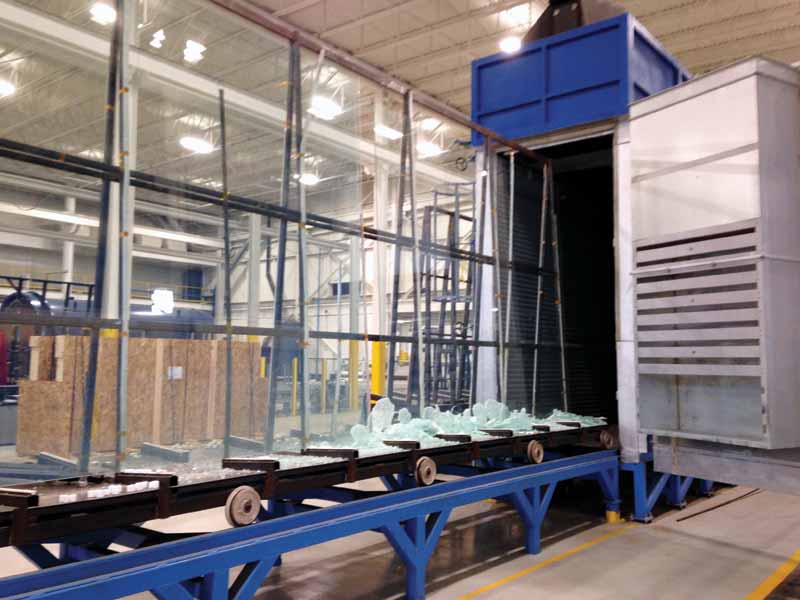
Photo courtesy Agnora.
Heat-soak testing
Heat-soak testing is a process whereby fully tempered glass is put back into a furnace and held there at a specific temperature for a period of time in order to induce any NiS inclusions to undergo their phase transformation, and thus break the glass during the test in the furnace rather than on the building in-service (Figure 4). The most widely used industry standard for heat-soak testing is the European code EN-14179, Glass in Building – Heat Soaked Thermally Toughened Soda Lime Silicate Safety Glass, which includes the following requirements:
- dwell temperature of 290 C (550 F) +/- 10 C (18 F) (i.e. temperature below the annealing point at which the RCSS from tempering could be reduced);
- dwell time of two hours, commencing when all of the glass surfaces have reached the required temperature; and
- separation of glass panes without hindering airflow (e.g. minimum 20-mm [0.8-in.] gap between panes) to ensure even heat distribution around the glass surfaces.
When carried out properly in accordance with EN-14179, heat-soak testing significantly reduces, but does not eliminate, the risk of NiS-induced fracture in-service. The authors’ experience with NiS-induced breakage over the last 40 years shows only one isolated example of NiS-induced fractures in fully tempered glass panels that were allegedly heat-soak tested. While heat-soak testing is effective in reducing the risk of in-service spontaneous breakage due to NiS impurities, it is not a guarantee. Further, heat-soak testing adds another step to the manufacturing process and comes at additional cost and production time. The spontaneous breakage in the furnace can also damage adjacent unaffected glass panels during the test.
Some manufactures provide warranties to replace glass broken in-service due to verifiable NiS inclusions if the glass was heat-soak tested, and the breakage exceeds a certain percentage (e.g. greater than five lites per 1000 or 0.5 percent of the total number of glass panels). In this case, on a building with 400 glass panels, the owner is responsible for paying for the replacement of the first two broken panels, and every other broken panel thereafter would be covered by the manufacturer. These warranties typically include the cost of the replacement glass material and installation labor and are limited to five years from the date of manufacture. These warranties, however, often do not cover mitigation or remediation measures (e.g. adding protective film to unbroken glass panes to help hold fragments in place in case future breakage occurs) or consequential injury/damages to people and property associated with spontaneous glass breakage.
Non-destructive testing
In-place, non-destructive test methods for identification of NiS inclusions in fully tempered glass, which could eventually lead to spontaneous fracture, are generally impractical. Several methods have been tried for locating NiS inclusions on in-service glass (e.g. ultrasound, laser imaging, photographic, and light detection), in the hope of identifying potential inclusions before they break the glass. These methods are labor intensive, time consuming, expensive, require specialized equipment, and highly prone to user error. Even if an inclusion is found near the mid-plane of the glass, the crystalline state of the NiS is still unknown. So, one does not know if the phase transformation has already taken place and whether the inclusion is benign or not.
Post-fracture testing and verification
The classic signs of a NiS-induced break include the distinctive “cat-eye” fragments at the fracture origin and no apparent localized crushing of the outer surface of the glass. Visual inspection can determine if the glass at the fracture origin remains intact in the opening. To determine conclusively the cause of breakage was NiS inclusion, the cat-eye glass fragments should be tested in a laboratory (Figure 5).
