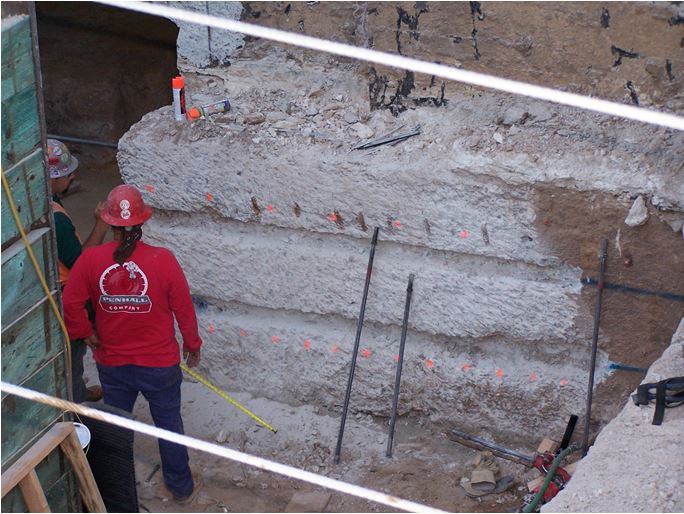
by Martin Ruch and Jim Collins, PhD, PE
In a previous article, the authors discussed the major physical properties of epoxy types, and examined how to read such products’ manufacturer’s printed installation instructions (MPII) to ensure one is not selecting an anchor or repair product that will have a dangerously compromised bond.
Indeed, when specifying epoxies, there are a few important things to check on the product label, such as:
- recommended substrate—concrete or concrete masonry unit (CMU);
- certifications, such as International Code Council Evaluation Service (ICC-ES), International Association of Plumbing and Mechanical Officials (IAPMO), ASTM, and Department of Transportation (DOT);
- whether good for wet or saturated conditions;
- expiration date;
- temperature range for nozzle, working, and cure times; and
- installation instructions.
The guideline is to find a product meeting the requirements of a specific application.
Further, installers need to determine whether the ‘substrate’ installation into unsound, weak, or contaminated concrete. Damaged concrete can affect the bond’s strength and can also reduce the capacity of the concrete to resist the loads applied to the anchor, causing premature concrete breakout failure. Epoxy is not magical—it is only as strong as the substrate to which it is bonding.
Installers need to drill the correct hole diameter when setting bolts in epoxy. The correct dimensions are always stated in the manufacturer’s technical data sheet. Generally, it will be 1.6 or 3.2 mm (1/16 or 1/8 in.) larger than the anchor diameter. If the hole is too large, the capacity of the anchor can be reduced. If the hole is too small, it can be difficult for the installer to insert the anchor and still allow room for enough epoxy to form a bond.
Installers need to clean the hole properly. Most manufacturers recommend the hole to be blown out and cleaned with a specific brush. These brushes also serve to roughen the interior surface of the hole for increased bond strength so specifying the recommended diameter is important. When the MPII is unavailable, the best practice for installers is to drill, blow, brush, blow, brush, and blow.
Installers needs to check the concrete integrity. Ideally, a bonded anchor should be installed into concrete of known compressive strength. Engineers who specify epoxy anchors also specify the compressive strength to ensure the epoxy can achieve its published bond strength.
When the compressive strength or overall integrity is unknown, they sometimes require field testing of the embedded anchor to determine if the concrete is good enough. One must never specify an epoxy anchor into concrete that appears to be unsound, weak, contaminated, or otherwise substandard. Also, as a general rule, concrete should always be left to cure for a minimum of 21 days before installing bonded anchors.
Finally, any epoxy anchors specified for seismic loads are tested to a specific set of design standards and require a design professional to be properly designed per the applicable building code.
Jim Collins, PhD, PE, is MiTek USA’s manager of engineering projects. He has worked 14 years in the engineered wood industry and eight in the truss industry. A former director of engineering at International Code Council Evaluation Service (ICC-ES), he has been a licensed professional engineer for 25 years, and is a member of American Society of Civil Engineers (ASCE), the American Concrete Institute (ACI), and Concrete Anchor Manufacturers Association (CAMA). Collins can be contacted at jcollins@mii.com.
Marty Ruch is vice-president of retail sales and merchandising for MiTek Builder Products. He has more than a decade of experience in commercial/industrial sales and spent 14 years working in the building materials industry with Gibraltar Industries and MiTek in marketing and product development roles. Ruch can be reached at mruch@mii.com.