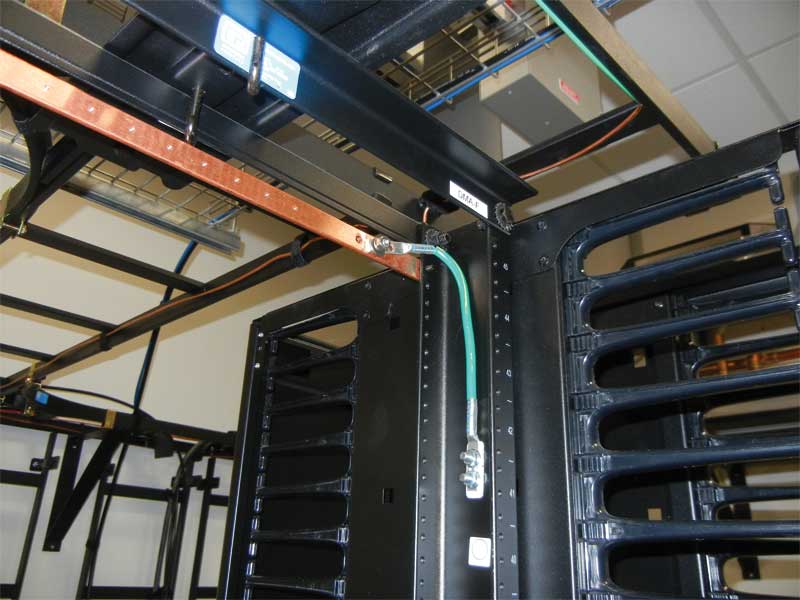
Helpful power quality techniques
In cases where power quality problems are encountered in an existing facility, careful study will be necessary to determine the best course of action. Solutions may be as simple as moving some loads between branch circuits or minor rewiring. In difficult cases, professional engineering assistance is recommended. The Copper Development Association (CDA) also suggests the following steps to help prevent power quality problems from occurring.
Copper conductors
There is less risk of failures related to power quality because of copper’s superior connectablity. Poor-quality connections are a major concern, especially when multiple contractors of unknown workmanship modify the system. This is where all-copper wiring excels over other materials.
Exterior ground ring
The use of an outside copper ground ring, sometimes combined with vertical electrodes, helps achieve low impedance from the building’s grounding system to the earth itself, and a convenient means of connecting various grounds leading from the building.
Segregation of sensitive loads
Power-sensitive equipment should be placed on separate dedicated branch circuits emanating from separate panel boards, fed from separate feeders back to the main service entrance. The neutrals and grounding conductors also need to be kept separate. One should never mix sensitive equipment with standard loads, motor loads, or outdoor loads.
Limited number of outlets per circuit
Three to six outlets per circuit maximum is recommended instead of the 13 permitted by the National Electrical Code (NEC) on a 20-amp circuit. This will minimize the amount and variety of sensitive equipment sharing circuitry. It tends to reduce voltage drop, decrease the chance for interaction, and leave some room for later growth or equipment changes.
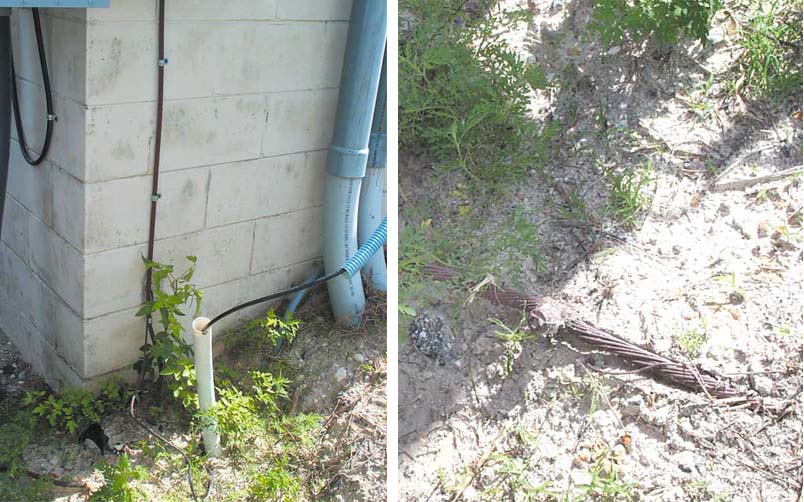
Conduit as a ground path
A metal conduit, properly grounded, provides shielding of the conductors from radiofrequency (RF) energy. However, one should not omit the grounding conductor (i.e. green insulated copper wire), irrespective of the conduit material, as it is needed for safety, as well as assurance of a continuous, low-impedance path to ground. The grounding conductor should be at least as large as the phase conductors and is run inside the metal conduit, rather than outside.
