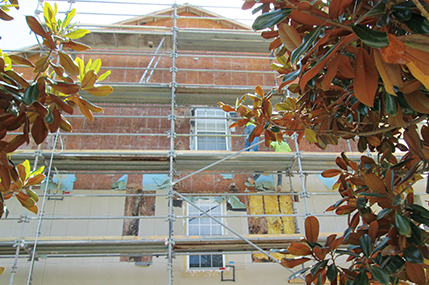
by Brett Newkirk, PE
There are two maxims about stucco application over wood-framed structures: first, it will crack, and second, owners will not do much about it. Water intrusion through stucco claddings is so common in Florida, re-skinning buildings here after five or 15 years is commonplace, even though it is not always warranted.
In some cases, re-skinned buildings are needing to be re-skinned again due to moisture intrusion years later. Damage to building structures is frequently related to poor installation of the veneer system and associated flashings.
In some examples, the stucco systems have been installed in general compliance with the building code requirements and product manufacturer instructions, yet damage to the wood substrate still ensues (Figure 1). Why then, does a code-compliant system fail?
This article includes a study of code requirements for stucco veneer systems to help explain the situation for design/construction professionals.
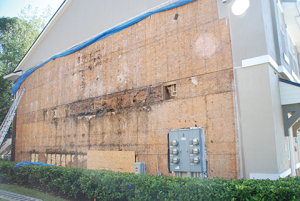
Bond-break layer
A major change was introduced to the 2003 International Building Code (IBC) and the 2004 Florida Building Code (FBC), which required two layers of an approved water-resistive barrier (WRB), equivalent to two layers of Grade D paper, behind stucco veneers. The purpose of the second (outboard) layer is to create a ‘bond-break’ between the back plane of the stucco rendering and the WRB’s front face.
The bond-break layer (BB) is intended to provide a disruption to the potential capillary movement of moisture from the stucco across the WRB and into contact with the wood wall sheathing. To that end, the bond-break layer is supposed to create a small air space, allowing gravity to draw moisture to the base of the wall, where it presumably will drain out of the wall system before it absorbs across the cross-section of the WRB. While this code change was a huge stride and of sound substance, it was not quite enough.
The problem is the method by which stucco is secured to the walls and through the WRB and BB. Fasteners, typically staples, are installed with a pneumatic tool that draws the lath tight against the BB and WRB. The tightly bound sandwich of lath, BB, WRB, and wood wall sheathing at each connection does not offer sufficient separation to break the capillary path of moisture travel or allow for drying of moisture in the system, even when a BB is present. Thus, the BB’s purpose is negated, and capillary movement across the system is possible.
However, the greater concern is a hole (or two, thanks to a staple) is conveniently created by the fastener at the precise location where the weatherproofing sandwich is tightly squished together (Figure 2). Consequently, permeation through the WRB is not required. Instead, moisture accumulates within the tightly bound assembly, clings to the fastener shank, and travels through the fastener hole in the WRB into contact with the wall sheathing (Figure 3). Equally important is the inability of moisture within the assembly to dry due to the tightly bound, unventilated space between the veneer and the wood substrate. Instead, the chronically damp conditions are favorable for wood decay.
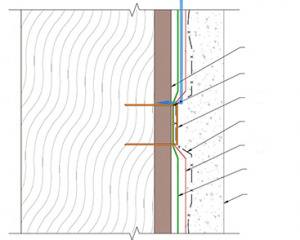
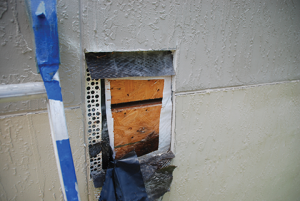
By code, the metal lath is fastened to the wall sheathing with more than one fastener per square foot of wall area. Some rough math reveals there are on the order of 6000 holes through the WRB for a one-story 230-m2 (2500-sf) structure footprint.
Stucco accessories, such as casing beads, weep screeds, and control joints, are typically installed prior to lath. Accessories are also typically secured with pneumatic fasteners, which draw them tight to the BB, eliminating any meaningful drainage space behind the accessory. Consequently, water within the system tends to accumulate along the horizontal edges of the accessories, where it may find weaknesses in the WRB, prompting migration to the interior. Of course, fasteners securing the accessories also serve as conduits for water to migrate through the WRB.
