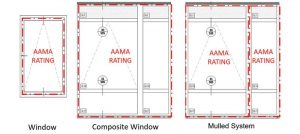
Mulled window systems
Mulled systems consist of multiple prefabricated window units, each with its own rating and often with relatively lightweight flexible frame extrusions, which are then combined in the field by fastening and sealing them together or attaching them to less flexible sub-framing members. These members include vertical mulls, horizontal transoms, subsills, head receptors, full perimeter receptor frames, or any combination of the above. This contrasts with storefront and curtain wall, which can also be used to fill a punched opening, but typically consist of deeper, heavier extrusions, and usually require a greater degree of field assembly and installer expertise to construct.
Each mulled system is assembled from multiple units, each with their own rating.2 This contrasts with composite windows (e.g. a casement over fixed configuration), which are similar in appearance, but are factory-fabricated with a shared mullion between each lite, so each sub-unit could not exist on its own if disassembled. The key difference for specifiers is that composite units carry one overall AAMA rating for the entire assembly while mulled systems often do not.
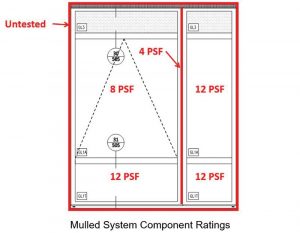
Since manufacturers often need to introduce a new component which is not common to the windows being mulled, this introduces new joinery and modes of deflection to the assembly, which were not present when the constituent windows were tested individually. However, since sub-framing is not directly addressed by NAFS-17, the connection between the window and its sub-framing may have a lower air, water, or structural performance rating than its constituent windows or no rating at all.3 The authors have encountered numerous projects where accepting an unrated mulled system without fully understanding these limitations resulted in air and water infiltration issues that did not meet performance expectations. Figure 3 shows examples of how this can impact performance depending on the configuration.
Designers navigating the complexities of mulled windows on their projects can easily find themselves in uncharted waters with few tested product options and unforeseen air, water, or structural issues. Several methods exist for charting a path past these risks such as avoidance strategies early in design, understanding and specifying a more appropriate performance standard such as AAMA 450-20, and as a last resort, accommodating unrated components via a program of careful shop drawing review, laboratory testing, and field testing to address any “weak link” sub-framing components that could compromise an installation’s performance.
Avoidance
Planning around performance requirements should begin early in design. An important rule of thumb to remember is product options and performance tend to decrease as opening size increases. A good first step to a successful project is to carefully consider opening sizes early in design and size each based on the limits of a preferred window product line with a known track record of success to ensure the initial design is realistic.