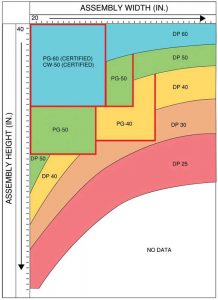
Incorporating AAMA 450 can be as simple as specifying a sub-framing that carry an equal or greater rating then its fenestration when tested in accordance with AAMA 450-20, and specifying a suitable AAMA 450-20 tested basis of design product. As an example, Figure 4 shows a generic mulled system performance grade chart. The chart can be interpreted by finding the mullion height and width of a mulled assembly to find the expected performance. The curved regions with a design pressure (DP) label indicate performance estimates established by calculation only, whereas the rectangular regions that include performance grade (PG) labels represent the largest size of each product physically tested. This chart also shows that even when using mulling, there are limits to how large a combined assembly can be. For example, a 1,625 mm (64 in.) wide by 2,159 mm (85 in.) tall window could be rated PG-80, but could only achieve a DP-20 performance when mulled together to span a much larger opening.
While AAMA 450 performance charts provide a user-friendly way of reviewing simple mulled systems, it has limitations. Unusual components designed for a specific project are often not tested. Similarly, end conditions where mullion components interface directly with perimeter flashings are often overlooked as well and can compromise the mull’s drainage strategy. Thus, even with a rated assembly, it is still important for the design team to carefully review the bid qualifications, test reports, and shop drawings of manufacturers to remain vigilant for these discrepancies between the tested system and the proposed system that could otherwise be overlooked.
Accommodation
The authors have observed the decision to use a mulled system is frequently driven by a contractor or manufacturer, either in a design-assist role early in the project, or as a substitution request due to perceived cost advantage. In cases where projects change to a mulled system instead of the original design intent, it can require significant effort from the designer to carefully review the system, identify its risks, and work with the project team to accommodate the changes if accepted.
The first step would be to request all available cut sheets and test data for a proposed system, including test reports documenting the ASTM E283, E331, and E330 laboratory tests necessary to validate air leakage, water penetration resistance, and structural performance respectively. If the proposed sub-framing is not included in these test reports, additional AAMA 450 certifications should be requested. If such reports are unavailable, some manufacturers may be able to perform additional analysis at the request of the design team on a project-by-project basis.
Proposed manufacturers should be vetted as early as possible to identify their limitations and account for them in design choices. Further, if the selection of the window manufacturer is driven by the contractor on a cost basis, designers must carefully research any substitution requests to confirm they are in fact equal to the specified system and flag any differences the owner or contractor may be unaware of.