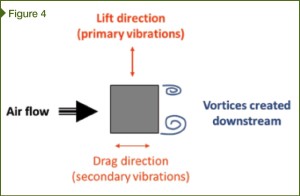
As shown in Figure 4, when air flows across a structural member, it creates vortices on both sides downstream of the member. The difference in pressure from the consequent uneven pressure drops on the sides of the member, causing it to move side to side perpendicular to the air flow’s direction. Movement in wind direction (i.e. drag direction) is of secondary significance. Primary structural oscillations perpendicular to air flow, or in the lift direction, is referred to as vortex-induced vibration (VIV).
The relationship between wind speed and VIV frequency depends on several factors relating to the properties of flowing air and the structural member’s surface and shape. For simplicity, this relationship can be expressed using the blue line in Figure 5. As the graph indicates, higher wind speeds result in higher excitation frequencies. Since resonance occurs when excitation frequency matches the structure’s natural frequency, any structural member can potentially be excited into resonance under high enough wind speeds.
Structures such as marine risers, bridges, and long utility poles/towers are routinely designed to resist VIV. When the length of a structure or a structural member is too long compared to its cross-sectional depth, it becomes more susceptible to damage by VIV. (The most recognized example of this phenomenon is the famous 1940 collapse of the Tacoma Narrows Bridge in Washington.) Fortunately, wind speeds required to excite everyday structures are normally higher than the typical range in habitable areas of the world.
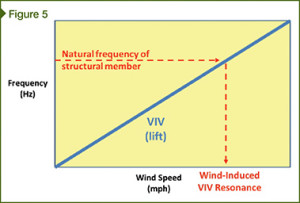
Figure 6 shows the mode shape of lateral picket vibrations of a balcony railing as simulated using finite element analysis. This vibration pattern has been verified in wind tunnel tests and observed by occupants at wind speeds and gusts as low as 32 to 40 km/h (20 to 25 mph). This example of railing resonance can generate severe magnitudes of noise and vibrations in windy days described by some occupants who experienced this phenomenon. In a study conducted by this author, the occupants described the noise and vibrations as “train noise,” “floor vibrations that rattle furniture,” and “uninhabitable.” In addition to noise and discomfort, when these vibrations take place for long periods, fatigue damage at connecting welds may cause some pickets to break off, exposing occupants to physical danger.
Recommendations
While wind excitation is not currently a design factor for balcony railings, recent industry trends and occupants’ experience suggest it should be. Some developers of recent high-end coastal properties in several southern states have learned this lesson in an unpleasant way. Complaints from occupants have caused expensive retrofits and disputes. In some instances, legal actions were pursued to settle the matter. This problem has become so common, several companies have been formed to develop and sell repair kits and services to property owners to control these vibrations.
In the absence of industry standards, there are no adequate means for developers, architects, or railing manufacturers to handle this problem or predict railings’ performance. In extreme cases, all parties can also become targets for legal action. To ensure the safety and comfort of occupants, and to protect the interests of all parties involved, some corrective action must be taken.
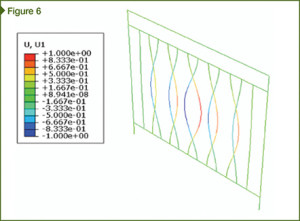
Typically, problems of this sort can be handled using one, or a combination of, the following:
- engineering analysis and/or testing requested by the architect on a project-by-project basis;
- engineering analysis and/or testing conducted by manufacturers during product development; and
- industry-wide standards or design tools.
Due to the magnitude of the problem and potentially prohibitive cost of the first two options for small projects or manufacturers, the third option seems to be the most effective solution.
An industry-wide mechanism may be accomplished using various forms. One option is a rating system based on physical wind-tunnel testing of product specimens. This is the most accurate way to determine the wind speed at which railings become susceptible to resonance. The system can capture the actual behavior of imperfect structural connections and variations in the manufacturing process, which are difficult to handle using computer models. The generic system can be used for any design or configuration. If well-designed laboratory instrumentation and procedures are developed, this approach can produce results in a timely and cost-effective manner.
Another option involves using design aids based on simplified analysis of common railing configurations. Such tools, which may be in the form of design charts or software, can be used by manufacturers to design products and by architects to estimate the resonance wind speed of available products. This approach typically requires:
- determining design parameters;
- developing an analysis methodology;
- executing computer simulations; and
- calibrating accuracy using representative wind-tunnel testing.
To encapsulate many design parameters into a simplified office tool, a sizeable upfront investment of resources may be necessary.
Conclusion
An effective long-lasting solution to vortex-induced vibrations of balcony railings requires group action by architects, manufacturers, or both. Given the observed trend, esecially in coastal regions, and potentially serious consequences of this problem, there seems to be enough incentive for both parties to support such an endeavor.
Mahmod Samman, PhD, PE, FASME, is the president of Houston Engineering Solutions. He has more than 25 years of engineering experience. Samman earned his PhD in engineering mechanics from Duke University in 1991 and is a licensed professional engineer in Texas. In addition to his consulting practice, he taught a graduate level course in finite element analysis at the University of Houston, as well as numerous seminars to industry professionals. Samman has one patent, over 30 journal and conference publications, and numerous industry reports. He is a Fellow of the American Society of Mechanical Engineers (ASME), and a member of the American Society of Civil Engineers (ASCE). He received the Herbert Allen Award from the South Texas Section of ASME, a Fulbright Scholarship from the U.S. Department of State, and the Young Engineer of the Year Award from the City of Houston. He can be reached at mms@hes.us.com.