FAILURES
Aluminum accounts for the greatest share of the U.S. commercial market for windows, doors, and skylights. Its manufacturing versatility, structural longevity, performance dependability, and near-infinite recyclability contribute to its popularity. While aluminum also offers high corrosion resistance, certain conditions require caution to avoid potentially costly failures.
In architectural building products, the aluminum used is always an alloy. By adding other metals—such as magnesium and silicon—in small amounts, the alloy yields better corrosion resistance.
Aluminum’s inherent corrosion resistance is due, in large part, to its naturally-occurring oxide film, which acts as a protective barrier between the metal and the environment.
Minimizing handling and moisture is key to preserving this performance. Unfinished aluminum should be stored in a dry, controlled environment and never be handled with bare hands. Moisture between the aluminum pieces and oils on the skin can cause permanent and even severe corrosion.
Galvanic corrosion causes deterioration of aluminum. This process occurs when dissimilar metals are in contact and in the presence of an electrolyte such as salt water. More anodic metal will corrode as a result of electrochemical action in the presence of moisture.
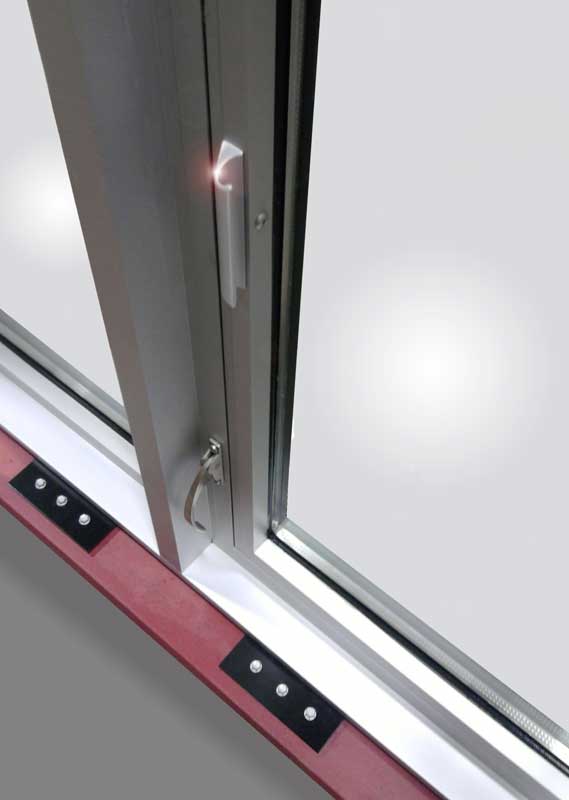
Photo courtesy Wausau Window and Wall Systems
To reduce the opportunity for galvanic action, it is necessary to increase the electrical resistance between the two metals—in other words, to turn off the switch. Separation of the dissimilar metals can be done by means of thick elastomeric tapes, non-absorptive plastic, or sealant materials. Alternatively, one of the metals, preferably the more cathodic, may be painted or coated.
For aluminum, a single coat of chrome phosphate pretreatment followed by primer and high-performance paint may effectively prevent galvanic corrosion. Alternatively, a single field-applied coat of heavy-bodied bituminous paint can be employed. Anodic coatings alone are usually insufficient for galvanic separation.
The relative areas of the dissimilar metals involved are extremely important to the potential for galvanic corrosion. The use of stainless steel (cathodic) screws or rivets in aluminum (anodic) window framing members is satisfactory. No harmful corrosion is likely to result because the area of stainless steel is small in relation to the aluminum.
The use of a copper roof or fascia located above unprotected aluminum can cause copper salts (cathodic ions) to be deposited on the aluminum by draining rainwater. Since the area of copper is larger than the aluminum’s, there is greater cause for concern and prevention of harmful corrosion.
When carbon steel is employed as reinforcing material or steel anchors in conjunction with aluminum-framed window systems, separation is required to prevent galvanic corrosion. This can be accomplished by using zinc or other coatings.
The opinions expressed in Failures are based on the authors’ experiences and do not necessarily reflect those of The Construction Specifier or CSI.
Steve Fronek, PE, leads Wausau Window and Wall Systems’ new product development, marketing, technical support, and general research. He is the past-president of the American Architectural Manufacturers Association (AAMA), and has served on 16 of AAMA’s committees and task groups, including the Aluminum Material Council. Fronek can be contacted vie email at sfronek@wasauwindow.com.
Many thanks for such an informative and detailed explanation for reasons of applying isolation coat on aluminum