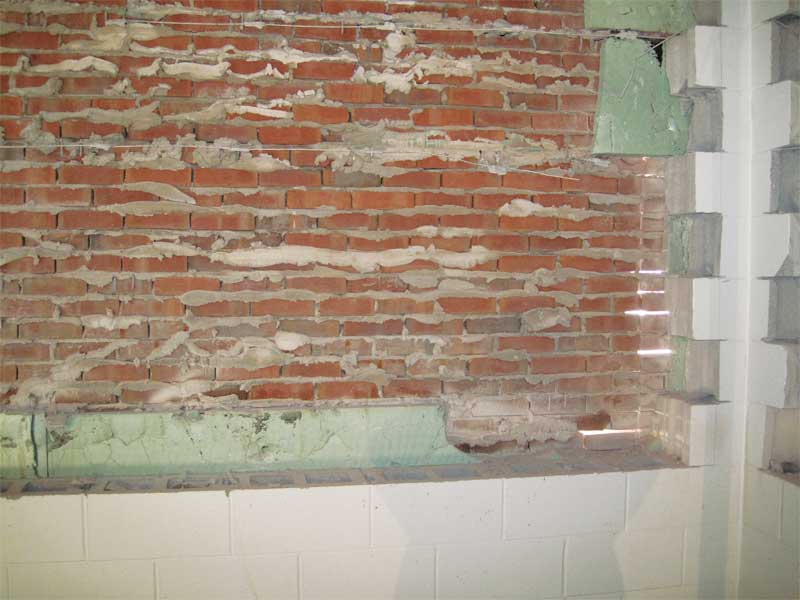
Workmanship
Every effort should be made to weatherproof brick veneer joints by improving the workmanship. There are two characteristics of the bond between brick and mortar—extent and strength.
The extent of bond, the more important of the two for weatherproofing joints, refers to how completely the mortar is spread in intimate contact with the
brick across the entire surface of the joint—a result of the mason’s skill and mortar’s workability. An experienced mason can feel if the mortar is sticking to the brick properly and adjust, if necessary, by rewetting brick or retempering mortar that has gotten too dry on the board.
A few more workmanship practices can improve the efficiency of cavity wall construction. Masons can reduce mortar dropping by sloping the mortar in the bed joint away from the cavity and buttering the head joint more carefully. Additionally, one must not slush mortar on the joints. Mortar joints on the cavity side of the CMU must be cut flush to allow rigid insulation to fit tight to the wall and prevent creating a hollow space where moisture can collect.
Issues for the designer
- The roof flashing over the top of the masonry wall must come down far enough on the face of the brick wythe to prevent rain from blowing up under the flashing and entering the cavity from the top. Rain will be blown up the wall under the flashing at a rate of 22 mm (1 in.) for each 16 km/h (10 mph) of wind speed.
- Cavities for pressure-equalized rainscreen walls must be kept as narrow as practical to facilitate the increase of air pressure in the cavity.
- Due to their hidden condition and potential for allowing a continuous flow of moisture-laden air into the building, openings between the top of a masonry wall and a hip roof condition must be filled with a permanent product, not stuffed with batt insulation.
- The brick wythe should rest on a foundation ledge below the floor level in order to prevent rainwater from being driven under the weep vent flashing and into the building. The same attention must be given to brick ledges in multistory construction.
Conclusion
The design and construction of a successful pressure-equalized rainscreen cavity wall is a challenge for the designer and inspector. This type of wall is also expensive to build. It is difficult to imagine construction drawings for a large commercial building anticipating all the potential breaches in the air barrier wall requiring special treatment to make an airtight barrier. The alternative would be a large contingency budget and a considerable number of change orders to deal with unforeseen conditions—something most designers and owners prefer to avoid.
This makes a well-designed vented cavity wall with an air barrier, moisture retarder, and a partial compartmentalized cavity a good alternative to a pressure-equalized cavity wall. The air-vented wall anticipates some moisture will enter the cavity and provides air circulation to dry it out.
Paul Potts is a technical writer, owner’s representative, and construction administrator. He has worked in the construction industry as an independent contractor and administrator for architects, engineers, and owners in Michigan. Potts can be contacted at paulpotts1@comcast.net.