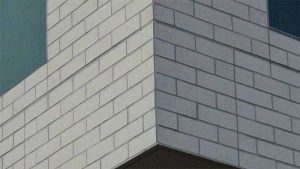
QC could be employed to verify the specified products are stored and used correctly and the work is being performed according to the specification, manufacturers’ directions, and industry standards.
Undoubtedly, it costs more to do diligent QA testing and to implement a meaningful QC plan. In this author’s experience, QA and QC could add approximately two percent to the total cost of the application in projects similar in scale to the Brickyard Campus. Consultants are often brought into projects only after ill-informed decisions have been taken and QA testing cannot be done without causing delays. In the case of the Brickyard Campus, the developer was committed and willing to pay the price to ensure the building was constructed correctly. Per their directions, this author was hired through the GC about two years prior to the completion of the project.
This author began by reviewing existing project plans and specifications for the installation of the thin brick tiles and then performed the following work:
- evaluated the specified thin brick to verify its suitability for the project;
- prepared installation guidelines as well as a MasterFormat specification for the installation
of the thin brick over the plaster substrate; - assisted in selecting the installation company;
- performed QA testing of the thin brick before and during installations, including the mockups;
- reviewed shop drawings and submittals by the installer; and
- implemented the specified QC plan.
Installation system
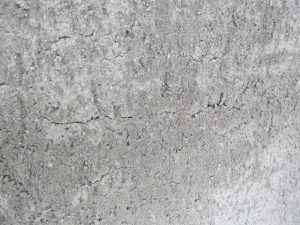
In this author’s experience, it is best to specify a single source installation system as they ensure compatibility between the products and usually come with extended warranties. For instance, the installation system employed in the Brickyard Campus project qualified for a 15-year labor and material warranty. It is advisable to specify ‘or equal’ performance as long as manufacturers can provide the required performance and warranty.
Architects often provide a reference specification that only mentions industry standards and building codes. They also tend to rely on calling out the standards without providing detailed execution instructions, thereby deferring responsibility to the installer. Reference standards do not provide the detailed installation methods an installer needs to know. The installer is a craftsman with the skills to do the work, but they need the architect to specify the method. In this author’s experience, the best way forward would be the use of the Tile Council of North America (TCNA) Handbook for Ceramic, Glass, and Stone Tile Installation that will help specifiers select and reference in the documents the appropriate installation method. The TCNA installation methods also apply to adhered thin brick applications.
It is important to note labor and material warranties are not like ‘no-fault insurance’ policies. Products have to be installed per manufacturers’ directions and industry standards for the warranty to be valid, and therein is the challenge. As mentioned earlier, installers of thin bricks are not fully aware of industry standards or manufacturers’ directions and rely on their on-the-job training experience. This at times may result in subpar installations. Therefore, it is important to have a QA process and QC plan to ensure tradespersons are knowledgeable and the products are being stored and installed correctly.
Installation systems always require the exterior veneer substrates to be structurally sound and meet industry and local building code requirements such as:
- deflection must not be more than L/600 along framing and between framing spans;
- adequate movement (control) joint design and placement as per ASTM C1063, Standard Specification for Installation of Lathing and Furring to Receive Interior and Exterior Portland Cement-Based Plaster; and
- transitions and penetrations must be properly flashed and waterproofed.
The liquid-applied waterproof/crack isolation membrane employed in the Brickyard Campus project was not mandated by building standards, but provides additional levels of protection as plaster finishes tend to have shrinkage cracks. ANSI A108, American National Specifications for the installation of Ceramic Tile, does not allow the installation of tiles over cracked substrates. The waterproof membrane mitigates shrinkage cracks, so they do not telegraph through the thin brick. It also provides an additional layer of waterproofing to prevent the plaster substrate from absorbing and retaining moisture, thereby avoiding efflorescence staining, spalling, and potential water intrusion problems with thin bricks. Additionally, it is important to flash at all membrane transitions and penetrations to make it watertight. Breathable liquid-applied membranes are recommended as they are more user friendly, provide high bond strength between the substrate and the thin brick adhesive, and practical for installers to apply (Figure 3).