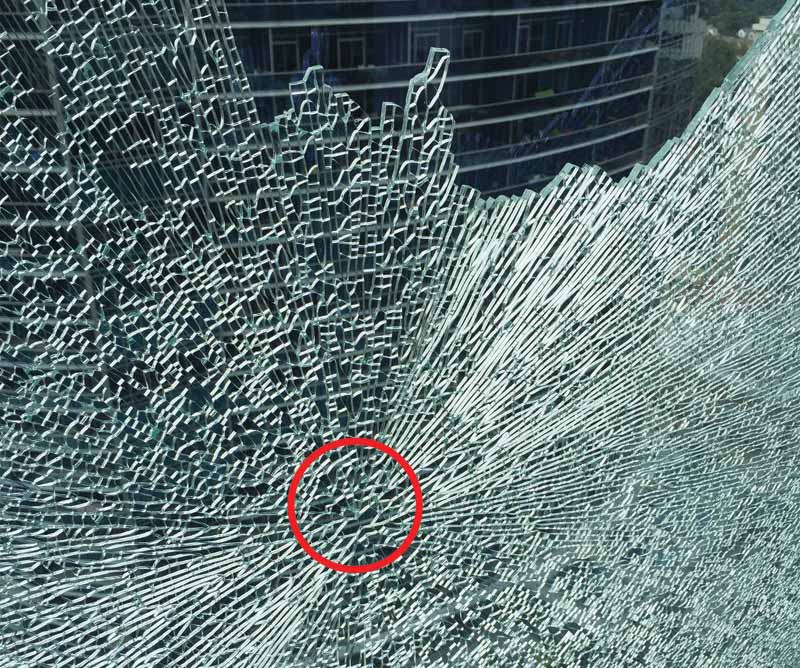
Images courtesy Simpson Gumpertz & Heger
Spontaneous fracture
Spontaneous fracture is a term generally applied to the sudden breakage of fully tempered glass without any apparent external stress.
If fully tempered glass does break spontaneously, the residual tension built into the glass core drives cracks throughout the plate, producing a diced fracture pattern. If the fragments do not leave the opening after breakage, one can see a series of primary cracks radiating from the point of origin, in what is commonly called a “starburst” pattern (Figure 2).
Impurities can be introduced into glass during the melting of the raw ingredients in the furnace at the float plant. Many impurities are benign, but nickel sulfide (NiS) can be problematic.
The sulfur in NiS can be derived from sodium sulfate (Na2SO4), employed as a fining agent in the molten glass mixture. There is debate within the industry as to exactly how nickel is introduced into the mix, but commonly known causes include:
- contamination of raw materials;
- storage/handling equipment of raw materials; and
- inside surfaces of the furnace itself from nickel-bearing metals such as stainless steel.
Most float glass manufacturers are aware of the risks of contamination and include details within their quality assurance/control (QA/QC) procedures for minimizing contamination.
NiS is an unusual compound because it has different high and low-temperature crystalline structures, namely the alpha phase (i.e. high temperature, greater density, smaller volume, and less stable crystalline structure) and beta phase (i.e. low temperature, less dense, larger volume, and more stable crystalline structure). The cumulative effect of heat causes NiS particles to transition from the alpha to the beta phase. During the rapid cooling process of tempering, the NiS particle may be locked into its less-stable alpha phase. (The slow cooling process for annealed glass allows the NiS particle to transform from the alpha phase to the more-stable beta while the material is still soft and has the ability to accommodate the inevitable expansion without adverse consequences.)
If the NiS particle is locked in its alpha phase during the tempering process, it can eventually transition to the beta under the long-term effect of in-service heat from the sun or heating systems of the building. When this occurs in a particle locked in the mid-plane of the glass, its expansion, in conjunction with the residual tensile stress surrounding it, can propagate a micro crack or “vent” in the glass. When the vent reaches a critical length, the residual tensile stress in the glass core causes the crack to propagate throughout the lite and fracture spontaneously.
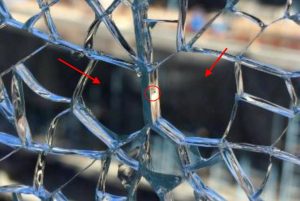
NiS-induced fractures show these characteristics:
- Two distinctive glass fragments at the fracture origin have a unique shape (roughly hexagonal or pentagonal) and are generally larger than the other fragments. This is often referred to as the “cat-eye,” “butterfly,” or “figure eight” pattern (Figure 3).
