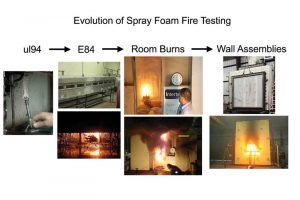
This technology is now presenting itself in the market. By taking a continuous sprayfoam and incorporating innovative, fire-addressing thermal barrier protective technologies within the foam, one can attain all the benefits of c.i., air barrier, moisture barrier, mold defense, structural rigidity, and high insulation value in their structures.
Reducing risk window
How does this benefit the owner, the general contractor, the architect, insurers, and/or the spray application company? Sprayfoams react in the field through a two-component chemical reaction. The NFPA-275 fire barrier rating of the new foam becomes an effective fire barrier as soon as the chemical reaction finishes. Fire safety is “built-in” as soon as the reaction is complete. This is what is known as a “zero risk window” product and is very different from what happens currently when flammable plastic insulation materials, both panels and continuous, must wait for a thermal barrier to be applied.
Often, the company providing the thermal/fire barrier is not the same company applying the insulation. This presents the issue of who owns the liability during that in-between, safety risk window period. Also pertinent is who ensures the proper application methods of the post-added thermal barrier and which code requirements are being met. This risk affects everyone in the construction phase, from the architect to the contractor, sprayfoam applicator, insurance company, and owner/end-user. The risk, added materials, labor, governance, and complexity are eliminated with NFPA-275 SPFs.
Another radically new and often overlooked paradigm credited to monolithic NFPA-275 SPFs is the ability to increase the fire resistance of a building wall or ceiling system. Historically, this has been reserved for non-combustible building elements such as brick, stucco, and concrete. With the achievement of method four (Figure 6), NFPA-275 SPF reduces the transmission of temperature through wall and ceiling assemblies. It passes the ASTM E119 temperature transmission tests described earlier (Figure 7), the method used to define wall ratings (i.e. when an inspector says a one-hour wall is needed between a garage and a house).6 As the thickness of the monolithic fire barrier SPF increases, so does its ability to delay the transmission of heat and poisonous fumes, increasing the overall wall system’s hour rating.
This extends the thermal barrier SPF into the realm of fireproofing; something foam could never be used for in the past. That benefit has historically been reserved for gypsum, concrete, cementitious, brick, and stone. This new technology opens many new and creative avenues previously unattainable with foam insulation in concert with the non-combustible materials described above.