
by Lawrence E. Keenan, PE, AIA and Robert A. Marsoli Jr., EIT
Elastomeric traffic-bearing membranes have soared in popularity over the past decade. But, what should designers know before specifying one at a parking facility?
It is true parking decks must be protected from the harmful effects of moisture and chlorides, but there is a growing misconception installing a traffic-bearing membrane is a one-way ticket to the garage equivalent of immortality. While a traffic-bearing membrane may be the best option for many situations, it is a big-ticket item, and thorough consideration is necessary to determine whether this costly investment is suited to the garage’s needs.
In order to withstand the punishing abrasion which a parking deck must endure, the traffic-bearing membrane must be hard and durable. At the same time, the membrane must be soft and flexible to bridge over moving cracks and joints without failure. However, traffic-bearing membranes are not perfect. Since hard membranes are generally inflexible, and more pliable membranes do not hold up well to abrasion, choosing the right membrane is a balancing act. Additionally, there are locations where no membrane performs well, such as those areas requiring a flexible membrane, yet are subject to snow plows.
Identifying product properties and applying appropriate selection criteria can guide the specifier in developing a customized system that will provide immediate protection, while also considering future treatment options.
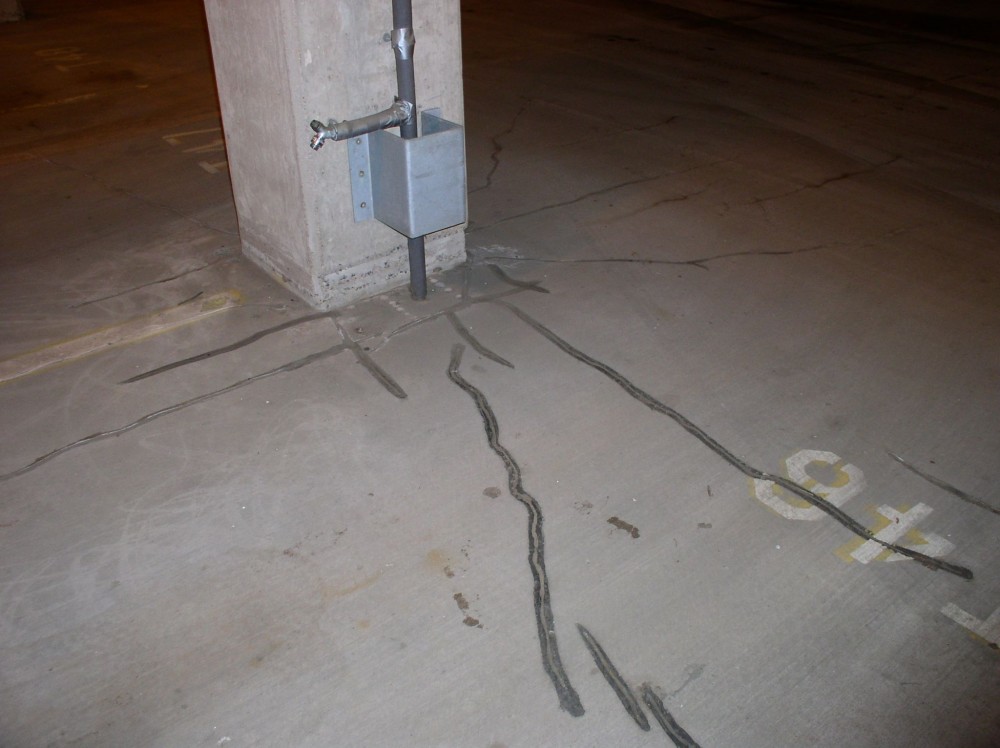
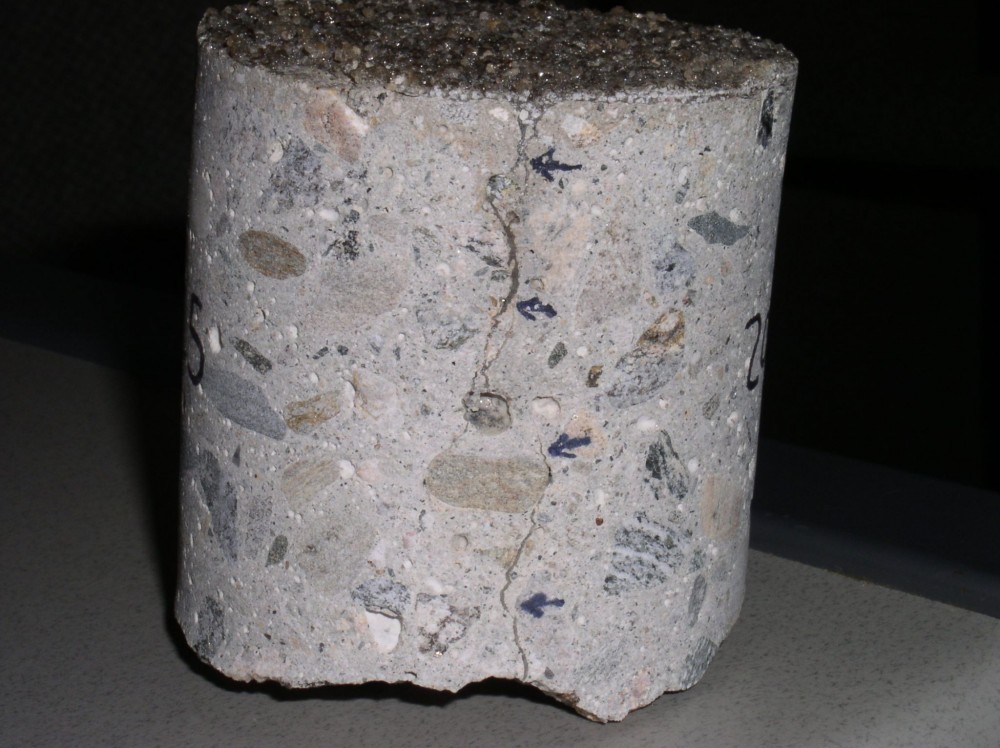
bottom of a crack, as indicated by the arrows
on the concrete.
