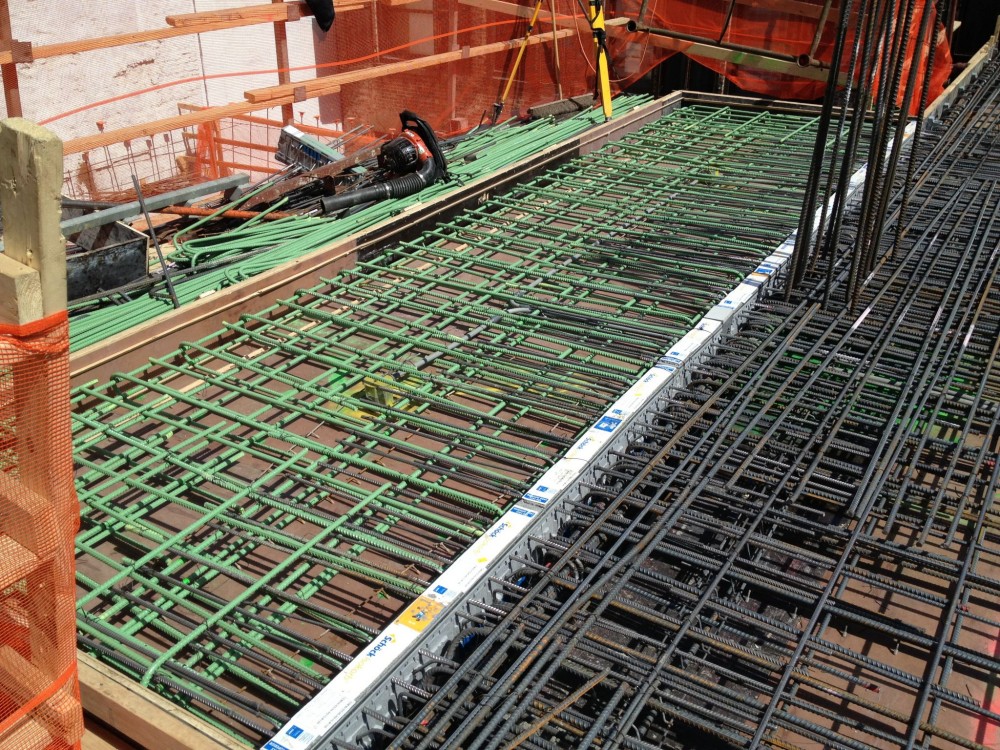
by Paul Nutcher, CSI, CDT, AIA Allied
Engineered structural thermal breaks at balcony connections can assist mid-rise and high-rise building project teams in complying with the new continuous insulation (ci) code requirements. These structural components are especially important to address in multi-family specifications because thermal bridging for every residential unit can contribute significant heating and cooling loads.
Simply adding insulating materials between reinforcement steel (intermittent concrete) or insulating a balcony’s full perimeter may improve performance slightly, but there are more effective approaches, such as incorporating structural thermal breaks between the balcony and the floor slab. Such products reduce the heat transmittance through the slab by up to 75 percent, effectively raising the interior surface temperature to improve condensation control This can assist project teams pursuing certification under programs like U.S. Green Building Council’s (USGBC’s) Leadership in Energy and Environmental Design (LEED) and the Green Building Initiative’s (GBI’s) Green Globes.
