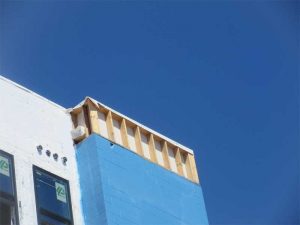
A primary design goal for any building enclosure should be to minimize the infiltration of bulk water into the intended dry zone of the various enclosure assemblies for the duration of their anticipated service life. Significant and/or recurring water infiltration can adversely affect moisture-sensitive materials and the overall performance of the enclosure. However, an often-overlooked aspect of achieving this goal is the control and management of bulk water during the project’s construction phase.
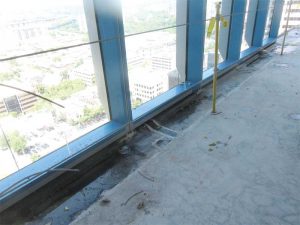
Some trades, such as roofing, acknowledged and emphasized the importance of maintaining watertight conditions for partially completed work. For example, it is common for specifications to limit the installation of roof assemblies to areas that can be made “weather-tight” by the end of each day’s work by installing temporary terminations to prevent bulk water from entering the completed portion of the assembly. These temporary “tie-ins” are then removed once work resumes. This process is repeated throughout the installation of the roof assembly until it is complete.
However, while maintaining watertight conditions during installation of roof assemblies is well understood, similar protections for vertical enclosure assemblies are often overlooked during design, or not considered during construction. Upon identifying the need for such protection, absent clear language in the specifications, confusion often ensues as to which trade
is responsible for implementing protective measures and who is responsible for the cost associated with such protection. Infiltration of bulk water into completed portions of the vertical enclosure, due to the lack of temporary weather protection provisions, can result in a number of potential performance issues, including premature degradation of moisture-sensitive materials, increased potential for organic growth, decreased thermal resistance, and a greater potential for elevated moisture levels within the interior environment following construction due to the “built-in” moisture within the enclosure assemblies.
The American Society of Heating, Refrigerating and Air-Conditioning Engineers (ASHRAE) also acknowledges the importance of controlling moisture within buildings during construction in their Fundamentals Handbook, citing that built-in construction related moisture (in part due to weather conditions during construction, the installation sequence/schedule of the work, and the effectiveness of temporary protection of incomplete areas of construction), can be a significant source of moisture for the first years of a building’s use after construction.
To reduce the potential for moisture-related issues resulting from exposure of completed work to the elements during construction, the requirements and responsibilities for temporary weather protection of completed work should be clearly specified, and in some cases where complex geometries or tie-ins exist, detailed in the construction drawings.
In addition, the sequencing of the work and protocols for establishing appropriate temporary protection around in-progress and complete work should be reviewed during each trade’s pre-construction meeting as part of the quality control (QC) requirements for the project.
The in-progress construction should be continually monitored and evaluated by the project team to better ensure the established protocols for protecting the completed work from water intrusion are being implemented as intended and effectively maintained.
Jeffrey Sutterlin, PE, is an architectural engineer and associate principal with Wiss, Janney, Elstner Associates’ (WJE’s) Princeton, New Jersey, office. He specializes in investigation and repair of the building enclosure. He can be reached at jsutterlin@wje.com
David S. Patterson, AIA, is an architect and senior principal with WJE’s office in Princeton, New Jersey. He specializes in investigation and repair of the building enclosure. He can be reached at dpatterson@wje.com.
The opinions expressed in Failures are based on the authors’ experiences and do not necessarily reflect that of The Construction Specifier
or CSI.