contractor’s submittals should include the manufacturer’s product data, details, instructions, material samples for submittal, as well as engineering calculations and shop drawings. A professional structural engineer licensed and registered in the same location as the project must prepare and stamp the calculations.
To ensure a zinc roofing system meets a project’s aesthetic and performance requirements, the architect may specify a mock-up. The contractor should construct the mock-up using specified materials, methods, and quality control standards. If the contract requires it, the contractor should install a full-size mock-up on location for final approval.