What makes it ‘smart’?
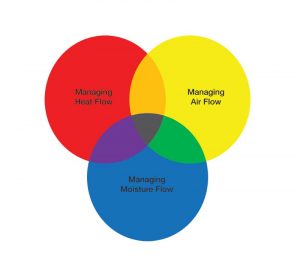
A smart vapor retarder has the ability to react to changes in relative humidity (RH) by altering its physical structure. During winter, when RH is low, smart vapor retarders have the ability to provide resistance to vapor penetration from the interior. However, when RH rises to 60 percent or above, its permeance also increases, thus allowing the water vapor to pass through, facilitating the drying of wet building systems.
When it comes to air infiltration and exfiltration, “air out always equals air in,” so if air can be either stopped from coming in and/or going out, the building team can be fairly confident in the success of the system as a whole. One key advantage of also including an interior air barrier system is they are far better protected from hazards (e.g. rips, tears, getting blown-off, ultraviolet [UV] degradations, etc.) that could diminish performance. Another detail to consider is climate, as it also dictates the amount of airtightness a building would need. For example, a home in the northern half of the United States will generally need an ach 50 of three or less; whereas, the same home in the South would require an ach 50 of five or less. This
is because buildings in the northern climates are susceptible to losing more energy due to the larger temperature differentials between the inside and the outside, especially in the winter months, so losing less air from the building allows it to more easily maintain internal air temperatures, thereby saving energy.
Another interesting nuance is exterior systems involve exterior trades (framers, siders, etc.) and interior strategies that generally involve insulators, drywallers, and other interior tradespersons. This raises the question of who is responsible for the occupants’ comfort, indoor air quality (IAQ), and energy efficiency? Regardless of whether the responsibility lies on the inside, outside, or both, the project team must make sure that the above-mentioned strategies are utilized. Otherwise, hot air would be let out instead of keeping it under control.
Moisture flow
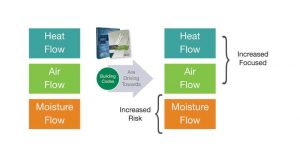
How are building professionals trying to manage moisture? Similar to heat and airflow, the goal is to always keep what is in inside and what is out outside. Of course, all of this changes once moisture gets inside the wall. The focus then is to provide the moisture with a pathway to escape the assembly and ‘breathe,’ so it can dry out.
Every component of the building assembly has a different vapor permeance and falls into one of the following four categories:
- vapor barrier – includes polyethylene (PE) sheet, unperforated aluminum foil, etc., and is between 0.01 and 0.1 perms (per the International Building Code [IBC], this is a Class I vapor retarder);
- vapor retarder – includes kraft-faced fiberglass batts and is greater than 0.1 but less than or equal to 1 perm (according to IBC, this is a Class II vapor retarder);
- semipermeable – includes latex or enamel paint and is greater than 1 perm but less than or equal to 10 (Class III vapor retarder, Per IBC); and
- permeable – includes housewraps, building papers, etc. and is greater than 10 perms.
Quite often, construction practitioners focus on the permeance of just a few materials, but it is critical to take a much more holistic approach and understand how the entire assembly behaves from a moisture management standpoint. It should inspire building professionals to consider solutions that are robust in managing moisture. For example, smart vapor retarders are able to adapt their permeability based on the moisture trapped within a wall cavity—providing it has the means to dry out and minimize risks.
Good design and practice involve controlling the wetting of building assemblies from both the exterior and interior, and each climate zone requires a different approach.