Sources of deterioration
Since the interior and exterior of parking structures are exposed to the elements, they are more susceptible than other types of buildings to deterioration due to moisture, temperature cycles, and contaminants. Even the best designed and constructed garages need help to survive this onslaught of corrosive forces.
Water is at the heart of most parking deck deterioration. Moisture can facilitate reactions between certain aggregates and alkali hydroxides in the concrete, creating a cycle of expansion, cracking, and further moisture intrusion. Alkali-silica reaction (ASR) is difficult to stop once it has developed. Other minerals, notably sulfates, migrate via penetrating moisture and can lead to formation of gypsum, which can lead to softening and loss of concrete strength, and ettringite, a crystalline mineral the formation of which can result in an increase in solid volume, creating expansive forces that cause cracking and a loss of cohesion and strength in the concrete.
In northern climates, parking decks are subjected to extreme corrosive and deteriorating environments. Moisture, laden with chlorides from de-icing chemicals, tracks into garages and ultimately soaks into the concrete surface. The dissolved chlorides then migrate to embedded steel reinforcement through the pores in the concrete or penetrate through cracks. Once they reach the steel, the salts cause expansive corrosion, ultimately resulting in unsightly, destructive, and costly deterioration.
Moisture’s ability to transport corrosive chlorides is not its only damaging property. Coupled with cold weather, water can damage concrete decks as it expands and contracts during freeze-thaw cycles. Air entrainment, the deliberate incorporation of microscopic air voids in concrete, releases the internal pressure created by freezing water by permitting moisture to flow from void to void. Although this solution to freeze-thaw degradation has been known for years, garages may inadvertently be constructed with insufficient air entrainment, leading to premature concrete breakdown as freezing water destroys it from the inside out.
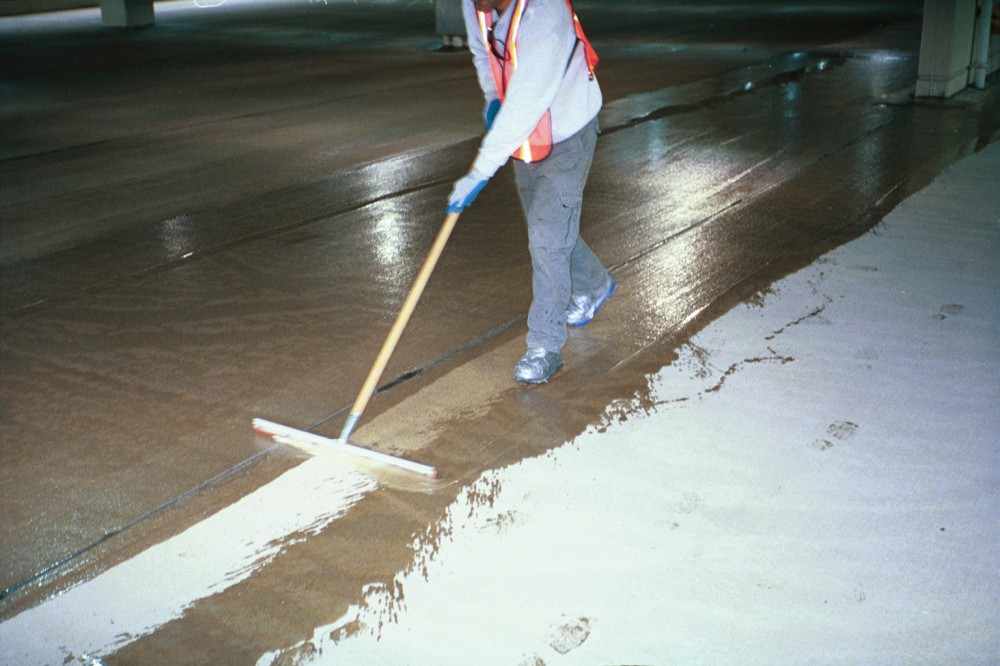
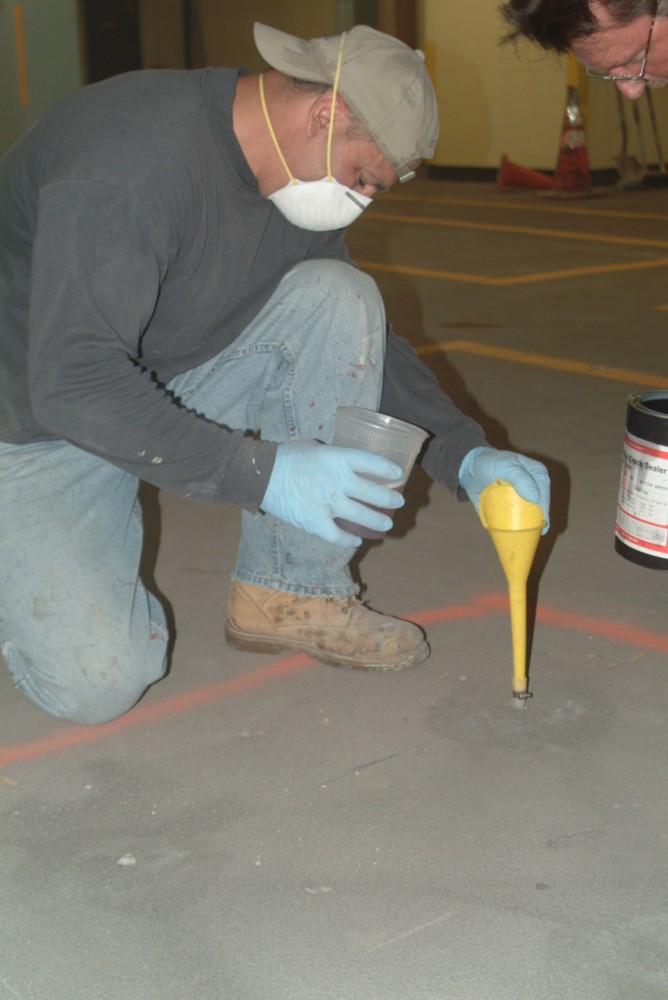
Deck protection: product types
Technological advances in the chemical industry over the past 30 years have brought concrete sealers a long way from the boiled linseed oil previously used. Today, an industry dedicated solely to concrete protection offers a dizzying array of products to treat concrete before, during, and after production.
