Designing and testing façade access equipment
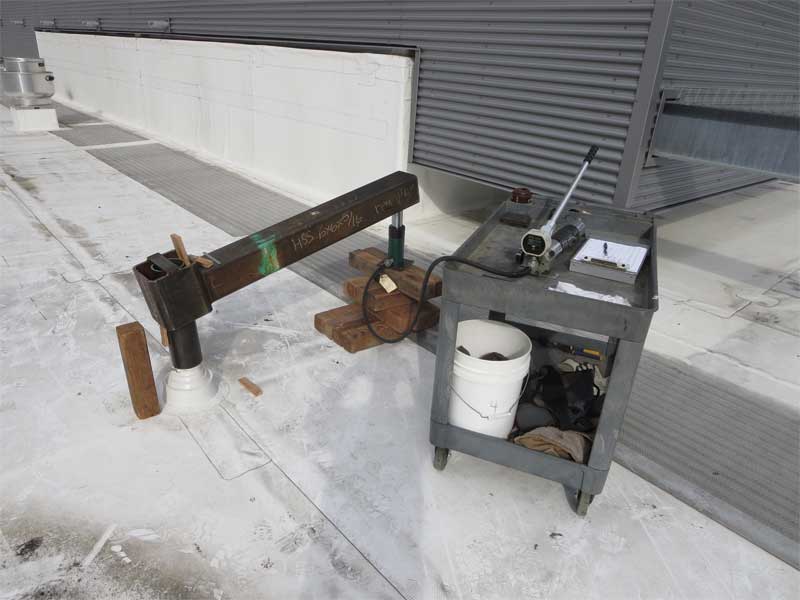
ASCE 7-16 and the 2015 IBC
ASCE 7-16 and the 2015 IBC incorporate design loads for façade access equipment that are consistent with OSHA strength requirements and comply with accepted structural engineering design procedures. Both ASCE 7-16 and the 2015 IBC require structural elements supporting façade access equipment (including both davits and outriggers, their connections to the structure, as well as the beams and columns supporting these elements) be designed to resist an unfactored service live load equal to the larger of:
- 2.5 times the rated load of the supported
hoist; or - 1.0 times the stall load of the supported hoist.
When combined with the applicable live load
factor of 1.6, the factored design live load equals the larger of:
- 4.0 times the rated load of the supported
hoist; or - 1.6 times the stall load of the supported hoist.
Unlike OSHA, the ASCE 7-16 and 2015 IBC design approach eliminates the need to distinguish between window-washing/maintenance activities and construction activities. Where the stall load of a hoist is unknown, it should be assumed to be 3.0 times the rated load of the hoist (the maximum allowed by OSHA), resulting in an equipment design load of 1.6 x 3.0 = 4.8 times hoist’s rated load.
For fall-arrest/lifeline anchorages, ASCE 7-16 and the 2015 IBC adopted an unfactored live load of 13.8 kN (3100 lb) for each attached person. Applying a 1.6 live-load factor, the resultant factored live load is 22.1 kN (4960 lb), essentially matching OSHA’s requirement of 22.24 kN (5000 lb) for each attached person.
Testing requirements
OSHA requires building owners provide users of façade access equipment with assurances that all equipment meets OSHA’s requirements, including the minimum strength requirements. OSHA further requires the assurance be based on a “field test” prior to initial use and following any major modifications. OSHA provides no guidelines for what constitutes an acceptable “field test.” It is typically interpreted to mean an in-situ load test, with the test method and magnitude left up to the judgment of the engineer in charge of the testing and certification program. Regardless of how the field test is performed, it must demonstrate that the tested equipment and its connections to the building meet the minimum capacity requirements of OSHA 1910.66. Otherwise, it is an invalid test and cannot be used as a basis for an assurance to the user.
Complicating the matter, OSHA published an interpretation in 1993 that conflicts with their published assurance and testing requirements. The 1993 interpretation by OSHA illogically indicates that test loading to the minimum capacity requirements is not required by the assurance/testing requirements in OSHA 1910.66.