- The NiS inclusion is visible at the mid-plane of the fractured interface between the two cat-eye fragments (Figure 3). The inclusion, or “stone,” is spherical and approximately 0.1 to 0.2 mm (4 to 8 mils)
in diameter. - No apparent sign of localized crushing of the glass surface at the fracture origin (surface crushing indicates potential impact).
As discussed previously, all float glass (including annealed, heat-strengthened, and fully tempered) may contain NiS impurities. However, NiS-induced fracture occurs only in fully tempered glass. The authors are not aware of any incidents of spontaneous fracture attributed to NiS in annealed or heat-strengthened glass, as long as the heat-strengthened variety has its RCSS within the limits (i.e. 24,132 to 51,711 kPa) set forth in ASTM C1048. One of the reasons for limiting the RCSS of heat-strengthened glass to this range is to provide a moderate level of strength increase over annealed glass, but limit the RCSS safely below the minimum RCSS of 68,948 kPa of fully tempered glass at which NiS-induced fracture is known to occur. The authors have found NiS-induced fractures in glass with RCSS at 56,537 kPa (8200 psi) or above. This level of RCSS provides sufficient residual tensile stress around a NiS particle, located mid-plane, to propagate fracture if and when the impurity undergoes its phase transformation.
Glass is manufactured in large batches. Once there is at least one NiS-induced fracture of fully tempered glass on a building, it is likely there will be others from the same contaminated manufacturing batch. The probability of NiS-induced fracture in a given population of fully tempered glass is unpredictable because of many variables such as:
- the likelihood and quantity of contaminates in the furnace;
- the potential location of inclusion within the tension zone of the glass; and
- the probability of the NiS occurring in the less-stable alpha phase.
Once fracture occurs, the possibility of the glass fragments remaining in place (i.e. retained in the frame) is also unpredictable and dependent on a variety of factors including, but not limited to:
- size and thickness of glass;
- exposure to post-fracture lateral forces such as from air movement (e.g. wind);
- magnitude of energy release during fracture
(a function of magnitude of residual stress built into the glass); - location of NiS inclusion within the glass;
- presence of laminating interlayers; and
- adhesion/stiffness of glass retention by the perimeter frame.
Therefore, unless the fractured lite is laminated to an unbroken lite, there is no definitive set of circumstances under which one can feel confident the fragments will be retained in place after fracture. Additionally, although a laminated sheet of glass retains the fractured lite, the laminated lite will no longer have the same stiffness or resistance to in-service loads.
Industry practice
It has been recognized in the architectural glass industry for decades fully tempered glass can fracture spontaneously due to the presence of NiS impurities. For this reason, it is, and has been, well understood monolithic, fully tempered glass should be avoided in applications where a fracture and glass fall-out pose a substantial risk of harm to people or property. A major glass manufacturer addressed this issue in a technical bulletin, first published in 1988. In this document, the manufacturer confirmed this inherent susceptibility of fully tempered glass to spontaneous breakage in-service, and refused to knowingly supply monolithic, fully tempered glass for “street wall” applications.
In some cases, fully tempered glass is mandated by the building code (e.g. safety glazing and fireman knock-out panels) or required for strength (e.g. to resist high thermal stress or tension due to design loads), as is often the case for point-supported and other similar “structural” glass applications (as a result of high tensile stresses around the anchors and glass fittings). In these cases, where monolithic, fully tempered glass is unavoidable, major glass manufacturers have advised for years the glass should be heat-soak tested as a means to reduce the risk of in-service breakage due to NiS inclusions.
DISPELLING MYTHS ABOUT SPONTANEOUS FRACTURE |
The terms discussed regarding fully tempered glass, spontaneous fracture, and heat-soak testing can be confusing. This has led to misinformation, false claims, and myths as discussed and clarified below.
Myth #1: If glass on a project has a statistical probability of breakage (SPB) of 8/1000, one should expect to have eight broken lites of glass for every 1000 pieces of glass on the building during construction or in-service. Myth #2: Heat-soak testing reduces SPB from 8/1000 to 5/1000. Myth #3: Heat-soak testing eliminates all risks of spontaneous breakage of fully tempered glass in-service. Myth #4: NiS-induced spontaneous fracture of fully tempered glass runs its course in the first three to seven years, after which breaks will eventually stop. |
Having specialised in the spontaneous fragmentation for several decades I find that some of the recommendations by the authors, such as specifying heat strengthened glass which is not prone to breakage due to nickel sulfide to be erroneous and misleading.
I have witnessed several NiS breakages in heat strengthened glass.