Ultimately, the goal of parking garage protection is to stop water from getting into the deck. This may be an over-simplification, but no water means significantly reduced deterioration. The tricky part is water comes in multiple forms. Liquid water is an obvious ‘villain,’ as is the expansive force of ice and snow, but water vapor can be just as damaging.
For example, a chloride-laden deck can actually draw moisture from the air and continue to deteriorate even after the best efforts to keep it dry. In fact, calcium chloride, the most popular and effective of all de-icing chemicals, is commonly used on construction sites for dust control. It is sprinkled onto the dry earth and wets the surface by pulling moisture from the air. Unfortunately, it works equally well at saturating a parking deck.
Remediating the effects of chloride ion attack, freeze-thaw damage, or moisture-driven chemical reactions is both difficult and costly, so preventing any type of water infiltration is a priority. While keeping a garage perfectly dry is an impossible task, through thoughtful product selection, the degree to which moisture can penetrate the parking deck can be limited. For existing parking structures, numerous waterproofing agents that can be applied to the deck’s surface are available.
Penetrating sealers
These liquid-applied treatments, which include silane, siloxane, and silicates, stop water entry by penetrating deep into concrete and forming a barrier that prevents water from entering, limiting chloride ion migration and freeze-thaw damage. These treatments are also vapor-permeable, allowing them to be used at locations where other coatings may be inappropriate, such as slabs-on-grade. Since they are inexpensive and quickly applied, with little or no down-time, penetrating sealers offer a good first line of defense for a parking structure that is in good overall repair. As invisible penetrants working below the surface, these sealers do not affect deck line striping, saving on project duration and cost.
However, these coatings can be short-lived solutions, requiring reapplication every five years or less. They also do not bridge cracks, so they only limit moisture and chloride penetration in intact concrete. Since cracking can be an ongoing process, the ability to bridge new cracks as they form may be important in parking decks that already have evidence of concrete distress.
Methacrylate and epoxy healer/sealers
These coatings both repair cracks and seal pores, so they can be used to restore a deck that has already undergone some deterioration. Low-viscosity methacrylates and epoxies fill the pores in concrete to create a barrier to liquid-water-driven chloride intrusion. They can also be injected or gravity-fed into cracks to structurally heal them. Where desirable, healer/sealers can also limit vapor transmission, although care must be taken not to lock moisture within the deck.
Moderately priced, this class of surface treatments offers a good solution for parking structures starting to show some signs of distress, both to treat deterioration that has already occurred and to prevent continued water-related damage.
Where methacrylate and epoxy healer/sealers fall short is in wet or soiled fractures (to which the materials will not adhere) and moving cracks (which are likely to re-fracture). On parking decks exposed to continuous sunlight, epoxies can degrade quickly under ultraviolet (UV) radiation, so methacrylates should be considered for these areas.
For enclosed parking structures or other areas where fumes might be a problem, offensive odors from methacrylates might prove prohibitive. Unlike the penetrating sealers, healer/sealers are not just ‘coat-and-go;’ surface preparation necessitates shot-blasting, which means increased down time and cost. Also, pavement markings must be reapplied.
Traffic-bearing membranes (elastomeric)
In parking structures with dynamic cracking, shrinkage, or more advanced damage, a traffic-bearing membrane may be the only option to address the ongoing deterioration. Unlike the sealers, these do not penetrate the concrete, but remain on the surface to create a barrier that locks out moisture and chlorides. Most elastomeric membranes have two layers—a base coat that provides the waterproofing protection, and a top coat, which protects the base membrane and provides skid resistance. Together, these yield an attractive, easy-to-clean surface that can give a ‘face lift’ to older, crack-riddled parking decks.
However, a traffic-bearing membrane’s assets are also its downsides. Flexible varieties offer superior crack-bridging, even for moving cracks, but they do not hold up well to abrasion because they are soft and yielding. More rigid varieties, designed to better withstand abrasive forces of heavy traffic, are too stiff to bridge these moving cracks. So while traffic-bearing membranes, as a class of surface treatments may seem to have the ideal combination of properties, in practice no single membrane actually does. Before specifying one of these coatings, the lengthy down-time required for preparation and application, and considerable ongoing maintenance of re-coating or top-coating every five to 10 years, should be considered. Once a traffic-bearing membrane has been installed, it is nearly impossible to return to an uncoated surface in the future.
