
Photos courtesy Copper Development Association
Fully redundant electrical systems
Copper also plays a role in the reliability of the Involta data center in Boise, Idaho; the 2915-m2 (31,400-sf) facility has an all-copper wiring and interior bonding and grounding systems. There is one grounding system with uninterrupted electrical continuity throughout the entire center. All of the center’s electrical equipment, including information technology (IT) equipment, operates at a single, uniform ground potential.
Constant expansion and contraction under ‘load/no-load’ conditions can cause non-copper materials to creep—a process resulting in the loosening of terminations. In turn, loose connections tend to heat up, and will sometimes arc dangerously. Copper may cost a little more initially, but its low maintenance and reliability make it cost-comparative to other common materials over time.
Power distribution buses are used in the center’s carrier rooms, where servers for Internet service providers (ISPs), networking, and several other communications companies are installed. Bonding conductors are routed to traditional copper grounding bars attached to rack frames. The racks themselves are bonded to copper buses with heavy-gage copper cables, and then to the master ground bus (MGB). Heavy-gage grounding conductors connect power distribution systems with copper grounding bars placed at convenient locations in the data rooms and mechanical spine.
An AWG 2/0 buried bare copper ring completely surrounds the center. Bonded to the ring at periodic intervals are 3 m x 19-mm (10 ft x ¾-in.) copper-clad grounding electrodes. Access ports along the ring allow for inspection of such items as lug tightness and ground resistance. All the facility’s electrical and lighting systems are connected to this ring. Mechanical equipment, water, gas, and telephone systems are also properly grounded and do not share branch circuits with IT systems.
Also bonded to the ring are copper down-conductors from the rooftop lightning protection system. They consist of interconnected, regular-spaced termination devices (i.e. lightning or Franklin rods) mounted along the roof’s periphery. This system fully protects the center from expensive damage, downtime, and data loss.
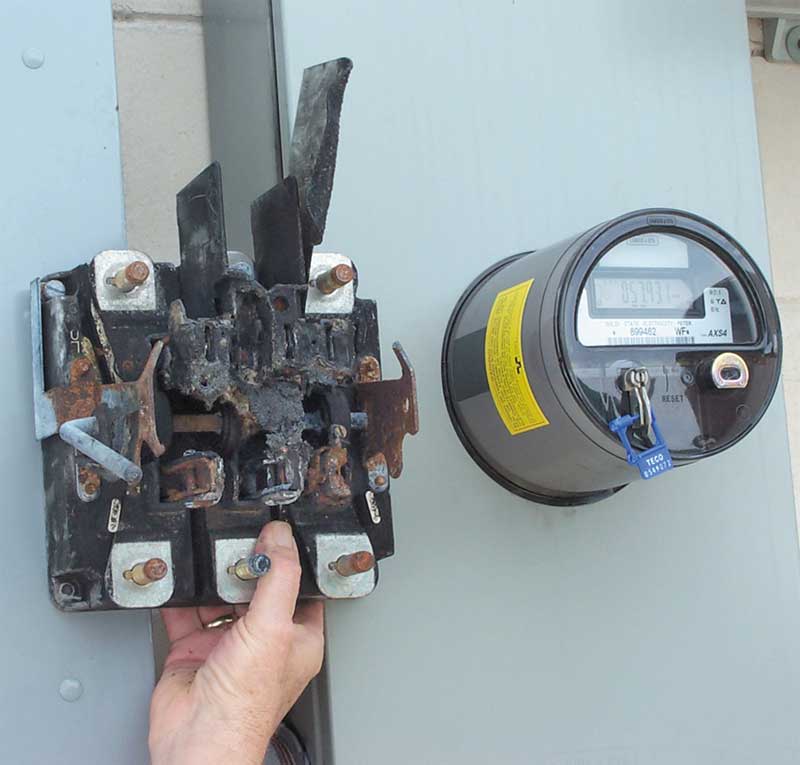
Redundancy also helps Involta maintain 100 percent uptime for its tenants. In data center terms, reliability means having built-in redundancy—usually duplicate equipment and/or systems for any mission-critical need. The center is equipped with a pair of 1-MW emergency generators serving its two power feeds. The generators are load-tested monthly and no-load-tested weekly, with results carefully documented. Should there be a utility failure and one generator goes down, the backup generator can support the critical load. Backing up the power feeds to data halls are two 500-kW uninterruptible-power-supply (UPS) units equipped with sufficient battery capacity to keep the critical load operating for 50 minutes based on the current critical load. One beneficial feature of a dual system is it enables personnel to shut down either feed if the other one requires maintenance or repair. Equipment on the system then remains completely operational, and the center’s 100 percent uptime is preserved.
Since systems can degrade over time, connections loosen, contact resistances rise, and loads can change—these may produce unexpected effects. Grounding connections and resistance should be checked on a fixed schedule and changes investigated as needed. Power quality should be monitored to ensure clean waveforms and voltage stability. Emergency generators and UPS units should be periodically tested. As the saying goes, you do not get what you expect—you only get what you inspect.