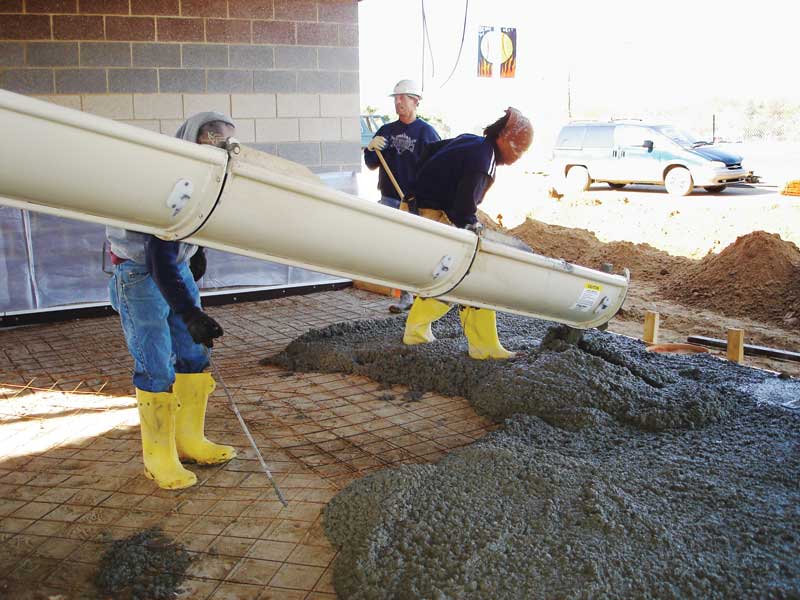
Photos courtesy Paul Potts
Retarders and barriers
Moisture from under the slab enters the concrete by capillary action—the ability of a liquid to flow in narrow spaces (pores) without the assistance of, and in opposition to, external forces like gravity. Moisture entering the concrete from under the slab will make it almost impossible to get the concrete dry enough for moisture-sensitive floorcoverings.
If groundwater is present in the building footprint, the architect-engineer should design subsurface drainage to route the water elsewhere. Regardless of flowing water or a high perched watertable, it is prudent to design for a moisture retarder in all circumstances, or manufacturers may void their warranties in the case of moisture-related problems.
American Concrete Institute (ACI) 302.1, Guide for Concrete Floor and Slab Construction, differentiates between vapor retarders and vapor barriers. Retarders are plastic sheets 254 µm (10 mil) thick, with a perm rating less than 0.2085 metric perms (0.3 U.S. perms). Vapor barriers are 381-µm (15-mil) thick plastic sheets with perm ratings of 0.00695 metric perms (0.01 U.S. perms). Almost all sheet vapor protectors used in the past have been vapor retarders by this definition.
In the past, moisture protection has rarely been carefully selected, placed, or maintained. However, with modern water-based adhesives substituting for solvent-based adhesives, floorcovering failures have become more financially threatening and have brought more attention to the proper installation of a sheet vapor retarder. Thicker sheets mean punctures caused by equipment or workers are less likely. Both careful installation and paying close attention to overlapping seams and holes in the sheets caused by infrastructure penetrations will ensure protection provided by the vapor retarder is more reliable.
The ACI 302 guide now recommends vapor retarders be placed directly under the concrete, with a cushion layer of sand between it and the aggregate subgrades. This sand cushion prevents punctures in the sheet and minimizes long-term shrink cracking in the concrete by allowing the slab to slip on the smooth surface without being restrained by the irregular aggregate.
To ensure proper construction of the vapor retarder, the 152-mm (6-in.) overlapped seams must be sealed with tape. This tape should also be used to carefully seal punctures and holes around piping and conduit. Even a small pinhole in the moisture retarder will be a continuous source of moisture in the slab.
Curing of concrete
Evaporation is the process by which water changes from a liquid to a gas or vapor. It is the primary pathway water uses as it moves from the liquid state to atmospheric vapor.
Making concrete requires the hydration of cement by exposing it to water and heat—the chemical reaction continues as long as there are cement particles in the presence of water. Curing prevents moisture from prematurely evaporating, keeping the chemical reaction going until the best qualities of hardened concrete are achieved.
After concrete starts to harden, the hydration process begins to slow down. However, if the moisture evaporates too quickly, hydration halts—leaving the concrete under-strengthened. Applied curing measures retain moisture in the concrete and must be kept in place until all the moisture required for developing the optimal characteristics of hardened concrete is used up, but the wait time for applying moisture-sensitive floorcoverings is increased by the same amount of time. The longer the curing measures are kept in place, the better the concrete; however, this also increases the wait time.
To minimize waiting, curing products and practices must be selected on the basis of their rewetting characteristics and the amount of time they keep the concrete sealed. In the case of slabs for moisture-sensitive floorcoverings, the curing products must dissipate or be mechanically removed to allow evaporation of excess water to begin. Curing products vary as to their rewetting characteristics and how long they must remain in place.
For this article’s purposes, curing methods can be divided into three classes:
- membrane-forming curing and sealing compounds per ASTM C 1315, Standard Specification for Liquid Membrane-forming Compounds Having Special Properties for Curing and Sealing Concrete;
- rewetting techniques, including continuous flooding of the concrete for seven to 10 days and absorptive covers kept continuously wet for the same period; and
- moisture-retaining covers of polyethylene film per ASTM C 171, Standard Specification for Sheet Materials for Curing Concrete.
Membrane-forming compounds are a problem because they persist for a long time—likely months—with a direct effect on the wait time. Some manufacturers advertise their membrane-forming compounds will dissipate in 30 days, but this only happens when the slab remains exposed to the sun.
Water flooding and moist burlap also have issues as they introduce additional water into the slab, rewetting the concrete. While all of these products and procedures make high-quality concrete, they complicate getting the floorcovering started.
Moisture-retaining polyethylene film—the ugly duckling of curing methods—is the most acceptable compromise between achieving adequate curing and meeting the long-term goal of installing the floorcovering on schedule. With this method, polyethylene sheets are placed on the top of concrete and weighted down against the wind. They are regularly maintained for seven to 10 days and then removed. Drying time begins once the polyethylene is removed.
After these decisions are made, construction practices begin to control the wait time. Rewetting the concrete by construction operations or exposure to the elements will replenish the moisture in the concrete and delay the start of the floorcovering. High ambient humidity in the space will also slow the drying process.
Good explanation of the drying process for concrete foundation. It’s good to know the proper water to cement mixture. Thanks for sharing!