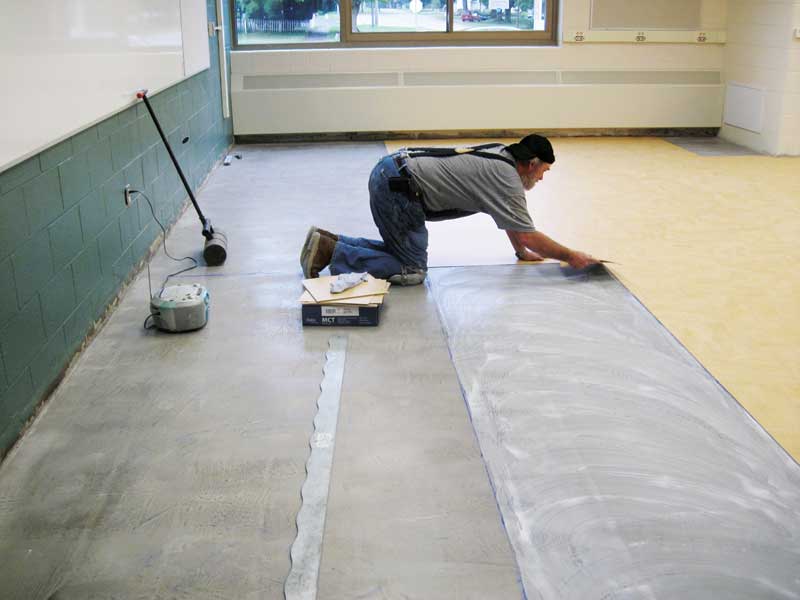
by Paul Potts
There are two major sources of moisture in fresh concrete—excess mixing water left over after hydration of cement, along with natural groundwater beneath the concrete that moves to the surface by capillary action. This article describes how to control the sources of moisture in concrete slabs, minimize drying wait time to meet floorcovering manufacturer’s requirements, and determine when the slab meets those requirements.
Concrete is a combination of cement, water, and aggregate; the specific proportions are called the mix design. When water and cement are combined, a chemical reaction called hydration occurs and then continues as long as there are particles of cement and new water to feed the process. Curing concrete is the procedure for keeping water in the concrete to prolong hydration until the optimal qualities of concrete have been realized. The longer the curing process continues, the better the concrete.
Excess water (i.e. what is needed for hydration) is figured into the mix as an aid in placement. If this excess water is not added, the concrete will be too stiff to place economically. Once hydration has progressed far enough to produce the desirable qualities of hardened concrete, the excess water must be allowed to evaporate for the concrete to become dry enough for moisture-sensitive floorcoverings. This is called the drying stage. Together, curing and drying equal the interminable ‘wait time.’
The excess water gathers in the pores of the concrete, first as water when the concrete is wet, and then as water vapor that produces a level of relative humidity (RH) in the concrete. (For more, visit www.59.167.233.142/publications/pdf/Moisture.pdf). The RH of concrete is a good barometer of when the concrete is safe for moisture-sensitive floorcoverings, such as vinyl tile, resilient sheet flooring, linoleum, vinyl-backed carpet, and cork and wood flooring.
During the drying stage, excess moisture evaporates at the surface of the concrete, while moisture deeper in the slab moves up near the surface, where it too gets whisked away by an exchange of relative humidity. The drying stage is a straightforward process—assuming there is no groundwater replenishing the moisture in the slab, nothing is atop the slab preventing evaporation, nothing is rewetting the concrete from the surface, and the ambient air humidity is less than the humidity in the concrete. As long as adverse factors are absent, the wait time for the concrete to dry is directly related to the water-cement (w/c) ratio and the RH around the concrete.
Water-cement ratio and total water
The w/c ratio and the total water content have the most direct effect on the amount of excess water that must evaporate before moisture-sensitive floorcoverings can be applied. The w/c ratio is the weight of water divided by the weight of cement in a unit of concrete. Wait time can be reduced significantly by specifying a low w/c ratio and using less cement. Low water-cement ratios and less cement decreases the amount of mix water and, thus, reduces drying time. Excess water can also be reduced by using the largest recommended graded coarse aggregates.
A water-cement ratio of 0.45 is optimal for slabs on grade. It produces high-quality concrete with shorter drying times. A higher ratio of 0.50 increases long-term shrink cracking and can take a month longer to dry to the floorcovering manufacturer’s requirements.
Concrete with a w/c ratio of 0.45 will be quite stiff coming off the truck and the contractor may want to add a plasticizer for convenience. However, under no circumstances should extra water be added onsite.
Six sacks of concrete (40 kg [94 lbs] per sack) for commercial building slabs on grade is unnecessary if 5.5 sacks will suffice. More cement at a given ratio requires more water, adding to the drying wait time.
Many architects and engineers are not practiced in specifying concrete by the water-cement ratio formula, so they specify strength and slump alone. Contractors bidding the project should check the cast-in-place concrete specification and the structural drawings for the water-cement ratio. If it is not stated, they should bring it to the attention of the architect-engineer during a pre-bid or pre-award conference.
Good explanation of the drying process for concrete foundation. It’s good to know the proper water to cement mixture. Thanks for sharing!