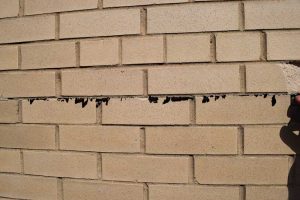
Flashings are a critical component in exterior wall (as well as roof) construction and are used at base of wall details, shelf angles, window lintels, and other locations to divert water that enters the enclosure system to the exterior. Since the 1980s, membrane flashing materials using rubberized asphalt have gained in popularity due to their flexibility, ability to adhere to a variety of substrates, and resistance to moisture. While these flashing materials can provide durable and effective moisture management, careful detailing is needed to ensure proper performance and avoid premature degradation.
In two recent case studies, staining on exterior masonry was found to be related to flashings installed in the 1990s. In the first example, rehabilitation of a historic structure involved reconstruction of brick masonry at relieving angles and installation of new rubberized asphalt flashings to protect the original or replaced steel angles. To avoid introducing a visible flashing line, detailing did not include a drip edge, and the flashing was cut flush with the face of the brick masonry. Over time, repeated solar heating of the wall on the west-facing façade caused the exposed membrane to soften and flow down the wall, depositing asphaltic material on the face of the brick (top right photo). (Also note the brick was inappropriately installed tight to the underside of the angles, leading to cracking and spalling of the brick that was the initial concern of the owner.)
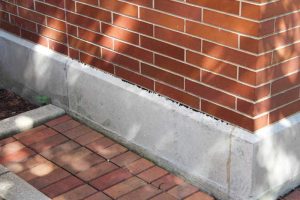
In the second example, a building constructed in 1994 included rubberized asphalt flashing at all shelf angles and window lintels. The flashing at upper levels terminates at a stainless-steel drip edge and has generally performed well. However, at the base of the wall, the flashing is positioned above a cast stone watertable and is terminated flush with the brick masonry above. Over time, the membrane has softened, and asphalt has flowed onto the cast stone surfaces (bottom right photo).
In these two cases, the softening and migration of the rubberized asphalt is primarily an aesthetic issue. However, softening and migration of asphalt also has the potential to obstruct weep holes or drainage pathways.
To avoid staining and potential flashing performance issues, rubberized asphalt flashings should typically be held back 13 to 25 mm (0.5 to 1 in.) from the exposed face of the masonry, with a metal drip edge or pan flashing to which the rubberized flashing can be bonded. While rubberized asphalt flashings can be effective in many locations, a different flashing material (such as uncured ethylene propylene diene monomer [EPDM]) should be considered for details such as base of wall flashing, where the flashing is bonded directly to the masonry without a drip edge. In this case, a high-temperature-tolerant sheet flashing can be installed to extend beyond the face of the wall and then trimmed flush with the face of the completed masonry.
The opinions expressed in Failures are based on the authors’ experiences and do not necessarily reflect that of The Construction Specifier
or CSI.
Kenneth Itle, AIA, is an architect and associate principal with Wiss, Janney, Elstner Associates (WJE) in Northbrook, Illinois, specializing in historic preservation. He can be reached at kitle@wje.com.
Deborah Slaton is an architectural conservator and principal with WJE’s Northbrook office, specializing in historic preservation and materials conservation. She can be reached at dslaton@wje.com.