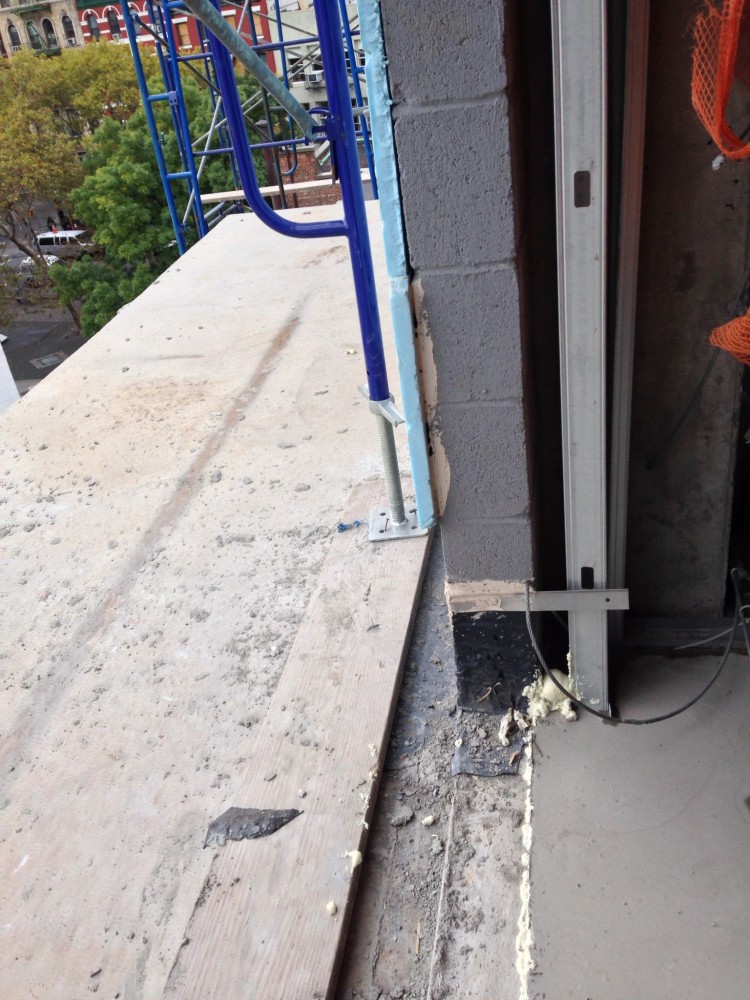
Some ad-hoc approaches to reduce the condensation and mold problems caused by thermal bridging have included various well-intentioned, but inefficient, designs as inserting insulating materials between reinforcement steel (intermittent concrete). However, this strategy is limited as common steel and its surrounding concrete continue to serve as bridges.
Insulating or wrapping the full perimeter for the balcony is another well-intended option, but this is often expensive and can create durability issues, leading to higher maintenance needs. Directing HVAC air-handlers to cold slabs is a third common remedy, but this is more of an improvised solution, as the mechanical system only reduces condensation when turned on and will not mean a permanently warm slab.
Understanding the technology
Structural thermal breaks are load-bearing insulation elements that, as their name suggests, form a thermal break between the balcony and the interior floor while transferring loads and therefore maintaining full structural integrity. Further, they enable the warmer interior temperature to be kept, avoiding condensation and preventing mold formation. Off-the-shelf structural thermal breaks are fully engineered assemblies; they come ready to install onsite, providing tension and compression reinforcement. In comparison to ad-hoc approaches such as intermittent concrete, it also offers significant cost benefits, greater flexibility in concrete design, opportunity for simpler specifications and scheduling, and improved site-handling.
Manufacturers now offer drawings and specification with configuration and design of the thermal break according to project needs. Standard systems are available to suit most depths of cantilevered and simple support balconies (propped cantilever balconies). The various systems allow the transfer of all loads in structural concrete, including moment, shear, compression, and tension to suit various load conditions.
A typical manufactured structural thermal break replaces the concrete between the exterior balcony and the interior slab with an insulating material such as high-density, graphite-enhanced expanded polystyrene (EPS); its reinforcing rods that penetrate the foam are stainless steel (rather than carbon). This type of assembly combines the strength of concrete, the thermal performance of foam and polystyrene, and the convenience of an off-the-shelf technology for cantilevered balconies.
The assembly’s stainless steel elements provide a third of the thermal conductivity of carbon steel. Further, the corrosion-resistant properties of stainless steel make it an excellent material for this condition.