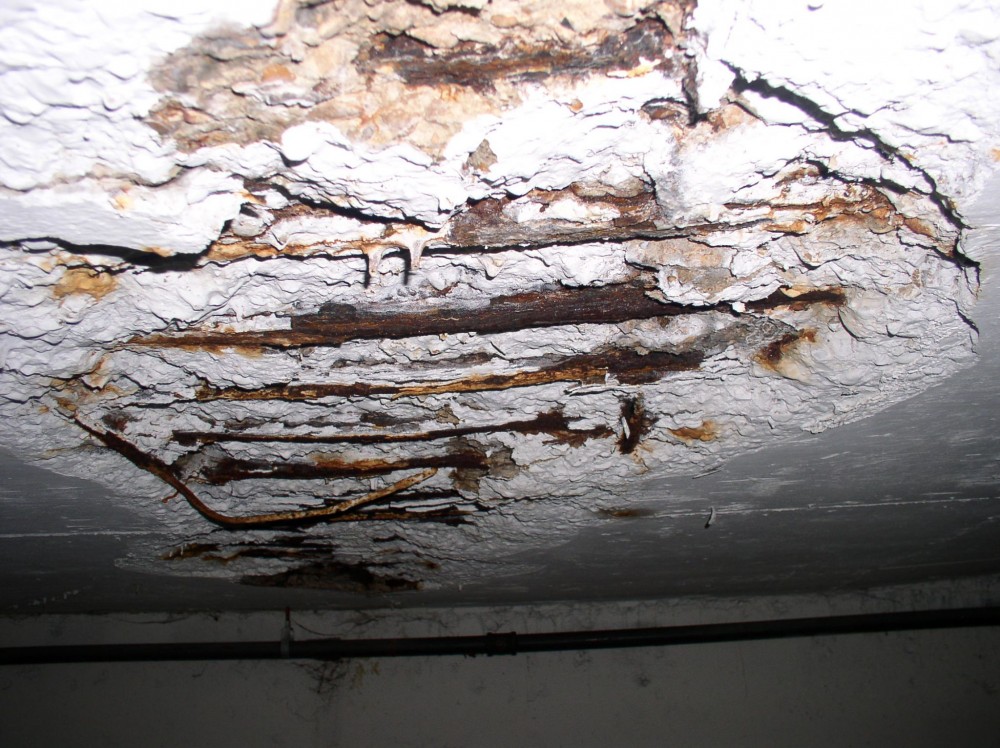
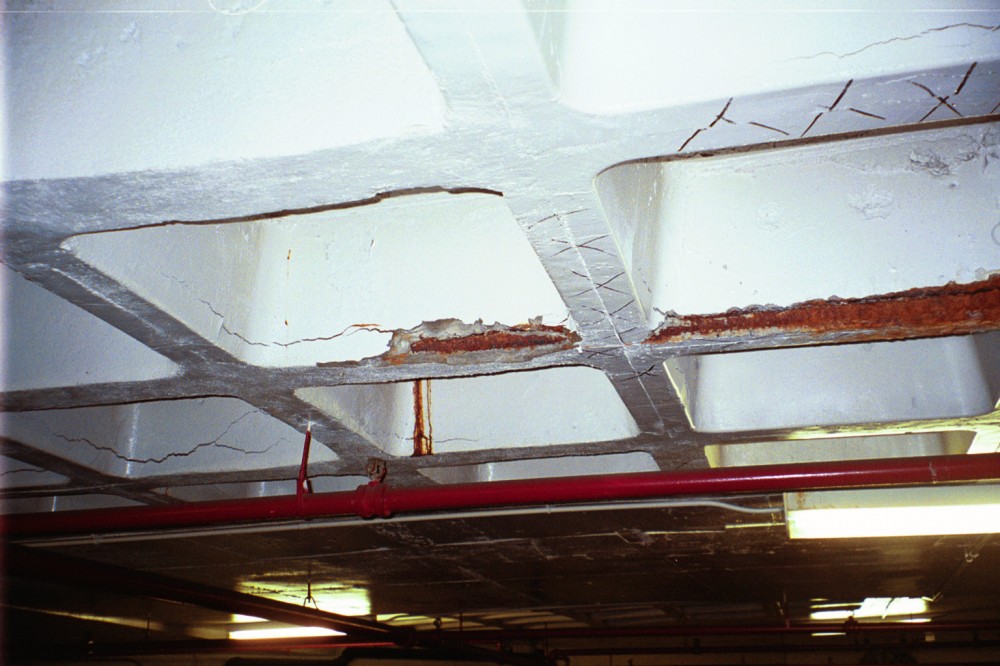
Cast-in-place vs. precast
To select the best of the available surface treatments for the parking structure’s characteristics, condition, and situation, designers should consider numerous criteria to determine which products offer the best-performing option for the cost, in terms of both initial investment and long-term maintenance.
Over the years, many different types of parking decks have been developed. For the purpose of investigating surface treatment options, deck types can be simplified into two basic categories: cast-in-place and precast concrete. Usually composed of a single, contiguous, reinforced slab of concrete spanning a concrete or steel frame, cast-in-place decks are constructed onsite.
Due to its nature, concrete shrinks as it cures, which coupled with the external restraint stress from the structure to which it is attached, can lead to crack formation. Cracks are water-borne chlorides’ direct route to reinforcing steel. Once established, these cracks form natural expansion joints that open and close with changing temperature and humidity.
Consequently, protective techniques tend to focus on these moving cracks. If cracks are few and the deck is chloride-free, then routing and sealing, and applying a low-cost sealer, may be appropriate. If the deck is riddled with cracks that cannot be adequately sealed, then elastomeric membranes can begin to look like a good option.