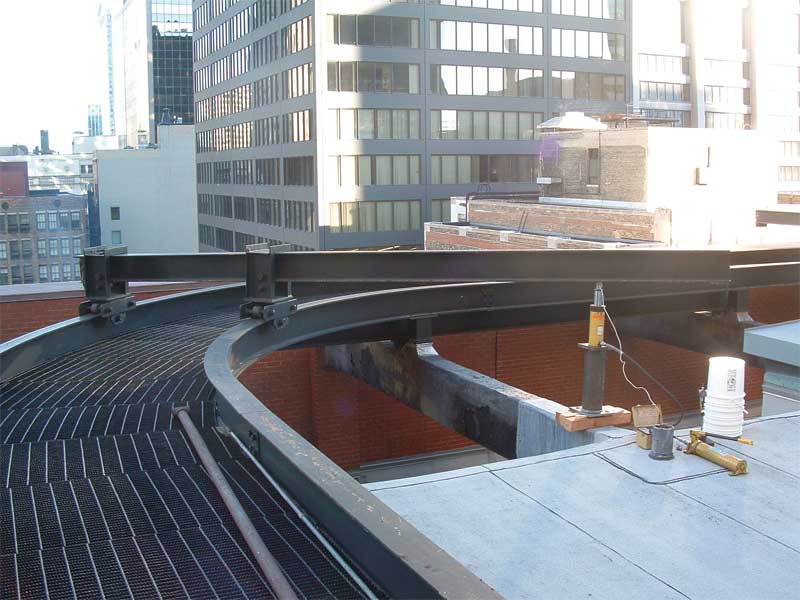
To satisfy the testing and assurance requirements of OSHA 1910.66, some engineers advocate for load-testing façade access equipment to only 50 percent of the minimum required strength. Use of this 50-percent test load limit was advocated in an article that appeared in the September 2016 issue of The Construction Specifier. Other engineers, including the authors of this article, believe that valid tests loads must be 100 percent of the required strength to verify whether façade access equipment complies with a particular strength requirement. Determining a logical test procedure to ensure the equipment is tested in the appropriate direction, and ensuring excessive deflections do not occur, requires consideration of well-established principles of mechanics, material science, and statistics.
Testing to only 50 percent of the minimum required strength
Advocates in favor of limiting testing to only 50 percent of the required strength (or ‘50-percent tests’) have often tested davits and outriggers to only twice the rated load of the supported hoists, and fall-arrest anchorages to only 11.1 kN (2500 lb). These test loads are only half of the minimum required strength for these components (and less than half the required strength for hoists used for construction purposes). Additionally, many proponents of this approach recommend only testing a sampling of the equipment and not every element. Advocates of this level of testing claim it is standard in the industry, but this is false; further, the 50-percent approach has absolutely no scientific or structural engineering justification.
Arbitrary limits on test loads and sampling rates may result in missing design or construction defects, deterioration, or damage that could result in failure—either when loaded between 50 and 100 percent of the minimum required capacity or at untested locations. This level of testing prevents owners from providing a valid OSHA-required assurance the equipment has the required capacity. Engineers who certify compliance with applicable capacity requirements based on test loads at 50 percent of the minimum required capacity are providing false certifications.
The following examples show the potential irrationality of this approach. In one case reviewed by the authors, an engineer tested a group of apparently identical fall-arrest anchorages to only 11.1 kN (2500 lb). While several of the anchorages failed and were unable to resist even the 50-percent test load, the engineer certified that the remaining anchorages could all support the full minimum required design load of 22.2 kN (5000 lb). Despite the blatant red flag that a significant number of the anchorages were not able to resist even half of the design load, the engineer took the leap of faith that the remaining anchorages—also tested to only 11.1 kN (2500 lb)—would be able to resist 22.2 kN (5000 lb).
In another case, an engineer certified a group of davit bases based on testing to only half the minimum required capacity. Subsequent testing to higher loads revealed several bases did not have the strength needed to carry the minimum OSHA-specified loading. In the time between the two tests, workers had unknowingly placed their lives at risk by using the defective equipment.
In their arguments against 100-percent testing, proponents of 50-percent testing often confuse the term “minimum required strength” with “ultimate strength.” By definition, the “ultimate” strength of an element is the load at which that element fails. As structural engineers know, the ultimate strength of a properly designed, constructed, and maintained element is always greater than the minimum required strength. When ultimate strength is less than the minimum required capacity, only load-testing to 100 percent of the required load will reliably identify this unacceptable situation.