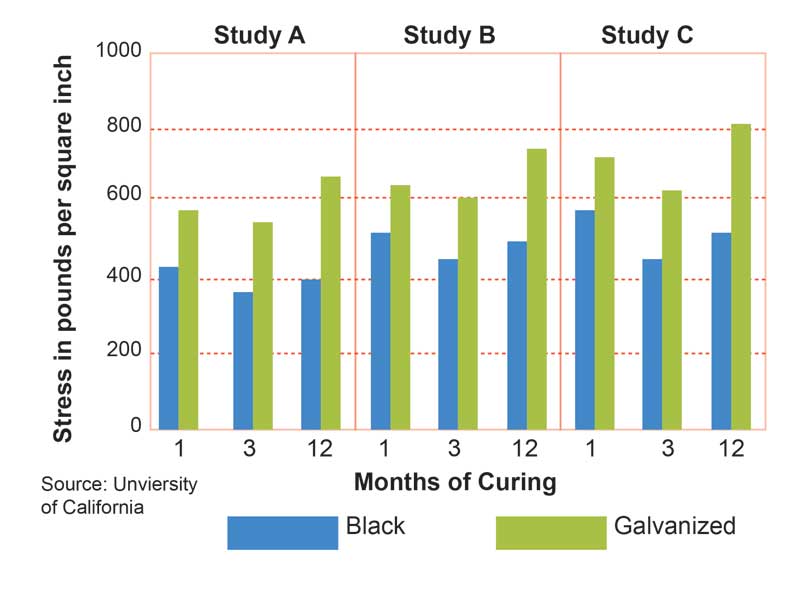
A good bond between reinforcing steel and concrete is essential, as bond strength helps ensure reliable performance of the structure (Figure 1). Many factors affect the development of this bond, including environmental factors, cure time, and the chemistry of the concrete mixture. Studies of the bond strength of galvanized rebar show it offers equal or slightly better performance compared to black rebar, while epoxy-coated rebar tends to have even less bond strength than uncoated. (For more, consult S.R. Yeomans’ and D.R. Ellis’s “Further Studies of the Bond Strength and Slip Characteristics of Galvanized and Epoxy Coated Steel Reinforcement in Concrete” from the December 1992 International Lead Zinc Research Organization [ILZRO] Project Report.)
One of the biggest factors that have an influence on corrosion concrete is chloride concentration. The protective layer of zinc on galvanized reinforcing steel serves as a barrier to the many corrosive elements the rebar is exposed to when embedded in concrete. It can withstand chloride concentrations at least four to five times higher than black steel’s limit, delaying the onset of chloride corrosion. (See “Galvanized Steel Reinforcement in Concrete” by Yeomans, published by Elsevier Ltd. in 2004.) As noted, galvanized reinforcing steel corrosion byproducts tend to be less dense, and eventually migrate away from the steel and into the concrete mix. This reduces the risk of rebar failure, preventing cracking and spalling of the concrete.
Durability is important to reinforcing steel, as the bars tend to incur rough handling during installation and may be stored outside for some time before use. From installation through the use phase, galvanized rebar is abrasion-resistant and durable due to the strong metallurgical bond between the steel rebar and zinc coating, which is created during the galvanizing process. While in the galvanizing kettle, the zinc and steel react to form a series of intermetallic alloy layers, which are harder than the steel they safeguard and provide excellent abrasion resistance. This protective coating remains tightly adhered when galvanized rebar is dropped, kicked, stepped on, or rubbed against existing concrete or other rebar on the jobsite. It also withstands the effects of ultraviolet (UV) light, temperature extremes, and exposure to rain or snow, protecting the rebar both as it waits to be used and while in use.