Cast off-site under controlled conditions, precast decks are lifted and welded into place after they have cured and partially dried out. Since the concrete used for this type of construction is typically high-strength and denser than its cast-in-place counterpart, precast decks should rarely experience cracking. However, this manner of construction is favored for fast-track projects, and the end result is rarely defect-free.
As these materials are factory-made and must be lifted into place, precast units do not create a single, contiguous, monolithic structure. Instead, the individual members meet at sealant joints. Extending around each precast unit, these joints add up to miles of sealant that must be maintained and periodically replaced. Even if cracking is not an issue, water migration through failed joints can be just as damaging.
Aside from routine sealant maintenance, surface protection requirements are typically minimal and can usually be addressed with simple low-cost penetrating sealers. Heavily cracked decks may be routed and sealed or treated with rigid epoxies or healer/sealers, since these cracks are typically non-moving. However, the precast deck’s irregular surface does not readily lend itself to flexible membrane-type coatings. The leading edge of each panel quickly becomes a wear point, bumping against automobile tires or catching the tip of a snow plow. Protection techniques that soak into the deck and keep the concrete as the wearing surface are preferred.
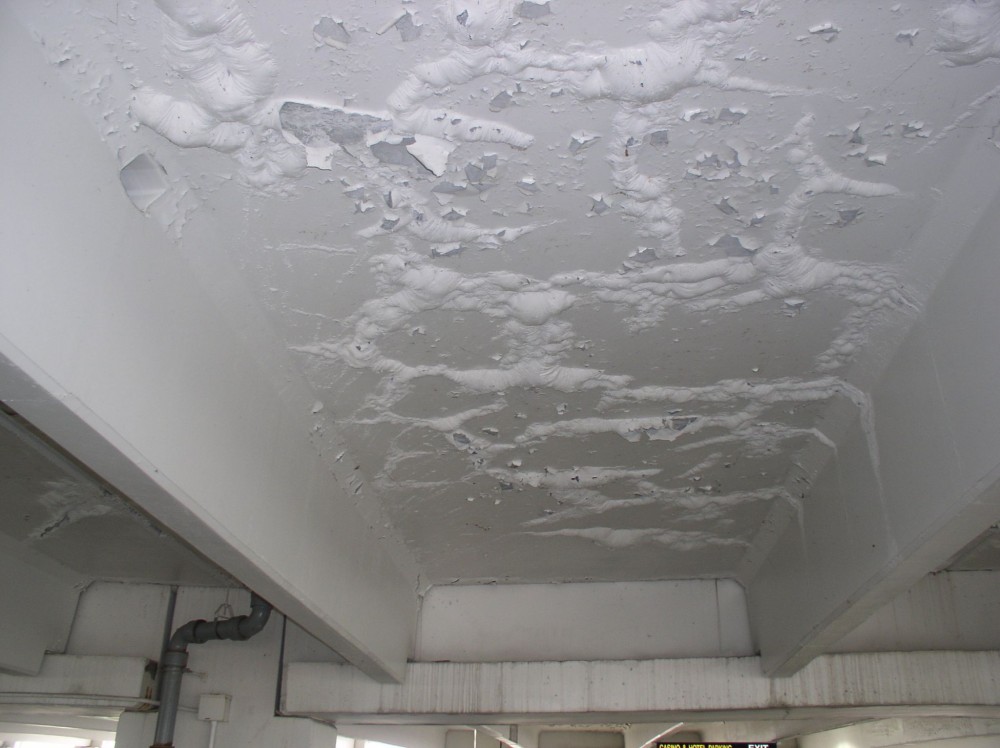
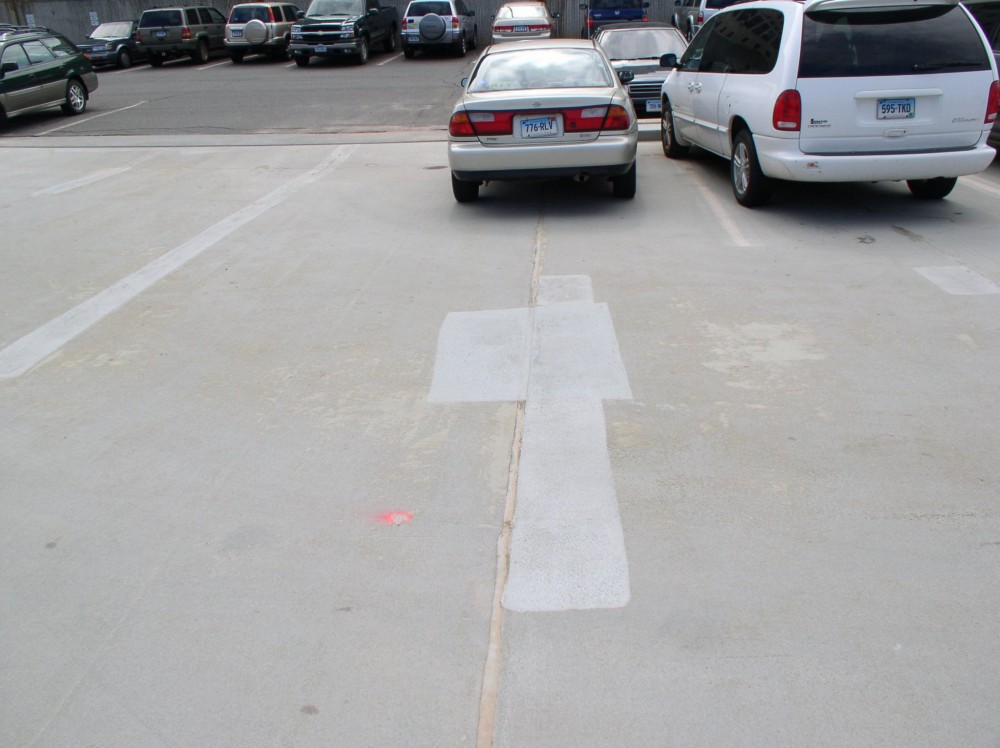
repair damage from snowplow blades.