Water-resistive barrier performance
Sheet-good WRBs are tested in a laboratory setting to ensure they perform under a battery of tests established by the International Code Council Evaluation Service (ICC-ES). The most commonly used WRBs are polymeric sheets called ‘house wraps’ or ‘building wraps.’
ICC-ES AC38, Acceptance Criteria For Water-resistive Barriers, evaluates the WRB material’s tensile strength, vapor transmission, air permeance, and resistance to water penetration, to name a few. The polymeric material’s adequacy in resisting water penetration is judged by its ability to prevent water passage for two hours when subjected to a 25 to 550-mm (1 to 24-in.) column of water on one side. Once proving performance, the WRB is considered code compliant. However, the battery of laboratory tests fails to include one little detail of real life: holes in the WRB from veneer fasteners.
A single fastener penetration would result in a ‘failure’ of the AC38 water penetration resistance test. Why should one expect field performance of a product that is installed in a different (and far inferior) manner than that under which it was tested and approved?
To this author, even more perplexing is AC38’s seeming double standard for the use of paper-based WRBs, which are not subjected to the same tests as those required of polymeric WRBs. Grade D paper is used as the backing for paper-backed lath, whose installation is the most common means of creating the BB layer. By definition, Grade D paper allows water to pass after only 10 minutes of exposure with no meaningful hydrostatic pressure, while polymeric WRBs are expected to perform for hours, at pressures of up to 5.36 kPa (112 psf). Why then are two layers of Grade D paper the code-mandated baseline for WRBs behind stucco veneers? Obviously, the very low tolerance of Grade D paper to resist moisture absorption can cause substantial moisture-related distress to wood-framed buildings where it is used.
Mockup testing
Full-scale testing was performed by this author to gage the performance of several ‘code-compliant’ stucco wall assemblies, with various polymeric-based and felt-based sheet-good WRBs. The tested wall assemblies consisted of 1.2 x 1.2-m (4 x 4-ft) specimens constructed with wood framing and oriented strandboard (OSB) sheathing, and then clad with various types of WRBs.
A three-coat stucco system was then applied over paper-backed metal lath secured with 25-mm (1-in.) crown staples, confined within 22-mm (7/8-in.) plastic casing bead accessories that were secured around the wall’s perimeter (Figure 4). A 0.6 x 0.6-m (2 x 2-ft) observation port was created in the center of the OSB substrate, where gypsum wallboard wrapped in kraft paper was substituted for the OSB (Figure 5). This way, the wallboard could be removed and the back side of the WRB could be observed after testing. The kraft paper also served as an indicator of water contact during the test.

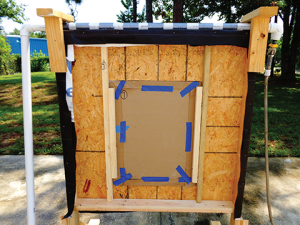
Testing was performed using a variation of ASTM E2273, Standard Test Method for Determining the Drainage Efficiency of Exterior Insulation and Finish Systems-clad Wall Assemblies (AC38 drainage test), with the additional step of performing observations for moisture ingress during the test. (ASTM E2273 only calls for a comparison of the volume introduced to the specimen to that which escapes at its base. This measurement was not of interest to the author as it related to this evaluation.)
Water was introduced to the drainage cavity at the top of the wall at a rate of 3.38 L/min/m2 (5 gal/sf/hr) for 30 minutes. Perhaps unsurprisingly, the testing revealed water penetration occurred through the fastener penetrations in both polymeric and felt-based WRBs (Figure 6). Water migration also occurred directly through the field of some woven polymeric WRBs and Grade D paper. Intrusion through Grade D paper-based WRB mockups was substantially more severe than that of the polymeric or felt-based WRBs.
