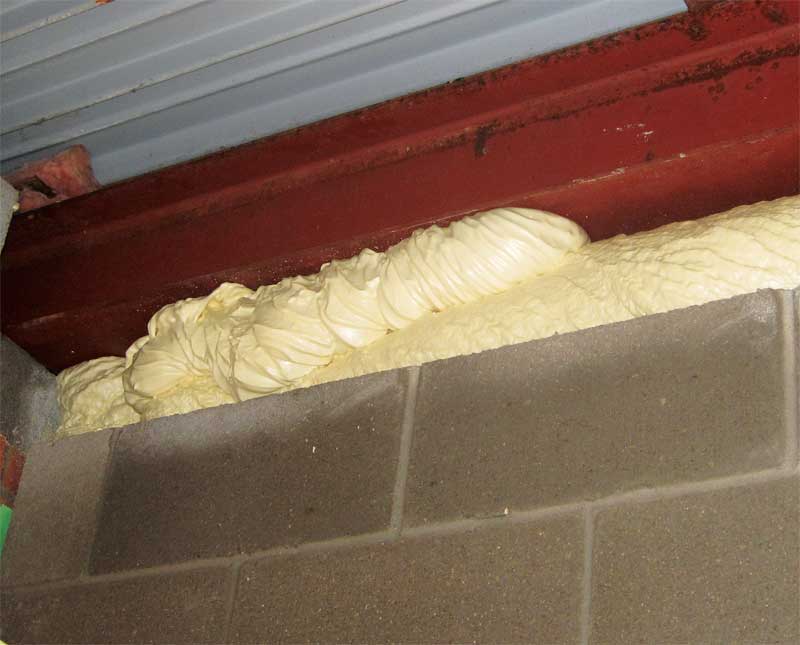
Air barriers and moisture retarders
Better workmanship could improve the watertightness of the mortar joints, but an air barrier and moisture retarder are needed to prevent moisture from entering the building.
Many designers recognize the need for a moisture retarder on the exterior face of the CMU, but tend to overlook the importance of an air barrier. According to a study by the National Institute of Science and Technology (NIST), the energy savings from a well-constructed air barrier can be as much as 33 percent of the annual energy cost. (Visit www.nist.gov/news-events/news/2005/10/simulations-predict-savings-more-airtight-buildings for more information.)
Cavity wall designs should place an air barrier and moisture retarder on the cavity face of the CMU to avoid creating a gap where moisture could condense between the two materials. Products with both air barrier and moisture retarder properties eliminate the need to install two separate assemblies.
Moisture retarders should be on the warm side of the insulation to prevent moist, warm interior air from condensing in the insulation in winter climates and on the exterior side of the insulation in hot, humid climates. This is a conundrum for the architect to resolve in regions experiencing some
of both extremes.
Insulation in cavity walls
Three types of insulation are used for masonry
cavity walls:
- extruded polystyrene (XPS) moisture-resistant rigid board insulation;
- foil-faced polyisocyanurate (polyiso) rigid foam insulation; and
- closed-cell sprayed polyurethane foam (SPF) insulation.
XPS insulation offers moisture resistance and long-term durability. It is lightweight, easy to handle, and can be cut into smaller pieces. XPS comes in 400-mm (16-in.) widths, 1.2-m (4-ft) lengths that can be pressure-fit between the wall ties. A misgiving about XPS is its rigid configuration makes it difficult for enclosing irregular shapes and openings for a complete air barrier.
Dual foil-faced polyisocyanurate rigid foam insulation in 400-mm (16-in.) widths and up to 3-m (10-ft) lengths is recommended for cavity wall insulation. It has a higher R-factor than XPS at the standard test temperature of 24 C (75 F). However, studies have shown the R-value of polyiso steadily declines as the temperature goes below 15 C (59 F). (Consult Building Science Corporation’s Info-502, “Temperature Dependence of R-values in Polyisocyanurate Roof Insulation.”)
Closed-cell SPF insulation has sound/air barrier and moisture retarder properties. The adaptability of SPF to foam into irregular openings and cover irregular shapes makes it a potential complement to the rigid products in the perfection of air barriers. This adaptability helps simplify the design of cavity drainage walls, air-vented cavity walls, and especially pressure-equalized cavity walls.
Cautions about SPF have been published in ASTM STP1549, Dimensional Stability Considerations in Spray Polyurethane Foam Air Barriers:
One of the most significant problems experienced recently in the use of SPF for air barriers is short- and long-term shrinkage variations in the foam system, particularly when applied to the exterior of the building. Such shrinkage can result in damage to flashings, closures, and terminations in exterior veneer systems. This document explores the potential causes of excessive shrinkage in SPF systems, the physical changes that can cause the problem, and best practice measures to minimize the potential for significant problems during installation.
In a paper published in 2013, the Brick Institute of America (BIA) reported concerns raised in the ASTM paper had not been addressed by sprayfoam manufacturers. Regardless of these concerns, SPF has an important place in the design of pressure-equalized rainscreen walls and air-vented cavity walls to make airtight building envelopes.