When using a primerless membrane, ensure primer is not required on all substrate materials. In some instances, differing substrates or different temperature and humidity conditions may require a primer for
a primerless product. Unfortunately, this may not be apparent until the air barrier loses adhesion after installation. Having to then prime the surface and re-install the membrane can cause unplanned delays and additional labor costs. Last minute design changes may result in substitution of a planned material, making it even more critical to have a primerless membrane tested for a wide range of substrates. Rather than relying on manufacturers’ published claims, it is a good idea to request independent testing data to validate the barrier’s primerless bonding performance on various materials. The data can be attained through the third party testing laboratories, as they can test the barrier’s performance without using primer on various substrates and at various temperatures.
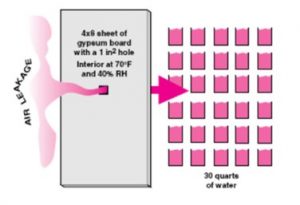
Testing air barrier durability
Since most air barriers will be installed behind exterior cladding and not readily accessible, it is important to select a long-standing membrane. ASTM E2357 defines a standard test method for determining air leakage rate (permeance) of air barrier assemblies.7 This involves constructing a specimen wall assembly, including a window opening with flashing and typical wall penetrations such as pipes, vents, and ties, and roof and concrete foundation tie-ins (Figure 1). Varying positive and negative pressures are applied to the specimen wall and air leakage is measured. As noted previously, the air barrier assembly must have an air leakage rate (permeance) no greater than 0.2 L/s/m2 (0.04 cfm/sf) at a pressure difference of 0.075 kPa (75 Pa).
ASTM E2357 is designed to provide a realistic evaluation of air barrier assembly performance and helps verify whether the components are compatible with each other. The method has been adopted by the ABAA as part of its acceptance criteria.
However, some manufacturers have gone further, testing wall specimens under real-world, field conditions over long durations of a year or more to assess the effects of time, temperature, and humidity changes on air barrier performance. Leak tests are performed at regular intervals. At the conclusion of the test, the exterior siding is removed to assess any areas of air barrier failure, such as at laps, seams, or penetrations, and any damage caused by common factors. Reviewing a manufacturer’s data from such a long-term field test can provide additional assurance regarding the air barrier’s long-term performance in the real world.