Painted coating performance
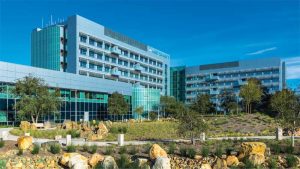
Photo courtesy Quality Metalcrafts, LLC and Linetec
Retaining the color and resisting degradation from ultraviolet (UV) radiation are notable performance strengths of high-performance architectural painted coatings on aluminum wall cladding systems. Paint also protects and maintains the structural integrity of the aluminum and withstands salt-spray.
To ensure optimal performance of coated aluminum, reputable finishing service providers, and product manufacturers follow the American Architectural Manufacturers Association (AAMA) voluntary specifications. The specification series, most recently updated in 2017, is known by its document numbers:
- AAMA 2603, Voluntary Specification, Performance Requirements and Test Procedures for Pigmented Organic Coatings on Aluminum Extrusions and Panels (with Coil Coating Appendix);
- AAMA 2604, Voluntary Specification, Performance Requirements and Test Procedures for High Performance Organic Coatings on Aluminum Extrusions and Panels (with Coil Coating Appendix); and
- AAMA 2605, Voluntary Specification, Performance Requirements and Test Procedures for Superior Performing Organic Coatings on Aluminum Extrusions and Panels (with Coil Coating Appendix).
AAMA 2603: Typical for interior specifications
Required to show only ‘slight’ fade and chalking after one year, AAMA 2603 has no specifications for gloss retention and erosion resistance. Baked enamel (acrylic/polyester) paints should meet AAMA 2603. These painted finishes are less expensive than PVDF resin-based coatings, but have poor resistance to color fading and chalking. Baked enamel coatings are harder than PVDF and can be used for interior applications where color retention is not required.
AAMA 2604: An ‘intermediate’ specification
AAMA 2604 specifications are more demanding than AAMA 2603. For a finish to qualify, five years after its application the color must have faded no more than five delta E (Hunter), the chalking will be no higher than eight, the finish still retain 30 percent of its gloss and no more than 10 percent of it has eroded (Chalking is measured in accordance with the procedures explained in ASTM D4214, Standard Test Methods for Evaluating the Degree of Chalking of Exterior Paint Films). This finish will provide good color and gloss retention. It also will offer good hardness and abrasion resistance. Painted finishes meeting this specification typically are 50 percent PVDF resin-based coatings and are commonly applied on aluminum storefront framing, entrances, or other high-traffic areas.
AAMA 2605: The specification for high-performance building exteriors
The highest-performing organic paint coatings meet AAMA 2605, Voluntary Specification, Performance Requirements, and Test Procedures for Superior-performing Organic Coatings on Aluminum Extrusions and Panels. Ten years after it has been applied, an AAMA 2605 paint will have faded no more than five delta E, the chalking will be no higher than eight, at least 50 percent of its gloss will still be retained and only 10 percent of the film will have eroded. These finishes exhibit outstanding resistance to humidity, color change, chalk, gloss loss, and chemicals. Painted finishes meeting this specification typically are 70 percent PVDF resin-based coatings.
Regardless of specification, all coatings should be visibly free from flow lines, streaks, blisters, or other surface imperfections in the dry-film state on exposed surfaces when observed at a distance of 3 m (10 ft) from the metal surface and inspected at an angle of 90 degrees to the surface.
Painted finishes for aluminum wall cladding installed on building exteriors are typically specified to meet AAMA 2605. For interior wall cladding applications, AAMA 2604 or 2603 may provide an acceptable performance specification.
Decreasing the number of touchpoints often increases the clarity of communication and the opportunity for success. There are a few finishing service providers in the United States that are able to offer a single-source solution for aluminum wall cladding and other architectural products. Beyond offering both painted and anodized finishing services, some of these companies offer value-added services, such as:
|
Anodize process and performance
Unlike architectural coatings, anodizing is an integral part of the aluminum substrate. The anodizing process produces an oxide film that is uniform, hard, and protects the aluminum substrate from deterioration—providing excellent wear and abrasion resistance. Anodized finish is durable and the hardness of the surface is comparable to a sapphire, the second-hardest substance on earth. This characteristic makes anodizing sulfate for aluminum wall cladding systems—both on the exterior, where finishes must withstand continuous exposure to weather and pollution, and on the interior, where finishes must hold up to constant wear and tear by the people within the buildings.
AAMA 611, Voluntary Specification for Anodized Architectural Aluminum, provides the industry standard for Class I anodic finishes. Finishes meeting or exceeding all requirements of this standard are shown to resist the ravages of time, temperature, corrosion, humidity, and warping.
To meet AAMA 611 requirements, Class I anodize must have a minimum dry film thickness (DFT) of 18 μm (0.7 mils) and should also pass the following stringent guidelines.