Pre-engineered thermal breaks can be used for concrete-to-concrete, steel-to-steel, and steel-to-concrete assemblies with a thermal break module between an external balcony and an internal structural frame. They are suitable for various floor depths and cavity widths in building cladding applications, and can be used for precast or cast-in-place.
The precise calculation of thermal conductivity of an engineered product with multiple components is a complicated process. However, relying on foam and stainless steel instead of reinforced concrete (with plain carbon steel) results in significantly lowered thermal conductivity. Simplified examples of an insulated balcony versus a non-insulated one show heat loss through the former can typically be around 13 times less than through the latter.1 This dramatic reduction in heat loss translates to a slab that, in many conditions, will be warm enough to avoid condensation.
While thermally broken assemblies are used most often in balconies due to their numerous occurrences in multi-family and hotel designs, they can also be employed to thermally break other common commercial building elements—such as parapets, corbels, and relieving angles—wrapped around an entire multi-story skyscraper.
The result of installing thermally broken connectors is a warmer multi-family dwelling with chilly winter temperatures kept outside the balcony slab; further, discomfort due to condensation and mold is curtailed as moisture is also controlled by these pre-engineered systems. Additionally, these are among the requirements for gaining certifications through green building rating programs.

LEED for New Construction (NC) v4 will address the thermal comfort of occupants in its Indoor Environment Quality (EQ) Credit 5, Thermal Comfort. The relevant standard is American Society of Heating, Refrigerating, and Air-conditioning Engineers (ASHRAE) 55-2010, Thermal Comfort Conditions for Human Occupancy, with errata or local equivalent. By eliminating thermal bridging within the building envelope, project teams that design thermally broken balconies can meet the requirement of LEED v4 Credit 5.
However, most mid-rise multi-family projects at four or more stories tall would typically fall under the LEED for Homes Rating System: Multifamily Mid-Rise. (The exception would be mixed-use developments where less than 50 percent of the occupied space was devoted to residential dwellings. In these cases, LEED NC must be followed.) A balcony’s thermal break contribution to the mid-rise rating system is indirect, but could be significant in the energy credits and, to a lesser degree, other categories.
Continuous insulation and codes
The increasing popularity of thermal breaks in balconies is linked with the assemblies’ aim to provide continuous insulation. The latest versions of the 2012 International Energy Conservation Code (IECC) and ASHRAE 90.1-2010, Energy Standard for Buildings Except Low-rise Residential Buildings, require increased energy performance. In the past, these demands could be achieved with upgraded HVAC and lighting, along with higher R-Values in the building envelope. Now, meeting the new energy codes will require additional steps toward improving overall energy performance.
ASHRAE 90.1 is the benchmark for commercial building energy codes; its latest version is referenced in LEED v4, which was released in November 2013, while its previous 2007 and 2004 iterations continue to be commonly used in local building codes. All federal buildings entering design and construction as of July 2013 must now use the 2010 version of the standard.
The new energy requirements also call for the additional step of continuous insulation (ci) throughout the entire building envelope. Once these steps have been exhausted from an economic standpoint, pre-engineered thermal break connections assist project teams further with compliance with the new codes. Insulation control layers where the balcony interfaces the building is especially important to address in multi-family specifications when considering not only energy loss, but also occupant thermal discomfort and the possibility of potential condensation and mold conditions.
While some of the aforementioned bespoke approaches may slightly improve performance by reducing conductivity at the slab-balcony interface, they are often costly and create additional problems. Engineered solutions integrated into the existing floor slab provide a ci layer preventing thermal bridging through the balcony’s slab edge.
Continuous insulation for balconies
Previous energy code revisions have raised the performance requirements of all systems within the building—mechanical, lighting, and envelope. While this makes baseline buildings very energy-efficient, there is still room for improvement, especially in the structural-envelope interface as HVAC efficiencies can no longer be expected to make up for shortfalls in whole building energy performance.
