by Rich Rinka
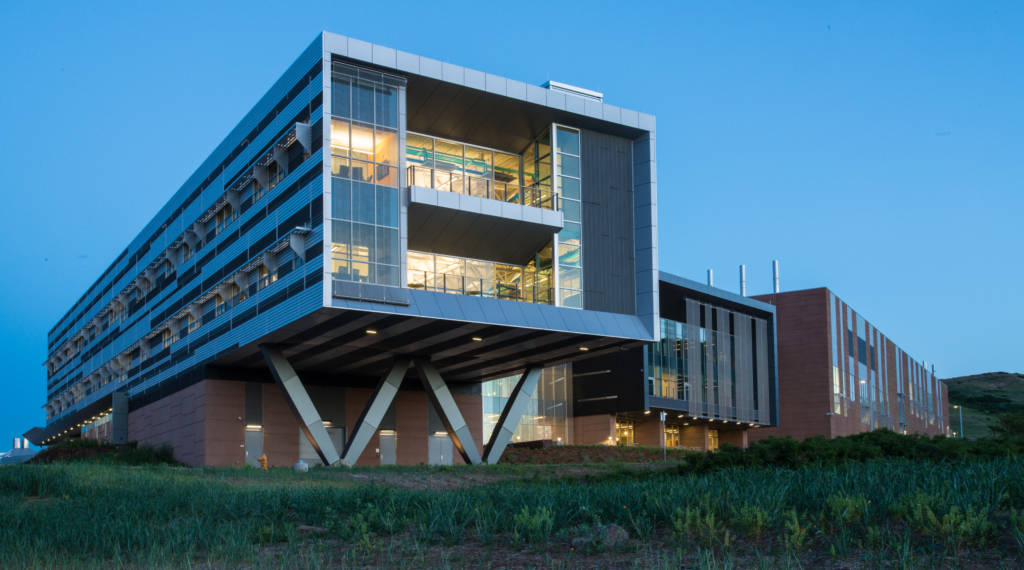
All photos © Dennis Schroeder
As energy concerns continue to infuse design considerations, the use of shading devices to help mitigate the effects of solar heat gain has become more common. However, in temperate climates, the sun’s direct rays can turn on a dime into onslaughts of ice or snow, especially in transitional seasons.
As roofers know, winter weather can impose some formidable loads on structural elements. The same is true of sun-shading devices projecting away from the building wall; they, too, can collect weighty ice and snow or be impacted by icy hunks falling from upper stories, parapets, or the like. Like wind-loading, this is an inherent and inevitable characteristic of the built environment.
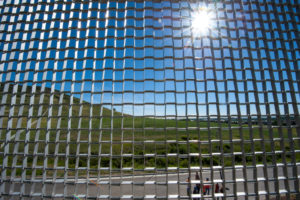
To help ensure a shading device can withstand such stresses, a test method has been devised for both static and impact loading. American Architectural Manufacturers Association (AAMA)-514-16, Standard Test Method for Static Loading and Impact on Exterior Shading Devices, provides a means for specifiers to evaluate exterior horizontal shading projections. The standard describes these projects as those 101 mm (4 in.) wide or greater, which are permanently installed, immobile, and non-retractable. They should provide sufficient resistance to static and impact ice and snow loads to be confidently prescribed as suitable for use on a specific project. Rather than providing protection from these elements, such projections should be considered both sources and targets of falling ice and snow.
Based on sources from the American Society of Civil Engineers (ASCE), the U.S. Army Corps of Engineers (USACE), and the U.S. Geological Survey (USGS), the AAMA-514 test method focuses on determining a design load. In this case, that load is the most unfavorable combination of dead load, weight of ice, wind load, wind-on-ice, and snow load, using the allowable stress design approach.
The testing imposes both static and impact loads related to the design load to verify the shading device will not bend, permanently deflect, or disengage from the building. It is important to note the test is not relevant to human impact loads or static loads from access, step, or purposeful attack.
For the static-load portion of the test, sandbags stacked upon the installed device replicate a uniform or triangular distributed static load simulating the combined effects of wind, snow, ice, and drift. Static load is measured at both the design load and twice that level. To pass, glass cannot break; nor can any components fall from the specimen. After the load is released, the permanent set for the louver blade and supporting mullion is calculated and cannot exceed 0.2 percent of the span length.
For impact testing, the most representative impactor is ice itself, which can be conveniently formed into an appropriate shape in a freezer, using a 152-mm (6-in.) diameter sleeve or form. The prescribed impactors consist of nine cylinders of freshwater ice weighing 4.5 to 9 kg (10 to 20 lb).
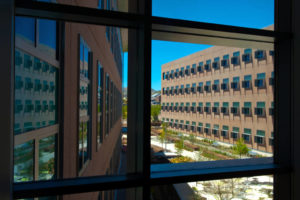
The specifier should determine the appropriate impact energy based on the anticipated buildup of ice or snow and the expected free-fall height. Unless otherwise specified, 406.7 Nm (300 ft-lb) should be used. (If higher loads or more stringent pass/fail criteria are deemed appropriate, this test method may not be applicable.) To impart the specified impact energy, the impactor is suspended 2.3 to 9.1 m (7.5 to 30 ft) above the specimen. By altering the height of the drop, it is possible to deliver an impact energy of 203.4 to 406.7 Nm (150 to 300 ft-lb). The impact is applied three times to each end and the center of the specimen, and at other locations specified.
After testing, there can be no disengagement of the shading device, its components, the system to which it is attached, glazing, hardware, or fasteners. If disengaged by impact, the design must prevent complete release of the device or of associated components other than the original impacting ice or snow. Visual inspection can disclose no significant damage (e.g. distortion, deflection or denting, glass breakage, or fastener breakage).
Net and residual deflection for the louver blade and supporting vertical mullion must also be calculated. To pass, residual deflection (i.e. deflection after the test load is removed) at either end of the shading device assembly cannot exceed 9.5 mm (0.375 in.) or one percent of the cantilever dimension perpendicular to the wall, whichever is greater.
Testing such as this helps specifiers include shading devices without concern for the impact of less-than-sunny weather.
Rich Rinka serves as the American Architectural Manufacturer’s Association’s (AAMA’s) technical manager for standards and industry affairs. Prior to coming to AAMA, he worked in the industry as a field technical engineer for a component supplier and served as chair of the AAMA 800 Maintenance Committee. During his time in product development for the automotive industry, Rinka developed and still holds four patents related to sealants. He may be reached at rrinka@aamanet.org.