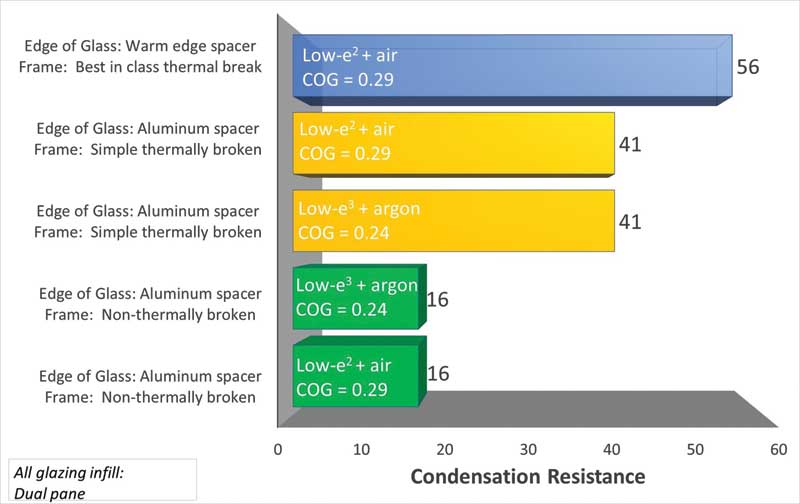
Condensation and thermal bridging: It’s all about the edge
Window Walls #3 and #5 in Figure 2 illustrate how condensation resistance (as shown using NFRC’s CR metric) is primarily driven by thermal bridging at the window’s perimeter. While both systems have approximately the same overall U-factor, Window Wall #3 achieves it through offsetting the high transmittance of a non-thermally broken frame with an extremely low COG U-factor (triple-pane). Window Wall #5 achieves the same U-factor by having a better, thermally broken frame and a more traditional, dual-pane low-e glass package. Due to thermal bridging through the non-thermally broken frame, Window Wall #3 has a lower resistance to condensation (i.e. lower CR) than Window Wall #5, which has the thermally broken frame.
Figure 4 shows the CR for five different window systems, comparing the relative impact of:
- frame type (non-thermally broken, thermally broken, and highest-performance thermally broken);
- EOG (aluminum versus warm-edge spacers); and
- COG (standard double-silver low-e, air-filled versus triple-silver low-e, argon-filled, dual-pane units).
This illustrates improving the frame and using a warm-edge spacer to reduce thermal bridging at the edge of glass are critical in obtaining better condensation resistance, whereas COG has a negligible impact.
Hospitals, laboratories, and projects where maintaining high indoor humidity is important have more stringent condensation resistance requirements than other building types. As an aid to designers, AAMA has created an online calculator to help determine an appropriate CRF specification for specific project needs.
High-performance frames
Based on the discussion of condensation resistance and whole-window U-factor, it is clear the frame is a significant determinant of fenestration performance. Heat flows through frames by conduction, convection, and—to a lesser extent—radiation, as illustrated in Figure 5. The standard method for reducing conduction in aluminum frames involves creating a separation between metal exposed to the building’s exterior and metal exposed to the interior, thus producing a thermal break. The bigger the separation between the two sides, the lower the effective thermal conductivity.
The two main types of thermal break are ‘pour and debridge’ and polyamide thermal barrier strips. (The two options were reviewed in a September 2016 article in The Construction Specifier—“Thermal Efficiency in Glazed Curtain Wall Systems,” by B. Mitchell, C. Ricker, and J. Schwabauer. Visit www.constructionspecifier.com/thermal-efficiency-in-glazed-curtain-wall-systems.)
Commonly known as nylon, polyamide is an inert, nontoxic material. Polyamide strips have a 40-year history of successful use in fenestration since their introduction in the late 1970s; an example of a simple thermal break is shown in Figure 6a. Since polyamide can provide the largest separation between framing members (exceeding 77 mm [3 in.]), some of the highest-performing fenestration systems use this type of material.
To reduce heat transfer by convection, polyamide strips can also be made into more complex shapes and used to prevent convection currents in extrusion cavities (Figure 6b). Various types of insulating foam can also be inserted into these cavities to reduce convection (Figure 6c). With conduction and convection mechanisms substantially reduced, some very high-performance systems in Europe now also include low-e coatings on the inside surfaces of the extrusions to reflect heat and reduce radiative heat loss.
To ensure appropriate strength, the polyamide strip material is glass-filled, with the fibers oriented in all three dimensions. As such, these strips have the capability of being used across all types of fenestration, including oversized and blast- and impact-resistant systems. Figure 7 shows an example of polyamide strips in impact-rated patio doors in the Hyatt House, Naples, Florida. With the airport on one side and the marina on the other, laminated IG was used for both impact and sound protection.
From an architectural design perspective, there are also other benefits of using polyamide strips. For example, they allow easy dual finishes (different colors, quality, and type) on the interior and exterior of the window (Figure 8). Further, they facilitate use of different glass packages (with different thicknesses) on a building without changing the look of the fenestration (Figure 9).
To ensure a polyamide strip system meets the required structural performance, regular shear testing should be done on extrusion assemblies as a quality assurance measure during manufacturing. Architectural specifications should also require compliance with AAMA Technical Information Report (TIR) A8, Structural Performance of Composite Thermal Barrier Framing Systems.