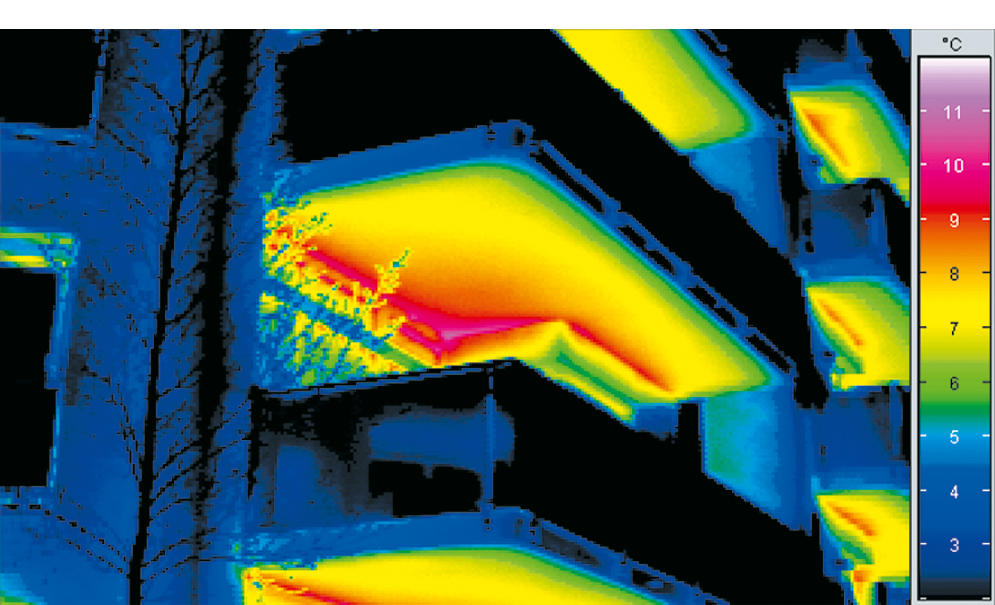
The balcony-slab intersection is one such detail, which has been a source of thermal bridging and therefore reduces the building envelope’s efficiency. Pre-engineered thermal break connections prevent thermal bridging because they block the pathway for heat transfer through the building thermal envelope, and occupants are no longer dealing with the discomfort of cold surfaces inside the building.
The 2012 IECC requires more insulation, a tighter building envelope, and improved energy efficiency mechanical and building assemblies throughout the structure. The thermal transmittance is among those more stringent measurements. A thermally non-broken balcony is typically approximately 0.474 kJ (0.45 Btu) per linear foot, but with thermal break assemblies, the number drops to approximately 0.211 kJ (0.2 Btu) per linear foot, according to engineering firm Morrison Hershfield’s Stephane Hoffman.
LEED, Green Globes, and ASHRAE 189.1 further challenge project teams to gain energy performance levels above and beyond baseline energy codes. In multi-family buildings with balconies using concrete construction methods there will be some unique challenges. Most energy codes have enacted continuous insulation requirements to address thermal bridging, including the 2012 IECC. The air barrier requirement will mean the enclosure must not allow more than 0.68 m3/hr (0.4 cfm/sf) of air leakage of the building envelope.
While some jurisdictions have not adopted any energy code requirements, most are now using the 2009 IECC, with some states (e.g. Washington) adopting the latest version. Still, some states are using the 2006 code.
To address these compliance challenges, ASHRAE Research Project (RP) 1365, Thermal Performance of Building Envelope Details for Mid- and High-rise Buildings was conducted by Morrison Hershfield, and accepted in July 2011 by ASHRAE. Prior to this report, ASHRAE 90.1-2007 offered little guidance on thermal bridging outside the building envelope assembly. This meant the project team spent little time on this potential energy draining detail. The expansive report with 3D drawings calculates the thermal performance data for common building envelope details for mid- and high-rise construction. The report will benefit project teams seeking to comply with the newer, stricter building and energy codes adopted in several states.
