Coatings
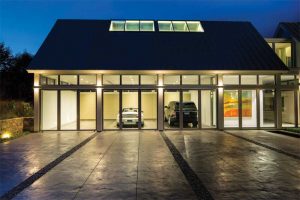
Photo courtesy Wasco
Externally applied coatings can be in the form of organic (hydrocarbon-based) paints, such as acrylics, fluoropolymers, polyesters, and siliconized polyesters. Each coating contains pigments and resins, or binders, which are the primary basis for their classification. In addition to the wide range of color choices, including bright metallic hues, paint finishes provide an attractive, smooth appearance. These organic coatings can be applied in a number of ways. Some of the more common methods include a spray system, similar to the way a car would be painted:
- dipping, that generally requires large automated conveyers; and
- tanks filled with the finish material of choice or powder coating.
AAMA standards describe laboratory test methods and performance criteria shown to be critical to coating performance. They are organized in a sequential order of basic-, high-, and superior-performance (i.e. ‘good, better, and best’)—a triumvirate of increasingly stringent performance criteria. This hierarchy allows architects to choose the best and most cost-effective match for the type and location of building and weather exposure. For aluminum profiles, the standards for organic coatings:
- AAMA 2603-17a, Voluntary Specification, Performance Requirements and Test Procedures for Pigmented Organic Coatings on Aluminum Extrusions and Panels (with Coil Coating Appendix);
- 2604-17, Voluntary Specification, Performance Requirements and Test Procedures for High Performance Organic Coatings on Aluminum Extrusions and Panels(with Coil Coating Appendix); and
- 2605-17a, Voluntary Specification, Performance Requirements and Test Procedures for Superior Performing Organic Coatings on Aluminum Extrusions and Panels (with Coil Coating Appendix).
The entry requirement for finish compliant with AAMA 2603-17a must be 20 µm (0.8 mils) thick, while those meeting 2604-17 and 2605-17a, must be 30 µm (1.2 mil) thick. The highest-performing coating would meet AAMA 2605-17a.
All three standards test for color uniformity, specular gloss, dry film hardness, film adhesion, resistance to impact, chemical, corrosion (caused by humidity and salt spray), and color fading or deterioration due to weathering. AAMA 2604-17 and 2605-17a, add abrasion resistance to this list. For other factors, exposure conditions vary. For example, exposure time to the corrosive influences of high humidity increases across 2603-17a, 2604-17, and 2605-17a, from 1500 to 3000 and 4000 hours, respectively. Weathering test duration also increases from one and five to 10 years, respectively. Corrosion susceptibility based on reaction to salt spray testing varies among the standards as well.
These are the specific requirements for superior performing coatings as described in AAMA 2605-17a.
Humidity
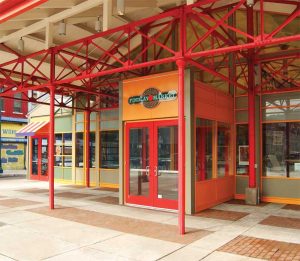
Photo courtesy YKK AP America
The sample is exposed in a controlled heat and humidity cabinet for more than 4000 hours at 38 C (100 F) and 100 percent relative humidity (RH). No formation of blisters to the extent greater than ‘few’ blisters, as defined by ASTM D714-02 (2017), Standard Test Method for Evaluating Degree of Blistering of Paints. Cyclic corrosion testing (previously referred to as salt spray resistance).
Score the film deep enough to expose the base metal. Expose the sample for 2000 hours according to the dilute electrolyte cyclic fog/dry test in Annex A5 of ASTM G85, Standard Practice for Modified Salt Spray (Fog) Testing. The sample must score a minimum rating of 7 on scribed or cut edges, and a minimum blister rating of 8 within the test specimen field, as defined in ASTM 1654, South Florida exposure.
South Florida exposure
The coating shall maintain its film integrity, color and gloss retention, and chalk- and erosion-resistance properties for a minimum of 10 years on the South Florida on-fence testing site.
Color retention
Maximum of 5ΔE Units (Hunter) of color change after the minimum 10-year exposure test. A ΔE unit is the variance or color difference measured on a vector scale from a specific point in the color space.
Chalk resistance
Chalking shall be no more than represented by a No. 8 rating for colors and No. 6 for whites after 10 years of test-fence exposure. Per ASTM D4214-07 (2015), Standard Test Methods for Evaluating the Degree of Chalking of Exterior Paint Films, chalking is measured on a numerical scale with higher numbers representing better chalk resistance.
Gloss retention
Gloss retention shall be a minimum of 50 percent after the 10-year exposure testing, as described by ASTM D523-14 (2018), Standard Test Method for Specular Gloss.
Resistance to erosion
Less than 10 percent film loss after the 10-year exposure testing. AAMA notes in high-humidity environments such as, but not limited to, coastal or industrial areas, performance of corrosion resistance may be diminished.
Sand abrasion testing improvements
An appropriate test to determine the abrasion resistance of organic coatings has been a falling sand test (ASTM D968, Standard Test Methods for Abrasion Resistance of Organic Coatings by Falling Abrasive), referenced in AAMA 2604-17 and 2605-17a, intended to simulate the effect of wind-driven sand. This test is still in high demand in the Middle East as well as in beach and desert environments in the United States. However, research has revealed there is a lot of variation between labs in the results, and it does not appear to have the repeatability and precision to provide good data.
Accordingly, the abrasion test in 2604-17 and 2605-17a will be changed in future to show the requisite performance mandate as ‘calculate and report’ versus the current pass/fail requirement prescribing a minimum passing value. Additionally, AAMA 2604-17 and 2605-17a abrasion resistance sections will match the corresponding sections in AAMA 624-17a, Voluntary Specification, Performance Requirements and Test Procedures for High Performance Organic Coatings on Fiber Reinforced Thermoset Profiles, and 625-17a, Voluntary Specification, Performance Requirements and Test Procedures for Superior Performance Organic Coatings on Fiber Reinforced Thermoset Profiles, standards for fiberglass finishes.
Corrosion testing evolves
AAMA has been conducting testing to evaluate alternatives for the use of salt spray fog to more accurately quantify corrosion. The likely outcome will be the replacement of ASTM B117-18, Standard Practice for Operating Salt Spray (Fog) Apparatus test, with ASTM G85-11, Standard Practice for Modified Salt Spray (Fog) Testing, method in AAMA 2604-17, as in AAMA 2605-17a.
The current corrosion performance test specified in AAMA 2603-17a and 2604-17 is ASTM B117-18, providing a controlled corrosive environment to produce relative corrosion-resistance information. However, correlation and extrapolation of actual corrosion performance has not always been predictable.
The ASTM G85-11 is described as useful when a different or more corrosive environment than the salt fog described in B117-18 is desired. Conditions for five modifications in salt spray (fog) testing are set forth in the form of annexes. For use with architectural aluminum, the cyclic acidified salt spray test in Annex A5 will be specified.
The cyclic corrosion testing method described in ASTM G85 is effective for evaluating a variety of corrosion mechanisms, including general, galvanic, and crevice corrosion. It is a more realistic way to simulate observed outdoor conditions than traditional steady state exposure tests, such as B117-18. Since actual atmospheric exposures usually include both wet and dry conditions, by using cyclic corrosion testing accelerated laboratory tests can be patterned after these natural cyclic conditions.