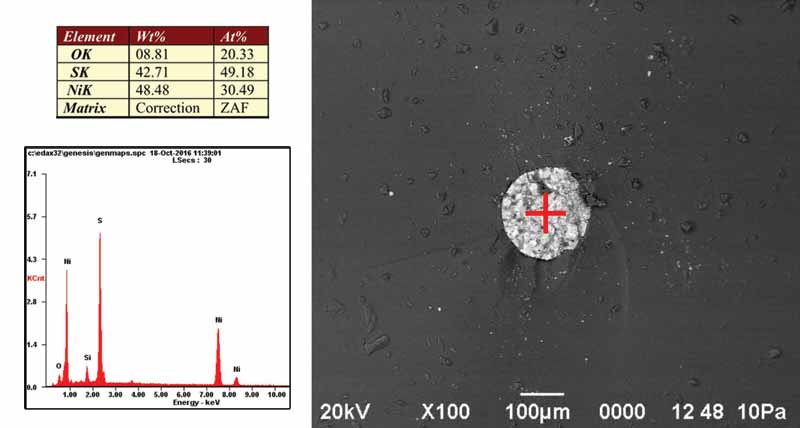
Image courtesy Simpson Gumpertz & Heger
Recommendations
The authors recommend consideration of the following when specifying glass on projects.
Consider using heat-strengthened glass at all exterior applications wherever possible, as it provides greater strength to resist structural loads and thermal stress when compared to annealed glass, without the risk of spontaneous fracture and likelihood of post-fracture glass fall-out associated with fully tempered glass.
It is important to not accept use of fully tempered glass without reviewing structural and thermal stress calculations confirming it is in fact required, as one may be taking on unnecessary risk in employing fully tempered glass when heat-strengthened glass would suffice. Additionally, fully tempered glass is sometimes produced in lieu of heat-strengthened at the convenience of glass manufacturers (and without approval) for economic reasons, and not because of code or strength requirements. (Heat-strengthened glass requires more stringent temperature and control during the quenching process than fully tempered, and therefore, can be more time-consuming and costlier to produce.). In any case, design professionals should not accept fully tempered glass unless its requirement for the project is proven.
One can also consider providing laminated glass to avoid the use of monolithic, fully tempered glass to meet safety glazing code requirements, as well as utilize available code exceptions. Section 2406.4.3, “Glazing in Windows,” of the International Building Code (IBC) 2015, for example, allows for the following exceptions to the safety glazing:
- if a horizontal rail is installed 866 to 965 mm (34 to 38 in.) above the finished floor surface; or
- he outboard lite of an IGU where the bottom exposed edge is greater than 7 m (25 ft) above an exterior walking surface.
If these alternative options are not available for the project, and monolithic, fully tempered glass is unavoidable, the authors recommend the following:
- heat-soak test all monolithic, fully tempered glass in accordance with EN-14179;
- utilize reputable glass manufacturers and fabricators who will address the risks associated with the use of fully tempered glass;
- require QA/QC procedures of glass manufacturers to minimize risks of float glass contamination;
- require factory logs documenting heat-soak testing of all monolithic, fully tempered glass on the project in accordance with EN-14179; and
- seek records of glass manufacturers’ past spontaneous breakage events and how they were resolved.
Conclusion
Although the percentage of buildings experiencing spontaneous breakage of fully tempered glass due to NiS inclusions is low, if a batch of glass is contaminated, the incidence of breakage on a particular building can be quite high. Since the likelihood of spontaneous fracture of fully tempered glass is unpredictable, the issue needs to be addressed on all buildings for which the use of monolithic, fully tempered glass is being considered. For example, consider the risk of spontaneous breakage of a non-heat-soak tested, monolithic, fully tempered glass as the exterior lite of an IGU installed in an all-glass curtain wall high-rise in a heavily populated downtown environment with active sidewalks below—is this a tolerable risk the design and construction team is willing to take?
Owners do not expect the glass on their buildings to fracture spontaneously, inviting injury and damage, nor should they. After nearly 60 years of manufacturing knowledge about the inherent susceptibility of fully tempered glass to NiS-induced spontaneous fracture, and 30 years after the issuance of the technical bulletin on the subject, it is time to fully address the issue, which continues to plague the industry to this day. For most projects, there are viable alternatives to the use of monolithic, fully tempered glass. Where monolithic, fully tempered glass is absolutely required, there are techniques to minimize these inherent risks. All parties of the design and construction team need to have frank, early discussions about these inherent risks to foster informed decision-making for the project at hand.
John A. Jackson, AIA, is project manager at Simpson, Gumpertz & Heger in Washington, D.C. Jackson holds bachelor of architecture and master of engineering (structural) degrees, from the Pennsylvania State University. He has more than 14 years of experience in building enclosure design and consulting, with particular expertise in curtain walls, custom glazing systems, structural glass, and glass investigations. He is an active member of the ASTM Subcommittee E06.52, “Glass Use in Buildings,” and regularly lectures on building enclosure design. Jackson can be reached at jajackson@sgh.com.
Thomas A. Schwartz, PE, is a senior consulting principal at Simpson, Gumpertz & Heger in Boston. Schwartz holds a bachelor of science degree in civil engineering from the Tufts University and a master of science in materials engineering from the Massachusetts Institute of Technology. For more than 40 years, Schwartz has conducted field and laboratory investigations, and produced new and remedial designs for building enclosure systems, including curtain walls, glazing, roofing, waterproofing, and masonry. He has been active in national standards development and research on various topics related to the construction industry, is a fellow of ASTM International, and past chair of the ASTM board of directors. Schwartz can be reached at taschwartz@sgh.com.
Having specialised in the spontaneous fragmentation for several decades I find that some of the recommendations by the authors, such as specifying heat strengthened glass which is not prone to breakage due to nickel sulfide to be erroneous and misleading.
I have witnessed several NiS breakages in heat strengthened glass.