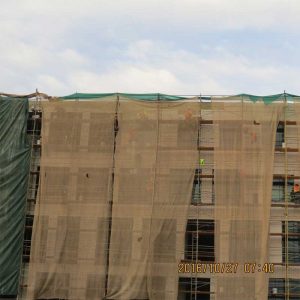
ASTM C482 uses a cement paste as an adhesive over a mortar block. The test can be modified in the laboratory and used with the specified adhesive and substrate material. However, it is not an in-situ test.
There is no formal test protocol for a field shear bond test for any type of tile, let alone a thin brick. More than 10 years ago, this author developed a shear bond test apparatus and protocol for tile and stone with the help of an engineering firm. The ASTM C18 Stone Committee is currently in the process of voting on this protocol.
This shear bond strength test protocol was employed on the Brickyard project. There are often concerns on whether bonding to a membrane is the weak
link of the thin brick assembly, so by performing the shear bond test, the project team was able to confirm the results met the building code requirement. It also met the specified performance requirement of 689 kPa (100 psi) minimum shear bond strength value. The thin brick on the mockup and on the two buildings exceeded the specification requirements for the thin brick bond strength to the assembly. The average shear bond strength on the two buildings was 1393 kPa (202 psi) and 1020 kPa (148 psi) with a high of 1878 kPa (268 psi). The point of failure was mostly a combination of cohesive failure within the plaster substrate and the thin brick. Rarely was it cohesive in the membrane. Thus, the bond strength of the thin-set adhesive to the thin brick was actually higher than those values to some degree (Figure 4).
Another QA requirement in the specification was to verify that the tile installers had adequate supervision and understood industry standards. The installation company was to provide at least one full-time, non-working laborer and a qualified supervisor per building during the installation process. All the 80-plus union tile setters and finishers had to take the five-hour Tile Installer Thin-set Standards (ITS) Verification online course produced by the University of Ceramic Tile and Stone (U of CTS). This course is available in English and Spanish. A highlight of this process was installers talked about what they learned and were enthusiastic and cooperative during the QC process. It created a culture of quality within the company as everyone ensured that the installation process was implemented according to industry standards.
Quality control
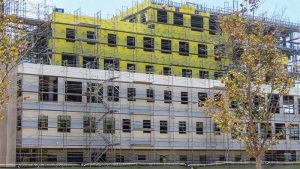
In this author’s experience, the QC section of the specification in Part 3–Execution is often left out. Even though QC is an added cost, it is cheap insurance when one considers the cost of failure and potential liability claims.
Some of the key steps requiring QC at the installation stage are:
- inspecting substrates prior to the application of the waterproof/crack isolation membrane to ensure it meets the respective requirements;
- verifying the membrane is being installed correctly and at the required thickness (Figure 5);
- verifying there is adequate adhesive contact and coverage and it is being used according to the manufacturer’s directions; and
- ensuring installation products are being stored properly and used under the manufacturer’s required conditions for temperature and other climatic conditions.
When temperatures are higher or lower than usual, provisions must be made to perform the installation within the manufacturer’s requirements. A shading barrier must be erected on the scaffolding in order to mitigate the impact of sunny and windy conditions (Figure 6). During the cold and/or wet seasons, there must be some sort of tenting and heating to control temperature. Stored and newly installed products must be kept out of the rain and other harsh, problematic weather conditions (Figure 7).
The QC process can also confirm adequate adhesive contact is achieved. Section 1404.10, “Adhered Masonry Veneer,” of the International Building Code (IBC) requires each unit to be fully bonded. The tile and stone industry require 95 percent contact with voids no larger than 1290 mm2 (2 si » size of golf ball). Voids must be minimized for the following two reasons:
- more voids result in weaker attachment; and
- voids collect moisture from rain or condensation, thereby leading to efflorescence staining on the surface of the thin brick or spalling from moisture freezing and expanding during freeze/thaw weather conditions.