Concrete quality and condition
Knowing the concrete quality offers insight into the type of deterioration to which it would be most susceptible. This is usually achieved by ordering a petrographic analysis of a test sample. A petrographic analysis is an extraordinarily useful tool in determining what is wrong with concrete or predicting what can go wrong in the future. This analysis can detect most durability issues, so the most appropriate level of protection can be selected.
Chloride content is determined by removing concrete samples from varying depths and analyzing them in a laboratory. If chlorides are moving through the concrete quickly, the deck protection system must be aggressively enhanced to stop further migration. If the chlorides have reached the level of the reinforcement, chances are deterioration has already begun and low-cost sealers are no longer an option. Deck protection that retards water vapor intrusion or effectively inhibits corrosion is now necessary.
Age
While there is nothing inherently wrong with old concrete, the life of a deck does tend to follow a natural progression. Unless design or installation defects are an issue, a new deck can be effectively treated with low-cost sealers that limit the intrusion of chlorides through the concrete. Further along in the life of the deck, a more positive barrier, such as a moderately-priced epoxy sealer, may be necessary to retard moisture entry.
Ultimately, if not properly protected, a deck may require a traffic-bearing membrane to provide the best defense. However, as these membranes are costly and require maintenance and periodic reapplication, waiting to address signs of trouble until there are no other options is not the best course of action. Once a deck has begun to deteriorate, the coating can only retard further deterioration, not stop it.
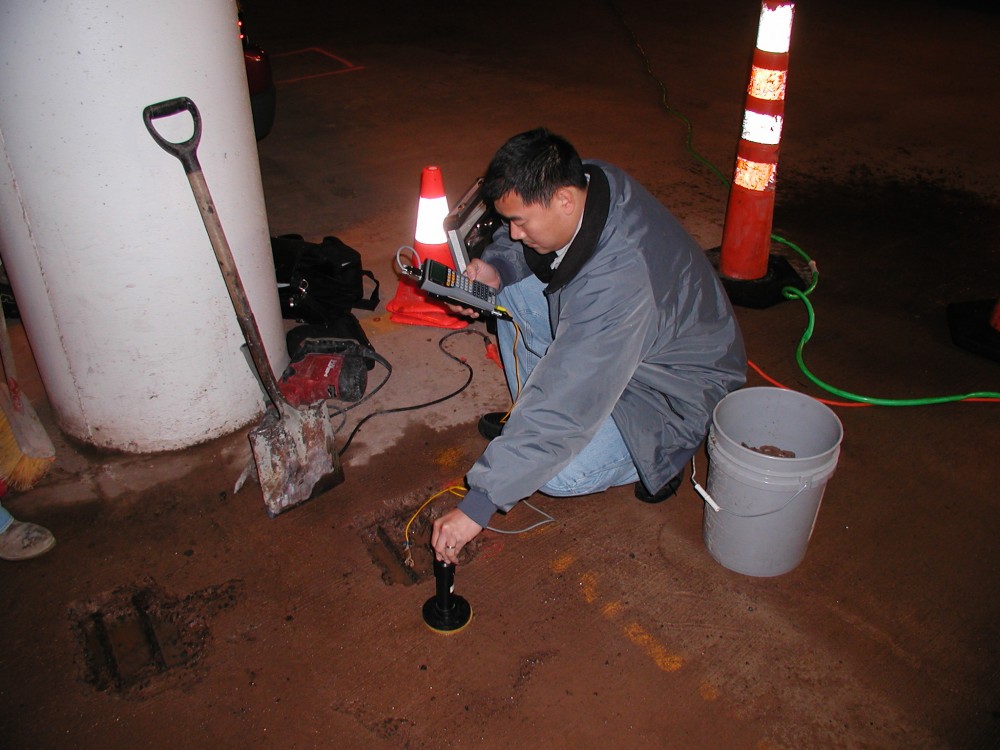
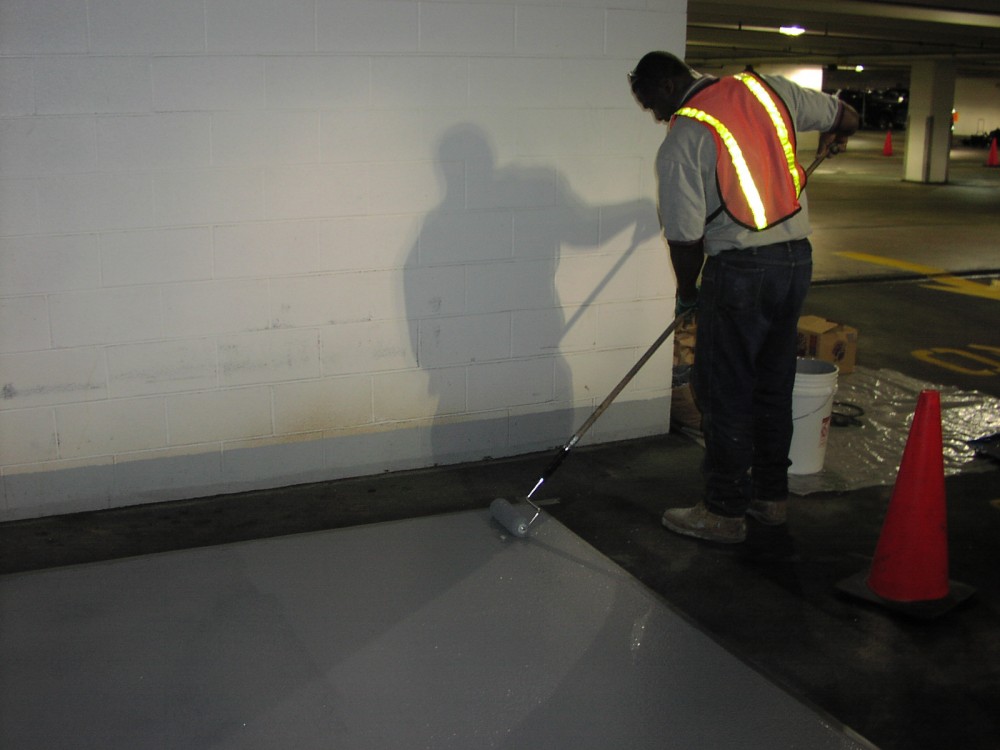
Exposure
Whatever protection system is employed, it must withstand the rigors of its environment. UV degradation may be a problem for some coatings on a top deck. Epoxies, in particular, have difficulties when exposed to direct sunlight. Soft, flexible membranes may not withstand abrasion in high-traffic garages or on a typical turning radius and will fare poorly against snowplows. For example, a coating that looks ‘like new’ after many years in an apartment garage may not withstand a year at an airport or shopping mall.
