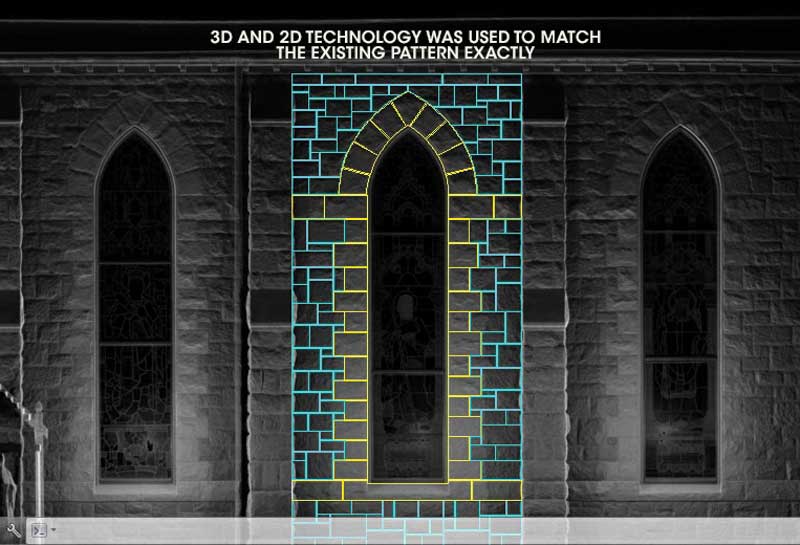
Image courtesy Coldspring
To replicate the twisting pattern of the 120-year-old stones, the granite fabricator employed 3D scanning technology. A complete scan of the church produced a 3D model, which was then converted into the 2D documents, in turn used to trace the pieces. Next, the fabricator used the 2D drawings to create a 3D model. These extensive efforts ensured the new façade would replicate the existing one with accuracy.
Despite the advanced scanning technology, some details could not be detected from the outside of the church. For example, some areas of the building were not visible from the ground, where the scan was performed. To meet this challenge and fully duplicate the pieces, photos and field measurements were taken. Piece size and joint variations were reconciled during the drafting process.
This technology was essential when looking for replication of an existing appearance in a restoration project. The other option would have been to provide blanks or sticks to the jobsite and have everything cut to fit onsite. However, with lack of space and continued use of the church, this was not a viable option; the staging area for this project was a small parking lot.
In total, 6706 granite pieces—each measuring 65,550 mm3 (4 ci)—were produced and installed at St. Francis of Assisi, which was completed in May 2016. Bishop Francis DiLorenzo celebrated with a mass to commemorate the renovation’s completion. The years of planning, fundraising, and execution were worth the wait, and St. Francis remains one of the most beautiful structures in downtown Staunton—a heritage preserved for many years to come.
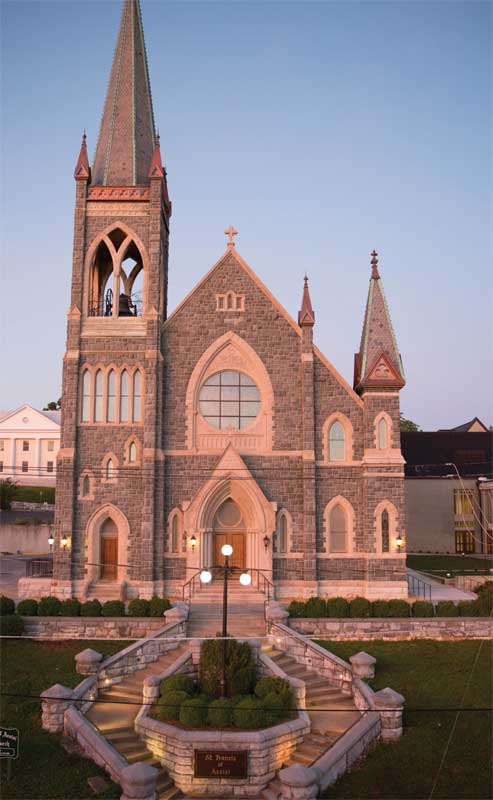
Photo © Tim Hoysradt Photography
Modeling and CNC shape museum hardscape
In September 2016, after nearly 10 years of planning and fundraising efforts, the Smithsonian Institution opened its new museum in Washington, D.C. The National Museum of African American Culture and History (NMAAHC) is the only museum dedicated to documenting the history, lives, and culture of African Americans. It features granite hardscape elements, which relied on 3D modeling technology and CNC fabrication.
Located on a 2-ha (5-acre) site on the National Mall—between the National Museum of American History and the Washington Monument—the museum encompasses 29,970 m2 (322,600 sf), with five levels above-grade and four below.
The museum’s design is distinctive among other structures on the National Mall. Its façade consists of 3600 customized, cast-aluminum panels known as the Corona. These bronze-colored panels call to mind the craftsmanship of enslaved workers in the pre-Civil War cities of Charleston and New Orleans, and create a distinctive impression for NMAAHC, representing traditional African architecture. Three architecture firms—the Freelon Group, Davis Brody Bond, and SmithGroup—worked on the museum.
Just as the museum’s architecture makes a unique design statement, its landscape design also distinguishes it among nearby museums and monuments, incorporating it into the larger configuration of the National Mall. According to GGN, the project’s landscape architect, “The site is designed to encourage visitors to extend the museum experience outside and to linger and reflect on the important narratives being told within.”
Granite played an important role in meeting the project’s design goals, about 3437 m2 (37,000 sf) of black granite in various finishes was used for hardscape elements such as paving, wall facing, wall coping, steps, curbs, benches, and bollards. Most of the stones for the project were modeled in 3D software, which allowed the fabricator to coordinate with the landscape architect and ensure the designs met expectations. Due to the project’s complex nature, an extensive amount of coordination between the fabricator’s drafting team and the architect was needed to ensure the 3D models were accurate before fabrication. Once the design team approved the fabricator’s drawings and models, the fabricator converted them into a file for use on a five-axis CNC machine.