Powder coating finishes
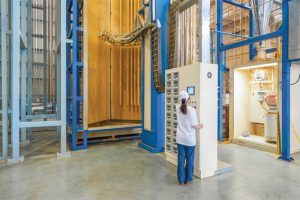
Photos courtesy AAMA
Powder coating is usually considered one of the most favored, durable, and cost-effective alternative among finishing options for aluminum extrusion products. It increases protection from cold, heat, corrosion, scratching, or even bleaching under the hot sun. Specific advantages include:
- the coating is fusion bonded to form a thicker coating, providing better protection and longer product life;
- since there are no solvents used, no potentially carcinogenic volatile organic compounds (VOCs) are released into the atmosphere, which many consider to make the process more environmentally friendly than liquid finishing; and
- the powder coating processes require significantly less energy for production.
Powder coating finishes involve a systematic process that— after pretreatment— consists of two steps.
Application
The powder, a fine mixture of colored pigment and resin, is commonly applied with an electrostatic spray gun. The powder is given a positive charge causing it to bond to the electrically grounded surface of the product. Other powder coating methods are fluidized bed, electrostatic magnetic brush, and electrostatic discs methods.
Curing
The object is heated in an oven for a set duration at a fixed temperature, causing the powder to melt uniformly, thus forming a hard coating when cooled.
Powder coating finishes on aluminum extrusion products can be categorized into thermosets and thermoplastics. The polymers used most commonly are acrylics, polyester, epoxy, and the hybrid polyester-epoxy.
Anodic finishes
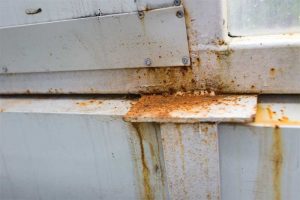
Since it is an integral part of the substrate, the oxide film produced by the anodizing process is uniform, hard, and protects the rest of the aluminum substrate from wear and abrasion. The coating is extremely durable, with the hardness of the surface comparable to a sapphire, the second hardest substance on earth next to diamond. This characteristic makes anodizing a suitable choice for use in high-traffic areas where resistance properties are important.
The process passes a direct electric current between aluminum and the electrolyte, with the alloy acting as the anode. The procedure mimics the naturally formed oxide film, but results in a thicker, more controlled formation of a durable oxide film.
To ensure quality and durability under long-term outdoor exposure, AAMA 611-14, Voluntary Specification for Anodized Architectural Aluminum, requires the anodized finish to pass tests for color and gloss uniformity, abrasion, corrosion, and resistance to ‘crazing’ (the formation of a network of fine cracks). It must also pass a weathering test, requiring minimal color fading or chalking (formation of a white film) due to sunlight after up to 10 years of exposure (depending on the specified performance level) in a Florida test location.
It is pertinent to note, the natural beauty of an anodic finish can be marred by harsh chemicals, rough conditions, or neglect. These conditions may only affect the surface finish and not reduce the service life of the aluminum, but mortar, cement, and other alkaline materials will quickly corrode an anodic finish if allowed to dry on the metal surface.
While similar to the requirements of the 2600 series of AAMA documents for organic finishes, the AAMA 611-14 and 612-17a, Voluntary Specification, Performance Requirements, and Test Procedures for Combined Coatings of Anodic Oxide and Transparent Organic Coatings on Architectural Aluminum, documents cover the unique requirements expected of anodic finishes. In order to meet AAMA 611-14 requirements, a Class I anodized finish must pass these stringent guidelines.
Abrasion resistance (Michael Clarke Test)
A go/no-go abrasion test using abrasive papers coated with silicon carbide, garnet, and glass, respectively.
Corrosion resistance testing
Expose the sample for 3000 hours according to ASTM B117-18 using a five percent salt solution. Test samples shall show no more than a total of 15 isolated spots or pits, none larger than 1 mm (39 mils) in diameter, in a total of 3810 mm (150 in.) of test area grouped from five or more test pieces.
South Florida exposure
The coating shall maintain its color and gloss retention and erosion-resistance properties for a minimum of 10 years on the south Florida on-fence testing site.
Color retention
Maximum of 5ΔE Units (Hunter) of color change after the minimum 10-year exposure test.
Gloss retention
Gloss uniformity shall be within established gloss range.
AAMA 611 defines two levels of quality. The highest, Class I, designates ‘high performance’ finishes at least 18 µm (0.7 mils) thick and are used in exterior applications receiving periodic maintenance, such as curtain walls. The second level, Class II, encompasses finishes between 10 µm (0.4 mils) and 18 µm thick used in interior or exterior applications receiving regularly scheduled cleaning and maintenance, such as storefronts.
A related standard, AAMA 612-17a, describes test procedures and performance requirements for anodized finishes combined with transparent organic coatings.
Solar reflectivity enhances energy efficiency
Another supplement to the AAMA 2603-17a/2604-17/2605-17a series, AAMA 643-16, Voluntary Specification, Performance Requirements and Test Procedures for Solar Reflective Finishes, describes a solar reflectance test per ASTM C1549-16, Standard Test Method for Determination of Solar Reflectance Near Ambient Temperature Using a Portable Solar Reflectometer, procedures and performance requirements for pigmented, organic, solar reflective coatings keeping the coated surfaces cooler than they would be with standard coatings. It applies to coatings for aluminum, as well as fiberglass or cellulosic-composite profiles particularly reflective to sunlight, and so tend to keep buildings cooler. This is a boon to commercial buildings, that are cooling-intensive and do not require much heating.
Using AAMA finish standards as a guide, specifiers can select a painted coating or anodized finish to meet a project’s performance and long-term durability targets based on the building’s location and function, the desired aesthetic appearance, and the aluminum products’ proximity to dissimilar metals.
Steven Saffell serves as American Architectural Manufacturers Association’s (AAMA’s) technical director where he oversees the standards, product certification and codes, and regulatory affairs aspects of the association. Saffell’s background is a tapestry of architectural firm work, modular design, as well as residential and commercial fenestration experience. Saffell also spent three years teaching as an adjunct professor. He is experienced in managing technical teams, including employee development, operational strategy, and financial management. With 32 years of experience, Saffell previously worked with Simonton Windows and Ply Gem. He can be reached at ssaffell@aamanet.org.