The damage that can be inflicted by snow removal should not be underestimated. Many coating warranties require snow removal equipment to have rubber tips; others do not cover snowplow damage outright. Unless the garage management operates its own snow removal equipment, coatings at exposed decks will likely encounter a steel plow blade at some point in their service life. There are coating systems tough enough to repel the steel tips, but these super-rigid coatings do not bridge cracks. The best solution depends on finding the right compromise between rigidity and flexibility for a specific situation.
Location
As the adage goes, location is everything. Knowing which surfaces in a parking structure can accept an impermeable coating and which are best left bare is critical to prolonging the life of a garage.
A coating successfully applied to an elevated deck may have disastrous effects in the same garage when applied to a slab-on-grade. As water levels and humidity change, ground moisture seeps up into the concrete slab. Vapor barriers, often installed under slabs-on-grade, are designed to block this moisture from entering the slab. However, in reality, breaches in the barrier or cracks in the slab can still permit water entry. If an impermeable coating is applied to the top surface of the deck, that moisture becomes trapped between two impenetrable surfaces. Unable to escape, the water sits in the slab, leading to chloride and freeze-thaw degradation. Even without a vapor barrier, moisture in the ground rises within the slab and becomes trapped within the deck. Therefore, leaving the slab-on-grade uncoated is the best course of action.
On an elevated deck, that permeability gradient is reversed. Moisture enters the deck from above and migrates through the slab to the underside, where it evaporates. Even with a waterproofing membrane protecting the top surface, the deck is still susceptible to water entering at cracks, joints, and failed coating sections. Coating the bottom of the deck with an impermeable coating invariably leads to trapped moisture and accelerated deterioration. For this reason, the underside of an elevated deck should be similarly treated to a slab-on-grade and left uncoated.
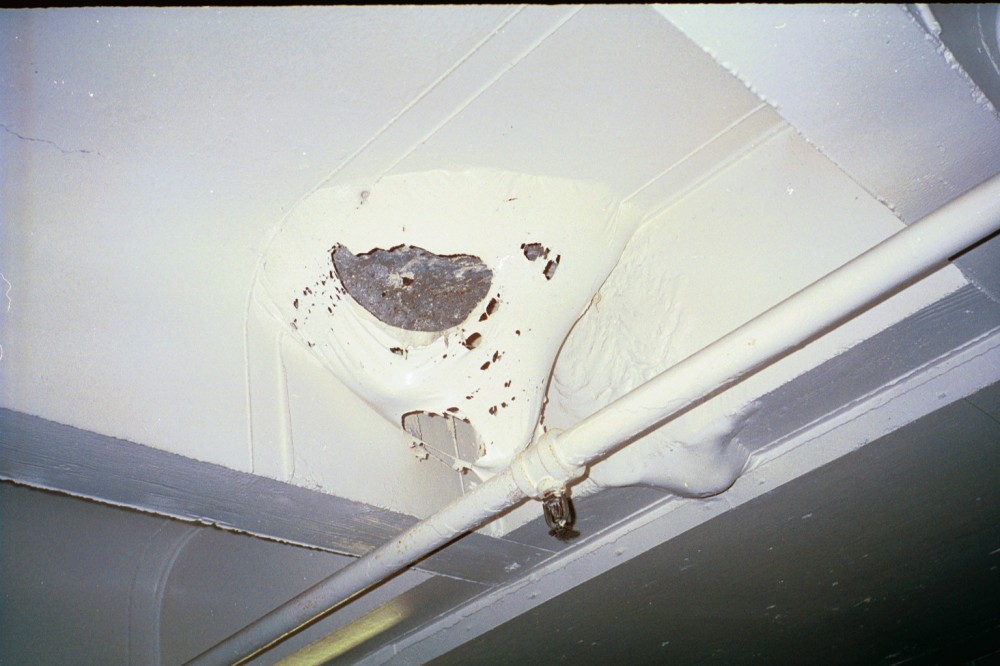
aesthetically unsightly.
Cost
While the saying ‘you get what you pay for,’ can be applied to surface protection as well as anything else, in terms of quality material selection and skilled application, it is also true lower-cost systems are usually lower-maintenance alternatives. If an inexpensive sealer would suffice, installing a traffic-bearing membrane because it is the high-end option may mean investing in a costly system that may not perform any better in that situation. Additionally, once the membrane is in place, it must be maintained and eventually replaced.
