Far away from any major city, the nine-story, 239-unit, high-rise Silver Creek Resort in Snowshoe, West Virginia, has undergone a complete claddings renovation.
The resort’s exterior was a panelized exterior insulation and finish system (EIFS) that had been experiencing water leaks since its 1985 installation. Incorrect installation and maintenance was the cause of the leaks, according to Sam Collins, general manager.
Once there was a decision to restore the building, the team worked with an architect and considered metal panels, fiber cement, and other claddings. In the end, however, a 127-mm (5-in.) drainable EIFS was specified because it was deemed to be the best fit and had the best R-value (i.e. approximately R-19 of continuous insulation [ci].)
Specifying EIFS
The system includes a fluid-applied waterproofing air barrier, and finish with a pronounced self-cleaning effect. This project consisted of 11,612 m2 (125,000 sf) of wall cladding.
Snowshoe’s climate includes some of the most extreme wind, snow, and rain in the Southeast. Prior to the renovation, whenever a severe storm came through, management had to deal with damages and continue to ‘Band-Aid’ additional problems.
According to Collins, when the original EIFS was installed there was no option for substrate protection, air barriers, or drainable systems, but this has since changed and staying informed is key.
Before starting the project, building sections had to be opened up to identify the existing condition behind the wall. Issues such as how the EIFS panels were hung on the building, window leakage, and imperfect seals had to be identified so a solid, watertight building with the new cladding could be created.
“We had to remove all the original exterior skin including the EIFS, exterior sheathing, and wet wall cavity insulation before we could begin,” said Gabriel Castillo, of EIFS-installer Pillar Construction. “The trend now is to insulate outbound of the exterior sheathing taking the insulation out of the cavity, and we did just that.”
The renovation begins
Members of the resort’s board of directors knew something had to be done. The building had been leaking for more than 25 years, and the damage would only escalate. After looking at various cladding options, they decided to employ EIFS.
After the initial drawings, they worked with architect Peter Fillat who came up with the design plans to maintain the building’s strong architectural façade.
Adding a continuous air and moisture barrier—now code in most states—gave the building a R-value not compromised by the thermal bridging effect of stud framing. The air barrier was connected to the windows to give it a tight seal. West Virginia has adopted the 2009 International Energy Conservation Code (IECC), which requires both ci and air sealing.
All 740 windows needed to be replaced. The new assemblies were thermal break horizontal sliding and fixed, and played a big part in energy savings. Without thermal breaks, the window frame becomes a thermal bridge to the exterior and a conduit for energy loss and a possible source of condensation in the wall section.
The previous installation had expansion joints between each panel, but because the renovations removed everything down to the studs, the panel-to-panel joints in the substrate were eliminated. This allowed the air barrier to run continuously between the panels and provided less opportunity for water and moisture to get in.
Challenges
The project was completed in two phases over more than two years. The building was occupied during the entire transition with full-time residents and vacationers. Getting all the ownership together was the first challenge, according to Castillo. However, something needed to be done immediately.
The next challenge was the climate. Silver Creek is located on the ski slopes and sits at 1280 m (4200 ft) above sea level. The average annual snow fall is 4572 mm (180 in.). The decision to renovate was made in early 2011, however, because of the winter, construction had to wait.
The final challenge was location. Even the closest hardware store was three hours away, according to Castillo. There is also limited use of cell phones, because of its proximity to the National Radio Astronomy Observatory (NRAO) located in nearby Green Bank. The construction crew committed to work for two to three months at a time, and stayed on the property.
Craig Swift of the project’s structural engineering firm, Keast and Hood, focused on repairing the metal stud backing. Much of the metal stud cladding wall system had deteriorated, though the primary structural system was in fairly good shape.
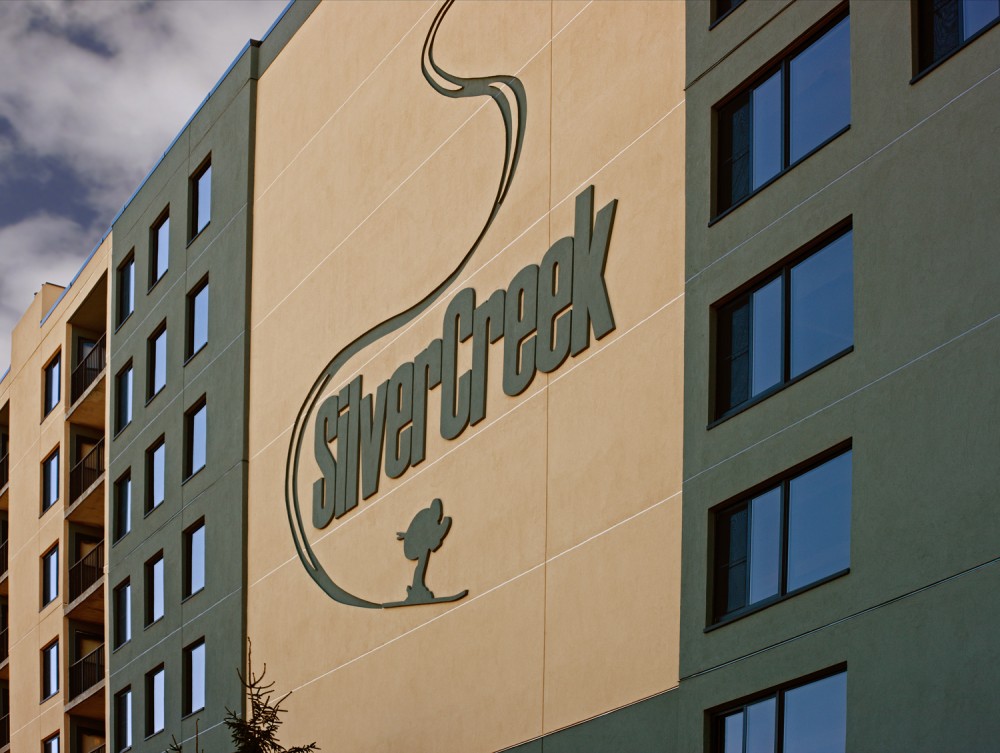
Testing—One, two, three
Scott Johnson, an inspector with Williamson & Associates, performed window water testing during phase one and tested windows and claddings related to the openings in phase two. The EIFS, windows, and installation all performed well.
“The building tested out fine,” said Johnson. “There was a major storm during the final phase of construction, with 85-mph [i.e. 137-km/h] winds and hard rain. There were no leaks.”
Johnson and his team conducted ASTM E1105, Standard Test Method for Field Determination of Water Penetration of Installed Exterior Windows, Skylights, Doors, and Curtain Walls, by Uniform or Cyclic Static Air Pressure Difference. This evaluates water infiltration performance, capabilities of windows, and related building construction.
The new primary cream color, with a separate forest green color insert, gives the building a distinct profile and more depth, according to Fillat. This was the first time the architect had ever worked with a drainable EIFS cladding, and he feels it solved this longstanding problem.
After the renovations, residents began noticing drastic changes in their utility bills, with savings of 20 to 50 percent, said Collins.
“There has been a big noise reduction from the outside— most likely due to the ‘air-tightening’ of the building envelope,” he said. “Another benefit is from inside my residence I can no longer hear the wind blowing or have snow in my living room each morning when I wake up.”
Tom Remmele, CSI, is the director technical services/R&D for exterior insulation and finish system (EIFS) producer, Sto Corp. He has held technical management positions in the construction industry for more than 25 years. Remmele is a past Technical Committee chair of the EIFS Industry Members Association (EIMA). He can be reached at tremmele@stocorp.com.
To read the full article, click here.