Additionally, the continuous air barrier requirement in ASHRAE 90.1 is not the only new requirements for the building envelope that will potentially impact the design and construction of balconies. There will be improved leakage requirements for exterior doors, restrictions on east and west windows, skylights, and automatic daylighting requirements for large spaces, and an exception to the solar heat gain coefficient (SHGC) for dynamic glass.

Moisture control
Indoor moisture control is addressed within certain specific LEED rating systems credits, and strategies to avoid excessive moisture migration are recommended. When properly executed, thermally broken balcony connections are among the methods for controlling moisture by avoiding condensation on cold surfaces. The science involved in calculating whether any condensation (i.e. dewpoint temperature) occurs on a given balcony intersection is beyond this article’s scope.2
Generally, determining this specific point involves the following variables:
- dry bulb temperatures;
- relative humidity (RH) or humidity ratio;
- specific volume of dry air; and
- enthalpy (i.e. amount of energy per unit of mass of dry air).
Using these values, along with psychometric charts, results in dewpoint temperature where condensation occurs. For this reason, insulating materials can only be analyzed in conjunction with specific temperature, air, and humidity conditions to assess the potential for condensation. Regardless, it is clear having well-insulated materials greatly reduces risk for most climatic conditions.
Ponding water on balconies can be another source of moisture getting beyond the building envelope. Further guidance about avoiding the potential for excessive moisture penetration within the balcony-slab interface due to ponding can be researched in American Concrete Institute (ACI) 117-10, Specification for Tolerances for Concrete Construction and Materials, which defines the acceptable amount of slope variation. Generally, a one-percent slope is called for by architects, but a two-percent slope maybe more desirable to avoid ponding, which is generally defined as water remaining on a balcony or rooftop for more than two days per National Roofing Contractors Association’s (NRCA’s) Roofing and Waterproofing Manual.
While ponding water can usually be avoided with the proper design specifications, the moisture control benefits of thermally broken connectors can reward project teams with savings in moisture damage to the envelope and costly renovations. There are also the potential occupant health benefits with the avoidance of mold due to moisture from condensation.
In LEED NC, healthcare projects must develop a moisture control plan per EQ Credit 3, Construction Indoor Air Quality Management Plan. The credit reads:
Also, include strategies for protecting the building from moisture intrusion and preventing occupants’ exposure to mold spores.
In LEED for Mid-rise, a moisture management plan is also required. This would be part of a strategy for compliance with the EQ Credit 3, Moisture Control, which directs the project team to address this potential threat during compliance with the Innovation in Design (ID) Prerequisite 2.1 and 2.2, which require development and performance of a Durability Inspection Checklist, including indoor moisture control measures. A strategy for moisture management that includes structurally broken connectors can assist project teams in meeting these requirements toward certification through a green building rating system.
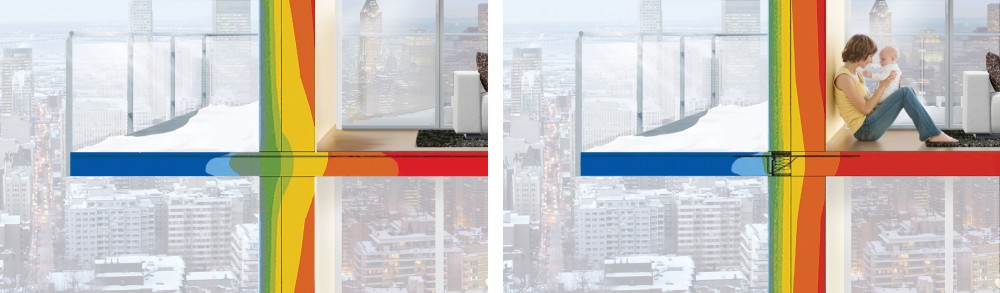
Market drivers
The market for multi-family is one of the most active building segments. Since the 2012 IECC is stringent, developers of such projects have to closely look at the economics of employing building technologies and engineered solutions. There is a lot of demand for the thermal breaking of balconies with the techniques of a pre-engineered solution. While these are relatively new in North America, their wider use is being driven by several factors. States beginning to adopt stricter energy codes is one obvious reason, but there is more driving their use.