Aesthetics
While a simple sealer can help prevent water infiltration, it will not change the parking deck’s appearance. On the other hand, an elastomeric membrane transforms the look of the garage and provides a uniform, fresh-looking surface that is easily cleaned of dirt and stains. For a crack-riddled older garage, this can be a welcome change. In a newer garage, however, the existing concrete surface is likely fine.
Using paint on the underside of a deck to improve its appearance can have problematic effects, since paint is a type of coating. Many of the concrete paints on the market are epoxy-based and relatively impervious to moisture. Even if a vapor-permeable paint is used, successive reapplications increase the coating thickness and so decrease its permeability. Over time, what was once a high-permeability surface can become surprisingly resistant to moisture migration. With the eventuality of peeling paint, spalls, rust, and cracks taken into account, a deck underside painted only for aesthetics begins to lose its appeal, as compared with a simple, uncoated one still intact.
Coating compatibility
Not all surface treatments are compatible. The parking deck protection specified now may limit future options, so both immediate performance goals as well as long-range planning should be considered before committing to a coating. Any applications already in place should also be investigated.
A ‘quick fix’ to get through the winter, for example, might be a less-restrictive sealer that penetrates the slab—rather than one that coats the surface—because various surface treatments can be applied over it in the future. Epoxy healer/sealers can cover such penetrants, and they provide a good base for membrane systems, should one be installed, down the road. However, once a traffic-bearing membrane is installed there is no way to effectively remove it without damaging the slab surface.
Proper application
Even if the right surface treatment is selected for a given project, problems can still result when the application is not executed correctly. Certain coating deterioration issues—such as delamination and blistering—may be avoidable if care is taken in surface preparation and coating techniques.
Before any coating is applied, surface defects must be corrected in order to create a sound substrate for coating application. Any dirt, dust, grease, paint, or other foreign matter should be cleaned, and surrounding areas protected. To prepare concrete for a penetrating sealer, procedures such as power-washing are often used, wherein high-pressure water or steam, sometimes mixed with mild detergents, forces dirt off an exterior surface. Other methods include hand-scrubbing and simple vacuum or broom cleaning. To prepare the deck surface for healer/sealers or traffic-bearing membranes, shot-blasting is required.
It is crucial to wait a minimum of 24 hours following any kind of water washing before applying a coating, in order to allow the deck to dry sufficiently. Cleaned surfaces should be tested for moisture at various sites just prior to application. If excess moisture remains, the coating may trap it inside the parking deck, exacerbating any water-related deterioration. A damp surface can also cause adhesion problems.
In weather conditions such as extreme heat or cold, wind, or rain, the area must be protected and coatings should not be applied. One must also avoid coating in direct heat of sun, as this may result in rapid drying of the material and cause bubbles or wrinkling. It is important to check the specific temperature range recommended by the manufacturer, as these vary from product to product. Also, keep in mind checking the ambient temperature may not be sufficient as surface temperatures may be significantly hotter or colder.
Conclusion
The preferred protection techniques stop deterioration before it begins. If a parking deck is well-maintained from the start, with sealers applied early and cracks promptly addressed, then surface treatment choices can evolve over time as the garage ages and needs change. However, if conditions are such that distress is advanced and progressing rapidly, more immediate and aggressive action must be taken to slow deterioration and minimize its impact.
Before specifying a concrete coating, one should consider the parking deck type, concrete age and quality, and level of exposure to traffic and weather. A surface treatment must not be specified until the garage’s condition has been assessed through investigation, testing, and evaluation. This can help navigate the array of available coatings. The right parking structure protection program should not only protect the deck today, but also anticipate the maintenance needs of tomorrow.
Lawrence E. Keenan, PE, AIA, is the director of engineering with Hoffmann Architects Inc., an architecture and engineering firm specializing in the rehabilitation of building exteriors. He has extensive experience in parking structure rehabilitation, including investigation, repair, and surface treatment consultation. Keenan can be contacted by e-mail at l.keenan@hoffarch.com.
Robert A. Marsoli Jr., EIT, is a project manager at Hoffmann Architects and has developed remediation solutions for a number of parking garages, from design through administration. He also provides preventive treatment consultation services for new construction. Marsoli may be reached at r.marsoli@hoffarch.com.
I have worked really hard on my editorial. I have tried a new method for prewriting—I have a bunch of different things in Word for different parts such as opposing arguments, topic sentences, and others.
I know that at my work, the lines in the parking garage are pretty much gone. You really have no idea where the parking stalls are. So having someone come in and touch up on those lines would be very beneficial to a lot of people in the company. I will make sure I let my boss know about this.
It’s interesting to read about common problems with older concrete. It makes sense that as concrete ages, there is a higher likelihood of something bad happening in it. It’s something to remember for the parking garage because getting a new barrier and sealing the concrete could make it look nice, but the concrete should be checked to make sure it’s not breaking apart.
Choosing the right garage floor applications need a considerable attention to prevent trouble later on. Epoxy and/or polyurea polyaspartic coatings are the choice of many here in Seattle, WA. Glad that I had my garage floors resurfaced with epoxy coatings.
Btw, it was good to see that this kind of pretty informative article available online. Thanks for sharing this!
All mentioned above are the reasons why I decided to have an epoxy garage flooring contractor. I thought of doing it myself but good thing I didn’t. Asking for a professional to help you in your concrete is really important to prevent further damage (and expenses).
Ive been asked by a client about removing snow from a membrane surface. Does anyone have any expierence with this or know what I should use? Or is a rubber tipped blade my only option?