Back to robustness
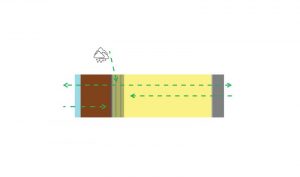
Heat and air flows are relatively static in how they are managed. For example, a hole can be sealed (hopefully during the construction phase itself) and additional insulation can be installed either in the wall’s interior or exterior. However, moisture is a bit different. No wall or roof is completely impermeable to moisture. A robust wall is one with the ability to actively and passively manage moisture while accounting for the fact moisture management changes with the time of day, season, and life of a building.
Additionally, building solutions need to evolve with codes that are driving the increased levels of insulation and airtightness. In the past, R-15 or even R-13 were considered acceptable thermal insulation targets for exterior walls, but today’s walls mostly require either increasing the wall thickness toward the inside (e.g. 2×6) to achieve R-20 and more, which is a code-driven requirement, or adding exterior insulation to the outside of the wall (up to R-10). Airtightness requirements are also more stringent than before. This is great from an energy efficiency perspective, but it increases the risk of moisture condensation in a wall with less drying potential. Surprisingly, there has been limited change in the building and energy codes (e.g. the International Codes [I-codes]) to account for these moisture-management challenges. It should be clarified this does not mean there are no areas where moisture management strategies are suggested (or implied) in some building codes. The issue is there are not enough deliberate references to construction practices to prevent moisture issues from occurring altogether. For example, Section 1404.3, “Vapor retarders,” in the 2018 International Building Code (IBC) suggests “approved designs for accepted engineering practices for Hygrothermal analysis” could be utilized. However, this “code speak” is vague and does not clearly identify acceptable assemblies that would enhance a building’s performance directly. The author anticipates focus will tilt toward areas like durability and resiliency during the next few code cycles as moisture-related problems arise and ideally there will be a shift in a direction that will provide content in an easy-to-understand format for all parties involved.
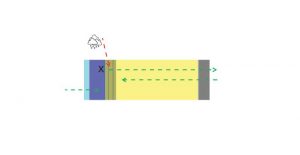
The challenge with moisture management led insulation product manufacturers to develop criteria to evaluate the durability and resiliency of a wall and to assess the robustness of an assembly. To be robust to moisture, the wall assembly needed to perform without moisture issues all year long. Based on research and analysis from dedicated building scientists throughout North America, the team was able to conduct a moisture analysis across various regions built on the following three fundamental performance benchmarks:
- Criterion 1: Assembly should avoid winter moisture condensation risk in the interior gypsum;
- Criterion 2: Assembly should avoid summer moisture condensation risk in the oriented strand board (OSB); and
- Criterion 3: Assembly should avoid water accumulation in case of rain penetration (This initial analysis was done on a single type of exterior wall construction with plans to expand the study to other construction types. Key findings from that preliminary analysis have been presented in this article. It is recommended to consult a professional building science consultant for questions related to any construction type.).
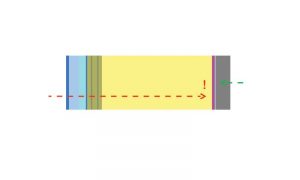
Here is what the team discovered when looking at various regions throughout the United States.
Marine (CZ 3C and 4C) – San Francisco and Seattle, and cold humid (CZ 5A and 6A) – Boston and Minneapolis
- Kraft batts
- Pass Criterion 1.
- Criterion 2: Moderate risk of summer condensation.
- Polyethylene (PE) Pass
- Criterion 1.
- Did not pass Criterion 2: High risk of summer condensation.
- Smart vapor retarders
- Pass both Criteria 1 and 2.
- Closed-cell SPF
- Pass both Criteria 1 and 2.
- 25-mm (1-in.) XPS (R-5) exterior insulation with R-13 fiberglass
- Pass both Criteria 1 and 2.
- Criterion 3: If rain infiltrates the assembly it can dry only toward the interior.
- Note: Risk increased in markets like Seattle and Boston where rain is frequent.
- 38-mm (1.5-in.) mineral fiber (R-5) exterior insulation with R-13 fiberglass
- Passes Criteria 1, 2, and 3.
- Criterion 3: If rain infiltrates the assembly it can dry toward the interior and the exterior.
Hot humid (CZ 2A and 3A) – Houston, Tampa, Atlanta, Oklahoma City, and warm humid (CZ 4A) – Nashville and Philadelphia
- Unfaced batts
- Pass Criterion 1 except in cities with cold winters (e.g. Houston and Philadelphia).
- Pass Criterion 2.
- Kraft batts
- Pass Criterion 1.
- Did not pass Criterion 2: High risk of summer condensation in fiberglass behind the kraft (vapor-closed); moderate in Philadelphia.
- Smart vapor retarders
- Pass both Criteria 1 and 2.
- Closed-cell SPF and open-celled SPF (ocSPF)
- Pass both Criteria 1 and 2.
- 25-mm (1-in.) XPS (R-5) exterior insulation with R-13 fiberglass
- Pass both Criteria 1 and 2.
- Criterion 3: If rain infiltrates the assembly it can dry only toward the interior.
- 38-mm (1.5-in.) mineral fiber (R-5) exterior insulation with R-13 fiberglass
- Passes Criteria 1, 2, and 3.
- Criterion 3: If rain infiltrates the assembly it can dry toward the interior and the exterior.