Many contractors find installation to be simple after the first balcony; for many, using the material ultimately saves time on the overall project. Developers will also be interested in selling their finished products for additional monies. However, LEED will also push the implementation of thermally broken balconies because a project team will want to gain some points in Energy & Atmosphere (EA) Credit 1, Optimize Energy Performance, which has the highest possible number of points to be potentially gained (between 15 and 19). Therefore, the need for points in this credit is virtually essential because some owner representatives, including many federal agencies, will demand a minimum of LEED Silver. It is difficult to gain this without attaining multiple points.
LEED v4 requires ASHRAE 90.1-2010, which most certainly require continuous insulation to gain the required EA Credit 1 for energy performance above 10 percent of a baseline building in terms of energy performance and ASHRAE 90.1.
Other environmental factors serving as market drivers include the fact the components of a thermal break can contain recycled content and are fully recyclable after their useful life span. Manufacturers typically reintegrate scrap into the supply chain if they are not actually producing the component steel and foam materials in the connectors, as part of a best manufacturing process.
Structural loading considerations
From a structural point of view, balconies have to resist several loading conditions, whether permanent (dead load) or variable (live loads, wind loads, snow loads). However, earthquakes are also an important factor. Seismic considerations could have a relevant influence on a building’s design, including the location (seismic hazard), soil composition, stiffness and weight, and the assemblies.
Building codes address the dynamic behavior of earthquakes by providing clear requirements for design procedures, along with dynamic analyses or equivalent static loading caused by the movement of the building as a reaction. The balcony, as an external structural element with a specific weight, also reacts on dynamic seismic effects—this must be taken into consideration when designing not only this component, but also its connection.
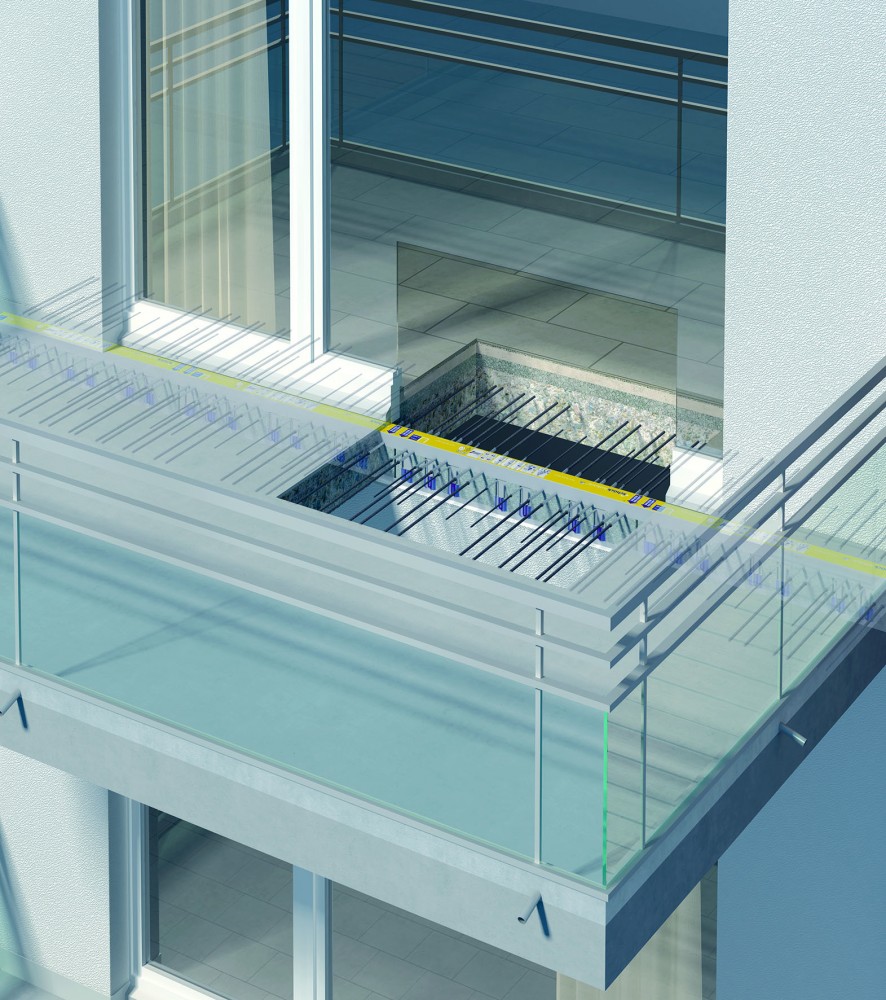
to work together to eliminate excessive
thermal bridging at the balcony connection of both mid-rise and high-rise buildings.
Earthquake loads typically result in movements in the horizontal directions of both building axes, upward and downward. The balconies follow these movements after a delay. In cantilevered balconies, specifically designed thermal break elements typically provide sufficient capacity for the transfer of the vertical loads caused by permanent and variable loading and horizontal forces, as well as uplift bending moments in both seismic and high-wind load events, as long as the structural engineer has provided accurate calculations. Further, the number of the specifically designed structural thermal breaks may have to be determined based on seismic considerations.
