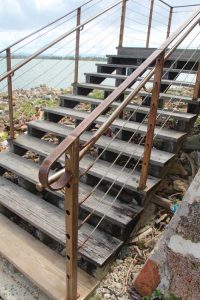
Stainless steel is commonly used to provide architectural metal fabrications that are corrosion resistant without the need for paint or other coatings. It is common misunderstanding that stainless steels (SS) will not corrode or stain, though they typically will perform much better than uncoated mild steel. The term “stainless steel” encompasses a variety of different metallic alloys; therefore, it is important to understand the needs of the application. A particular stainless-steel alloy that works well for general architectural purposes may not hold up in a severe environment.
When specifying a stainless steel, it is important to determine the environmental exposure conditions as well as the aesthetic requirements. For instance, what degree of staining or discoloration is acceptable. Other factors to be considered in addition to metal type and environment—are surface finish (smoother surfaces generally resist corrosion better), orientation (vertical or horizontal), and the likelihood of rinsing from rain or scheduled maintenance. Guides for selecting a stainless steel alloy are available from the International Molybdenum Association (IMOA).
The basic definition of stainless steel is a metal that contains more than 12 percent chromium. Some of the most common stainless steels, termed “austenitic,” are generally identified by being nonmagnetic, though some slight magnetic behavior can exist, especially if parts are formed or welded. Austenitic stainless steels are often used for architectural metalwork, with Type 304 being the most common and Type 316 recommended for more severe environments. The primary difference between 304 and 316 SS is the addition of molybdenum to 316 SS. This addition improves the chloride pitting resistance of 316, making it more appropriate for applications in salt or sea air environments. Both 304 and 316 SS are readily available in the “L” grade indicating low carbon, which helps maintain the corrosion resistance of the alloy, if welded.
Some stainless steels, termed “ferritic” or “martensitic,” are used because they generally have higher strength or other desirable mechanical properties (ductility and strength) as compared to the austenitic SS. These grades are typically identified by having magnetic properties. It is important to note, when properly specified, they can also provide good corrosion performance and are not inherently inferior to the austenitic grades. Often, stainless-steel screws and fasteners are martensitic stainless steel, such as Type 410, offering higher hardness and strength along with good corrosion-resistance.
In a recent project, the condition of an exterior Type 304 stainless-steel stair assembly was reviewed. This stairway is located in a tropical environment directly adjacent to an ocean inlet, where it is regularly subjected to salt spray from the action of waves. Although the stair is only about 10 years old, widespread surface corrosion has developed on most surfaces. The current degree of corrosion, while unsightly, does not yet approach the level of structurally significant distress; however, pitting and more advanced corrosion has begun to occur in localized areas. The use of a stainless-steel alloy such as Type 316 with improved pitting resistance would probably have provided better performance for this severe exposure. Although pickling and passivation cleaning processes to remove the corrosion buildup and staining are now recommended to extend the service life of the assembly, localized areas of pitting may not be repairable. Going forward, regular cleaning with a chloride-neutralizing detergent can help protect this assembly. A clear coating, sealer, or wax may also provide added protection to the metal.
The opinions expressed in Failures are based on the authors’ experiences and do not necessarily reflect that of The Construction Specifier or CSI.
Authors
Kenneth Itle, AIA, is an architect and associate principal with Wiss, Janney, Elstner Associates (WJE) in Northbrook, Illinois, specializing in historic preservation. He can be reached at kitle@wje.com.
Bernard Schulze is a metallurgical engineer and principal with Wiss, Janney, Elstner Associates (WJE) in Northbrook, Illinois, specializing in failure analysis and corrosion of metals in a broad range of applications.