
Wait time
Concrete that is 100 mm (4 in.) deep in an enclosed building with a recommended w/c ratio and properly installed vapor retarder under the slab with no rewetting complications will take three months or longer to be ready for moisture-sensitive floorcoverings. (For more information, visit www.concrete.org/portals/0/files/pdf/previews/302206_2pager.pdf).Thicker concrete will take even longer—up to one extra month more for each additional 25 mm (1 in.) of thickness. (“The Moisture in Concrete and Moisture Sensitive Finishes and Coatings” can be found online at www.59.167.233.142/publications/pdf/Moisture.pdf).
Once the building is enclosed, packaged refrigerant and desiccant dehumidifier systems are an effective means for accelerating the drying of concrete. Dehumidifiers reduce the RH in the space—drawing the moisture out of the concrete. Building HVAC systems can do the same if they are programmed for warm air that will absorb the moisture and then be passed over a cooling coil to release the water on the return cycle. Some HVAC systems are structured with a cooling coil ahead of the heating coil, with both coils working simultaneously. It also helps if the air is moving and not stagnant.
Moisture emission testing
Even though MasterSpec puts testing in the floorcovering sections, testing should be done by an independent agency under the direction of the architect, engineer, construction manager, or owner.
Once moisture evaporates from the coarse pores of the concrete, the RH falls to 80 percent, and unless the RH of the external environment is particularly low, the RH in the concrete will remain quite high over a long period—typically 75 percent, which equates to a moisture content of about ‘2.’ (For more information, visit www.water.usgs.gov/
edu/watercycleevaporation.html). For this reason, 75 percent concrete RH is a good point to start the floorcovering. One exception is parquet board, which requires a lower RH.
Any deviation from the manufacturer’s published testing requirements must be done with written consent of the manufacturer.
ASTM E1907, Standard Practices for Determining Moisture-related Acceptability of Concrete Floors to Receive Moisture-sensitive Finishes lists eight tests that may be used to determine moisture conditions of concrete. These procedures are divided into qualitative and quantitative classes. Tests in the first category merely check for the presence of moisture, but do not reflect any quantifiable amount. They are limited to reliably discovering moisture near the surface of the concrete.
Three of the qualitative tests and two of the quantitative tests have no ASTM reference standard and would be of little value protecting the project manager’s or contractor’s interests in the event of a failure. With respect to standing up as a defense in court, there is one qualitative test, ASTM D4263, Standard Test Method for Indicating Moisture in Concrete by the Plastic Sheet Method, and three of the quantitative tests:
- ASTM F1869-10, Standard Test Method for Measuring Moisture Vapor Emission Rate of Concrete Subfloor Using Anhydrous Calcium Chloride;
- ASTM F2170-11, Standard Test Method for Determining Relative Humidity in Concrete Floor Slabs Using in situ Probes; and
- F2420, Standard Test Method for Determining Relative Humidity on the Surface of Concrete Floor Slabs Using Relative Humidity Probe Measurement.
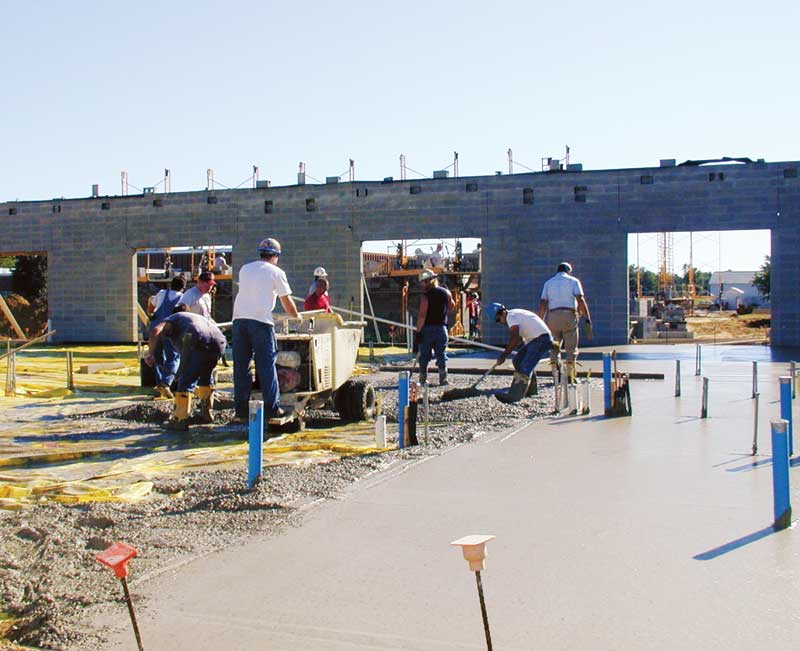
Most floorcovering manufacturers state their moisture requirements in quantitative terms. Nearly all have traditionally required results determined by the quantitative anhydrous calcium chloride test, described in ASTM F1869-10 (i.e. Moisture Vapor Emission Rate [MVER]). To protect the integrity of the results these tests should be done by a certified technician.
Moisture emission, RH, and pH testing combine to give the contractor confidence the concrete is ready for moisture-sensitive floorcovering.
More recently, manufacturers have begun requiring a panel of tests, including ASTM F1869-10 for MVER and ASTM F-2170-11 for RH. The latter tests for RH in the slab using an RH probe. Both these assessments require expensive equipment and should be completed by a trained technician working for a qualified, independent firm that can certify the results and testify in court if need be.
The MVER, RH, and pH tests are costly, and it is difficult to know when to start without wasting money on premature tests. The qualitative Plastic Sheet Test (ASTM D4263) is simple, reliable, economical, and does not require much training. This makes it a good screening test for determining when to start with more expensive quantitative tests. By itself, however, the plastic sheet test is not accepted by manufacturers.
Plastic sheet tests involve taping a 460-mm (18-in.) square of transparent polyethylene sheet tightly to the concrete, and sealing all edges with 50-mm (2-in.) duct tape. The plastic sheet is left in place for 16 hours and then removed. To be successful, the plastic sheet and the concrete should be dry to the touch and the concrete should not be darker than the surrounding concrete. The plastic sheet test is limited to testing for moisture in the top inch or so of the concrete and says nothing about the middle or bottom of the concrete.
Economical approach to testing
An economical approach to testing for concrete moisture content then is to begin early with the plastic sheet test, which will reliably screen without starting more expensive testing. Once the plastic sheet test comes up dry, it will be time to start professional testing with the quantitative calcium chloride test (ASTM F1869), the RH test (ASTM F2170), and the pH test (F2420). These should be done by trained personnel.
If the concrete has been placed and several months of drying time have passed, but the moisture rate emission is too high, it may be necessary (with the permission of the floorcovering manufacturer) to resort to post-construction alternatives. Moisture-retarding coatings, dispersive membranes, or combinations of these systems may be expensive, but they are acceptable under the circumstances.
Paul Potts is a technical writer and construction administrator. He has worked in the construction industry as an independent contractor and administrator for architects, engineers, and owners in Michigan. Potts can be contacted via e-mail at paulpotts1@comcast.net.
Good explanation of the drying process for concrete foundation. It’s good to know the proper water to cement mixture. Thanks for sharing!