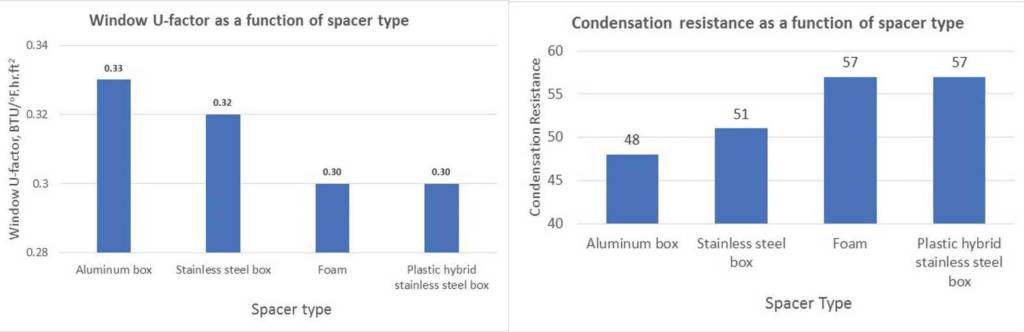
Figure 12 demonstrates the overall U-factor and condensation resistance (using CR value) of a thermally broken window with dual-pane low-e glazing as a function of spacer type (with the same sealant height and frame bite). There are two key takeaways from this data:
- Although the U.S. market often thinks of the stainless steel box spacer as a ‘warm-edge’ spacer, the data shows performance is closer to that of aluminum than it is to the higher thermally performing warm-edge options of plastic-hybrid stainless steel and foam.
- Despite the thermal transmittance of a foam spacer being lower than that of a plastic-hybrid stainless steel spacer, there is no meaningful difference in overall window performance when appropriate amounts of sealant are included in the edge seal and it is integrated into the frame with the same edge bite. The CR values and U-factors for the example window are the same whether foam or plastic-hybrid stainless steel is used.
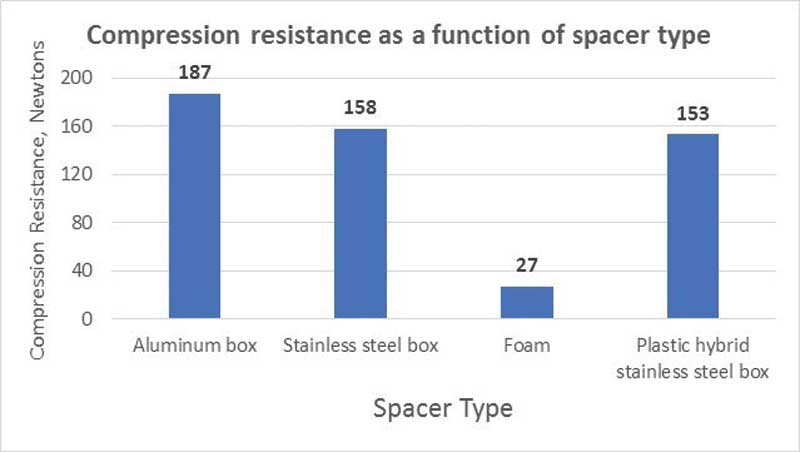
The addition of a true warm-edge spacer—such as a plastic-hybrid stainless steel—to a window system generally provides a reliable reduction in overall U-factor of about 0.02 to 0.03 Btu/F•hr•sf. This is approximately the same impact as replacing air with argon in the cavity and is a cost-effective, reliable, alternative strategy for achieving the desired U-factor performance. Other considerations relative to the choice of spacer include influence on IG durability, ultraviolet (UV) stability, and structural performance.
The compression resistance of various spacer types is shown in Figure 13 and illustrates stainless steel and plastic-hybrid stainless steel box spacers have similar performance in this area. As expected, foam spacers have significantly lower compression resistance. For nonmetallic spacers, or metal spacers with colored coatings, UV resistance is important. This author recommends specification of compliance with ASTM G154, Standard Practice
for Operating Fluorescent Ultraviolet (UV) Lamp Apparatus for Exposure of Nonmetallic Materials.
From an IGU durability perspective, sealant adhesion is critical, and meeting ASTM E2190, Standard Specification for Insulating Glass Unit Performance and Evaluation, is suggested. Since durability is as much a function of fabrication as it is IGU design, it is highly recommended to specify a requirement for IGU certification through a program that requires regular factory audits and regular testing of units made on the fabricator’s production line while being witnessed by an auditor. The Insulating Glass Certification Council/Insulating Glass Manufacturers Alliance (IGCC/IGMA) program meets this standard.
Conclusion
Since U-factor and condensation resistance are highly driven by the frame and EOG performance, it is important to focus on the perimeter first, and then the center of glass. It is vital not to confuse the easily obtained COG performance with the harder-to-calculate U-factor performance of the whole window. There is often a large disparity between the two, and interchanging them during the specification or modeling process can lead to significant issues with the as-built design.
As this article demonstrates, polyamide strips are a proven, flexible method to create high-performance frames. A warm-edge spacer delivers a reliable 0.02 to 0.03-Btu/F•hr•sf reduction in U-factor—one must consider durability when selecting spacers as thermal performance is only as good as the longevity of the unit. Stainless steel spacers with standard commercial sealant heights do not deliver significantly improved warm-edge performance over aluminum.
Helen Sanders, PhD, is responsible for strategic business development at Technoform North America. She has 23 years of experience in the glass industry, focusing on coatings and insulating glass technology and manufacturing. Sanders has a doctorate in surface science from the University of Cambridge, England. She is the president of the Façade Tectonics Institute and is a director of the Insulating Glass Manufacturers Alliance (IGMA). Sanders can be reached at hsanders@technoform.us.