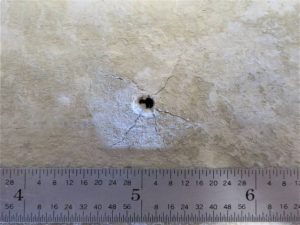
• When comparing the effect of spalling (case 1 to case 3.a), the percent reductions in pull-through resistance were approximately 45, 36, and 25 percent for Products A, B, and C, respectively;
• When comparing the effect of nail head condition (case 3.a versus case 3.c), the percent reductions in pull-through resistance were approximately 85, 63, and 63 percent for Products A, B, and C, respectively; and
• When comparing the best-case scenario (case 1) to the worst-case scenario (case 3.c), the percent reductions in pull-through resistance were approximately 92, 77, and 72 percent for Products A, B, and C, respectively. For each product tested, the pull-through resistance was reduced by at least 725 N (163 lbf) when comparing these two scenarios.
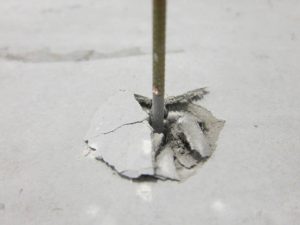
Overall, the test data indicates inboard face spalling results in significantly reduced pull-through resistance. Furthermore, when considering the effect of nail head condition, the pull-through resistance is further reduced upon nail head penetration of the outermost material layer (i.e. from the proud to flush condition) and reduced further yet as the nail head penetration depth with respect to the panel face increases (i.e. from the flush to recessed condition). Both the face spalling and nail head condition parameters contribute to variations in pull-through resistance and should be carefully considered during design, specification writing, and installation.
Conclusion and recomendations
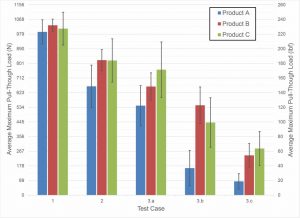
Fiber-cement-based products used in construction are not uncommon in the industry; however, limited information is available regarding their material behavior. Specifically, as a cladding material, specifiers and installers should be aware of the apparent sensitivity to variations in the substrate configuration and nail head installations, and understand the consequences of not installing in accordance with the manufacturer’s written instructions. Based on the independent laboratory results presented, the following concluding remarks are presented:
• Even subtle differences in the position of nail heads relative to the cladding panel surface can have substantial consequences on the cladding material’s capacity to resist applied loads. This is particularly important if pull-through resistance is already reduced due to unconstrained spalling on the inboard face of the fiber-cement panel, as is the case for wall assemblies that include cap nails which create a gap between the exterior sheathing and the panel;
• Construction specifiers should consider the sensitivity of pull-through resistance to the nail head condition and substrate configuration. As such, it may be prudent to specify a thicker panel and/or additional nails, based on the design criteria, to account for potential reductions to the rated load resistance due to installation errors (e.g. overdriven fasteners). This would be particularly important for projects with high design wind loads;
• When installing fiber-cement-based products with nails, builders should periodically calibrate their pneumatic nailers on a representative mock-up to avoid flush and recessed head conditions. Requirements for periodic calibrations should be clearly identified in the project specifications; and
• Field quality control measures should be implemented on all construction projects using fiber-cement-based materials. Such measures should be clearly identified in the project specifications and may include the construction of mock-ups for training the installers in accordance with the manufacturer’s written instructions and periodic inspections of installed nail head conditions.
Understanding the material behavior of fiber-cement-based products and the implementation of practices that reflect this understanding is critical to successful installations.
Author
Jacob W. Arnold is the manager of testing services at Raths, Raths & Johnson, Inc. (RRJ), a nationally recognized engineering, architecture, and forensics consulting firm. His experience includes laboratory testing of building materials, in situ field quality control testing, and implementation of monitoring programs to investigate the effects of environmental conditions and the performance of building components. Arnold can be reached at jwarnold@rrj.com.
Colin P. Rueb is a structural engineer at RRJ and is experienced in structural investigations and material analyses of various building materials, with emphasis on concrete construction. His background includes condition surveys, field and laboratory testing, structural analysis, and finite element modeling of distressed facade systems, building components, and various structures. Rueb can be reached at cprueb@rrj.com.
Kurt Hoigard is the President of RRJ and responsible for the leadership and oversight of the firm’s consulting and testing services. He has specialized in the investigation and repair of distressed and deteriorated structures and the performance of building materials and systems, and consults in the areas of structural analysis, complete collapse, design peer review, water leakage investigation, and expert witness testimony. Hoigard can be reached at krhoigard@rrj.com.