by Ted Winslow
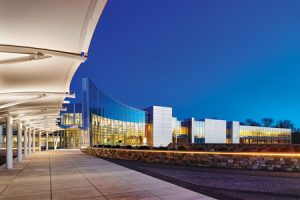
Construction professionals seem to find ways to add more layers and new materials to building envelopes. While these additional layers have helped reduce energy losses, they have not managed to keep water out of the walls. For example, the use of continuous insulation (ci) on exterior walls and the airtightening of building envelopes have only increased the need for materials with elevated drying potential (e.g. fiberglass insulation) because when (not if) moisture infiltrates the assemblies, it needs to escape. This is where resilient design comes into play.
Buildings must be durable and treated individually based on their climate zone (CZ), region, and the location—they must be robust. However, to do so, architects and specifiers must first understand how systems behave in different markets and how designs can be optimized to make the wall assemblies truly robust. Managing moisture would be the key to successfully constructing the sustainable buildings of the future.
In several building science circles, the concept of a ‘perfect wall’ is often discussed. It has a lot of sound principles, such as ‘keeping the outside out and the inside in’ and designing the wall assembly to not just manage, but also control rain, air, vapor, and heat. However, even walls deemed ‘ultimate’ or ‘perfect’ fail due to the multitude of unforeseen events, such as faulty installations and poorly communicated design details. Due to this uncertainty, the ultimate perfect wall is only flawless until it fails. What will happen then? Can the wall withstand failure?
A robust wall is able to anticipate the areas where a wall system or component may not succeed. It includes layers that are designed to reduce the impact of failure. Alternatively, a robust wall could be considered the perfect failure, as it is designed to fail. It embraces the fact that building professionals cannot always predict complete success. However, the building team can anticipate at-risk areas and potential failures. By minimizing risks and anticipating the perfect failure, construction professionals can create truly robust building assemblies.
Background
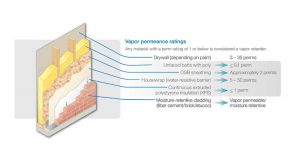
Let us take a step back and first understand the evolution of building construction. How has the industry shifted in the robustness of today’s building assemblies? How have building methods changed, and how are they impacting things like insulation?
The evolution of framing techniques has largely been driven by the need to build more efficiently. Platform framing became the norm as it was much more efficient to construct than balloon framing. Traditional roof rafters have been shifted to roof trusses as they can be built on the roof, ground, or even prefabricated offsite—making room for more options and versatility as well as expediting the construction. Even framing is changing with high-performing, lightweight joists and open-web trusses. Industry professionals are also seeing more and more elements being borrowed from prefabricated construction, which, on its own, is rapidly growing and changing how buildings are put together.
All of these changes come at a cost, especially as the industry is heading toward higher R-values and airtightness levels. There are even more challenging details to address and increasing opportunities for air to leak through the walls. Having said that, the primary goal still resonates within these structures—building professionals do want to develop healthy, durable, and energy-efficient structures. To do this, the project team must understand how the building works and where to look for key problems.
It is important to keep in mind contractors are no longer just responsible for one role or function—even trades are evolving. For example, the insulation contractor is now required to be an energy expert for the entire building envelope, the most important piece of the entire building. The contractor must be equipped with the tools and knowledge to decrease air infiltration and increase building comfort. He/she must understand where to air seal, how to inspect work for quality, and potential problem areas and how to prevent them from happening.
Builders are balancing and juggling multiple management strategies to address the needs—especially the management of heat, air, and moisture—of their projects. No single product or system can be used to address all of these. At a practical level, building project teams strive to achieve a balance between costs and performance, and sometimes one is compromised for the other. Trade-offs are made to reduce project costs. This can, in turn, negatively impact the building’s ability to control the flow of heat, air, and moisture through the building envelope.
Enter the HAM principle—heat, air, and moisture flows must be balanced to ensure optimum performance for any building.