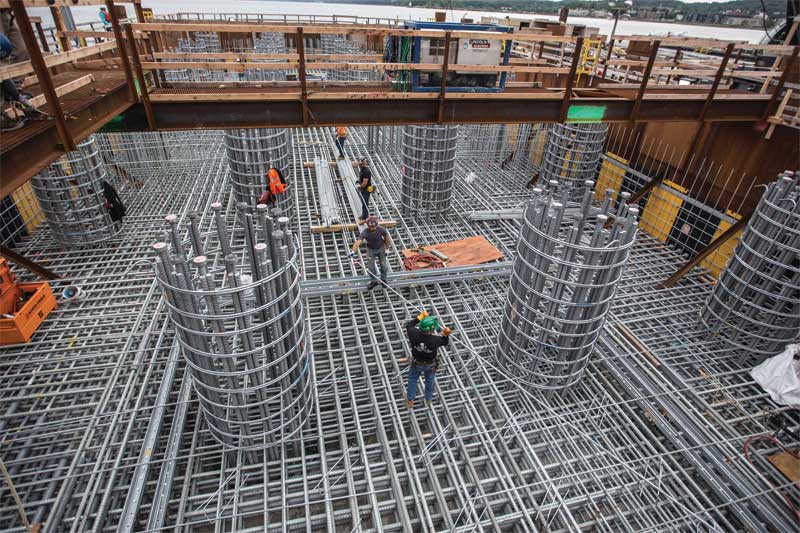
Photos courtesy New York State Thruway Authority
Galvanized rebar provides a level of cathodic protection where the zinc preferentially corrodes when in contact with bare steel, making it an effective coating material for durable corrosion resistance. Stainless steel is also quite durable, but lacks the sacrificial protection of zinc. Epoxy-coated rebar must be handled very carefully during transportation and installation to avoid damaging the fragile coating.
Cost is an important factor in choosing a reinforcing steel option. Many concrete building and transportation projects are created through the use of taxpayer money, so ensuring these structures last, remaining free of maintenance and spalling, is essential. Although epoxy-coated rebar can be less expensive on an initial basis, it tends to have a shorter lifespan than other types of reinforcing steel. Stainless steel is much more expensive on an initial basis, but has an estimated lifespan of at least 75 years. Galvanized rebar shares this longevity, but is competitive with epoxy on an initial cost basis and about 25 percent the initial cost of stainless steel.
A series of standards exist to ensure reinforcing steel meets the proper procedures and industry regulations. These specifications detail requirements for finish, appearance, and adherence. ASTM A767, Standard Specification for Zinc-coated (Galvanized) Steel Bars for Concrete Reinforcement, details galvanized rebar specifications. ASTM A955, Standard Specification for Deformed and Plain Stainless-steel Bars for Concrete Reinforcement, covers stainless steel rebar. Epoxy-coated rebar must meet either ASTM A775, Standard Specification for Epoxy-coated Steel Reinforcing Bars, or ASTM A934, Standard Specification for Epoxy-coated Prefabricated Steel Reinforcing Bars. It is important to become familiar with these specifications when using reinforcing steel, as improper use may result in either a loss of adhesion and bonding or poor performance.
VETERANS MEMORIAL BRIDGE |
The Veterans Memorial Bridge, which spans the Ohio River to connect Weirton, West Virginia, and Steubenville, Ohio, opened on May 1, 1990. The bridge is an example of what can happen when reinforcing steel fails to withstand the environment in which it is placed. By February 2009, after less than 20 years in service, the rebar had corroded, leading to cracking and spalling of the concrete. Using rebar able to withstand the moist river environment and damaging winter road salts would have kept the concrete intact, greatly reducing the economic and time burden required to repair and replace it. |
This article inaccurately states that, “Stainless steel is a newer reinforcing steel application. Therefore, there is less data available regarding its performance.” The world’s longest pier in Progreso Mexico was completed in 1941 using stainless steel reinforcement. Based on this article, that was well before galvanized rebar was introduced.
The statement indicating the studies of stainless steel reinforcement are limited is also false. Stainless steel concrete reinforcement has been extensively studied globally and its’ exceptional performance documented in NACE and other papers. There have been many long term side-by-side bridge deck installations (Americas, Europe, Asia) and comparative evaluations of stainless steel relative to other types of reinforcement.
Furthermore, for steel reinforcement to be identified as “corrosion resistant” in the ASTM standards, there must be a corrosion test and a minimum requirement for certification. The ASTM stainless steel and epoxy coated rebar both have corrosion test requirements – galvanized steel does not and when this has been discussed at past A01.05 meetings the industry has declined to add a corrosion test requirement. A review of the corrosion data available for galvanized rebar shows that it does not perform well in the standard laboratory tests that are used for steel reinforcement and the evaluation of its’ performance in actual installed applications has varied substantially based on the concrete type and actual conditions.
This article is factually problematic in many respects and is clearly attacking a competitive material by providing false information.