Installation considerations
As the pre-engineered thermal break has structural responsibilities, all efforts should be made to store the product according to the manufacturer’s recommendations. If the polystyrene units are damaged, they can be patched with polyurethane foam to maintain the insulation properties, as they are a non-structural piece of the assembly. The stainless steel shear bars must not be cut or bent—modifications should only be made under instructions from an engineer.
Structural thermal breaks are designed and shipped to the construction site in a standard length of 1 m (3.28 ft). To achieve connection lengths outside this, the product can be divided in the middle with a simple hand-saw.
To install the structural thermal break units, a gap in the reinforcement should be left at the balcony connection point. The thermal break unit is then placed between.
Conclusion
The project team and the structural engineer will need to communicate to gain the new measurements asked for in 2012 IECC. Designers may need to alter their previous approach to balcony design to meet the code update and incorporate a structural thermal break solution.
Additionally, while energy efficiency was often the mechanical engineer’s purview, the new versions of the energy codes and standards, and the new green building rating systems, task the structural engineer for contributions toward more energy-efficient structures. So in the case of balconies with structural thermal breaks, USGBC’s goal for market transformation toward greener buildings and LEED’s efforts to introduce a more integrated design process to building projects is working just how it desired. With growing voluntary and mandated requirements for energy efficiency in buildings, manufacturers have responded with solutions for thermal breaks within the building envelope with engineered solutions for thermally broken connectors for balconies.
Notes
1 See the article, “Concrete Solutions for Balcony Connections,” by Victor J. Yakin, CSI, which appeared in the April 2010 issue of The Construction Specifier. (back to top)
2 Ibid. (back to top)
Paul Nutcher, CSI, CDT, AIA Allied, is the president of Green Apple Group LLC, a marketing, technical, and sustainability consulting firm. He has more than 10 years of building industry experience as a specifications and technical writer, educator, and consultant to product manufacturers and design/construction professionals. Nutcher has served in leadership roles with CSI, the U.S. Green Building Council (USGBC), and the American Institute of Architects (AIA). He can be reached at pnutcher@greenappleconsult.com.
To read a case study about New York City’s Chelsea Green , click here.