Oh, hail!
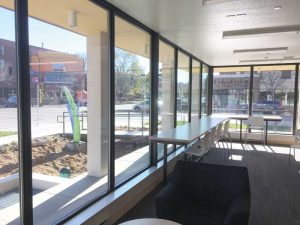
Vinyl and wood/plastic composite windows can struggle to withstand hits from large hail (ASTM D256 Standard Test Method for Determining Impact Resistance of Plastics). These window materials are difficult to repair and usually must be replaced because of potential water and air infiltration. In some cases, the sash may be replaced if only it is damaged, but the main frame survived unscathed.
Fiberglass has a high impact threshold and resists damage from a direct hit, but if damaged, can be repaired so replacement is not necessary. Fiberglass does not get more brittle in colder temperatures because of the pultrusion process. In fact, fiberglass changes little from -1.1 to 65.5 C (30 to 150 F) (ASTM E831, Coefficient of Linear Thermal Expansion).
Cost considerations for fiberglass and vinyl
There are lower cost vinyl windows in the market serving the purpose of filling an opening and providing views, daylight, and ventilation. However, lower cost vinyl windows lack the ultraviolet (UV) protection, structural integrity, and durability, which higher quality windows offer.
Lower cost vinyl windows used in multifamily projects will need to be replaced sooner than fiberglass windows. In the author’s experience, these lower cost windows have had to be replaced in as little as 10 years with most needing to be replaced within 15 years. These replacement costs are much higher than the initial cost of material, labor, and installation. Fiberglass is optimized for low-maintenance and longevity, making it a perfect fit for owners holding properties and looking to maximize their long-term return on investment (ROI).
Fiberglass versus aluminum
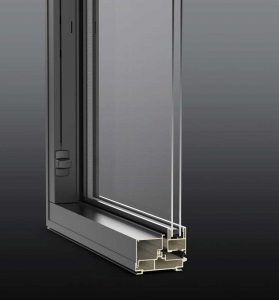
Aluminum windows gained popularity after World War II and rivaled wood windows by the 1970s. While maintaining popularity, aluminum windows are notorious for their lack of energy efficiency. Despite advances in spacer and thermal break technology, it takes triple-pane aluminum windows to match dual-pane fiberglass windows for U-factors and solar heat gain coefficient (SHGC) values. There is also a substantial difference in condensation resistance (see Figures 2 and 3).
Expansion and contraction
As far as how fiberglass compares to aluminum, the former has less than a third of the thermal expansion of aluminum and less than 0.02 percent of the thermal conductivity of aluminum. Aluminum has one of the highest thermal expansion coefficients of any metal type (ASTM E831-19, Standard Test Method for Linear Thermal Expansion of Solid Materials by Thermomechanical Analysis). Over time, this can lead to increased maintenance, cause stress to sealants and fasteners, and may lead to faster air and water infiltration.
WE used the fiberglass replacenment windows for their natural wood look and feel and fire resistance and strength on the El Cordova Hotel 1928, in Coronado, CA. many years back and as far as I know all is still going well there. Stuart Resor Architect