Voltage drop
Although NEC allows up to a five percent voltage drop on the combined branch and feeder circuits, recommended practice is to design for no more than a three percent voltage drop at full load on the combined circuits feeding sensitive equipment. This means conductor gages should often be larger than required by code minimums. However, a side benefit of larger conductor gage is larger conductors frequently save enough energy, due to their lower resistance, to compensate for higher initial cost, with a short payback.
Depth of grounding
Where there is insufficient real estate with which to work, or under conditions of unusually high ground resistivity, deep grounds may be required. Long copper ground rods, sometimes hundreds of feet long, in bored holes, are not uncommon in some cases. (To achieve 5 ohms, lengths of 15 to 30 m [50 to 100 ft] can be required. Case studies are available at www.copper.org/applications/electrical/pq.)
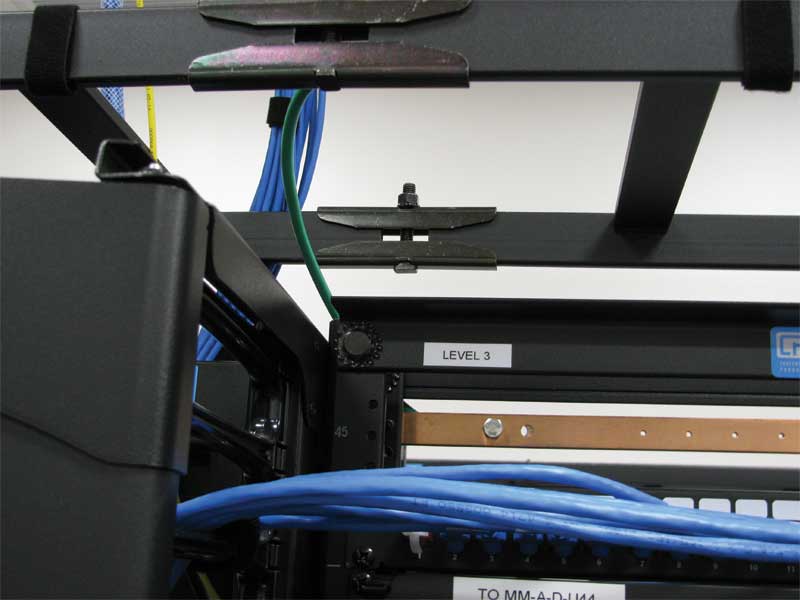
Surge and lightning protection
Lightning protection systems provide a low-impedance, easy path for the lightning energy to flow. This maximizes current in the lightning protection system, but it also minimizes current to the sensitive equipment. Lightning systems and surge protection devices must be connected to a low-impedance grounding electrode system to operate properly. As mentioned, the grounding resistance should be checked upon installation, and again periodically—annually or semiannually, depending on experience encountered. Five ohms to earth or less is recommended by Institute of Electrical and Electronics Engineers (IEEE) and others.
The ‘clean ground’ myth
Installers sometimes request a so-called ‘clean ground’ for their equipment, in the mistaken belief it does not need to be connected to other equipment within the environs. This practice is dangerous, as it establishes multiple paths to ground, thus using the earth as a conductor. In cases like these, adjacent equipment may be at different voltages. Also, by having separate grounds, there may be a shock hazard. All equipment must be connected to one common grounding system.