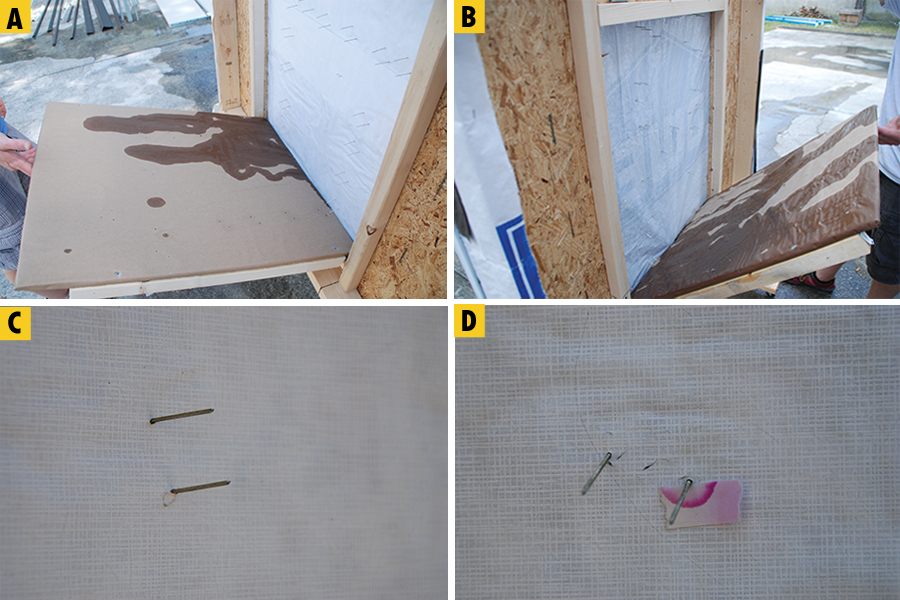
Magnified observation of staple-penetrated WRBs reveals an oblong, torn annular opening is created around the shank (Figure 7). The torn annulus was more significant at woven than spun-bound WRBs. In some cases, an additional indentation and hole through the WRB was noted due to the actuation of the pneumatic tool which impacted its surface. Additionally, use of ‘slap’ or ‘hammer-tacker’ staples caused rupturing of the WRBs at the staple shank hole and the tool’s impact location, which could allow water passage.
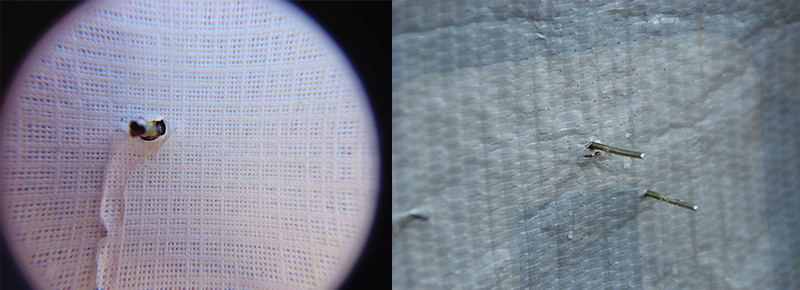
Where to go from here
It probably does not take the foregoing technical discussion to understand holes are paths for water entry or wood that stays wet will rot. So why do we build walls with thousands of holes in them, prevent them from drying out, and expect them to have watertight performance?
If repeating an activity and expecting a different result is the definition of insanity, then why do we tear stucco veneers off of water-damaged building structures and then replace it the same way? Accepting the realities of stucco cracking and inadequate owner maintenance, something else needs to change to give stucco-clad buildings
a longer life.
Based on the author’s testing and experience, there are a few installation practices that can help mitigate the compression of the veneer’s weatherproofing sandwich, which helps prompt drying and greatly reduces the likelihood of moisture migration through fastener penetrations in the WRB.
Separate stucco from WRB with furring or other drainage media
There are many randomly oriented polymeric filament products, typically 6 mm (1/4 in.) in thickness, that provide this function (Figure 8). Often called drainage media, drain screens, furring, or drainage mats, these products should be installed behind all accessories.
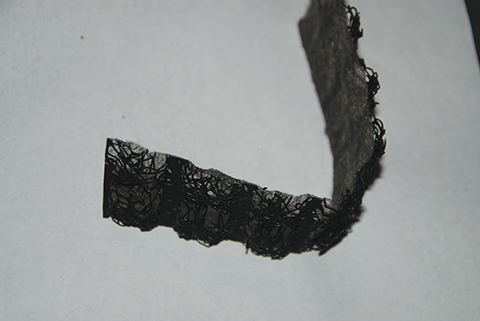
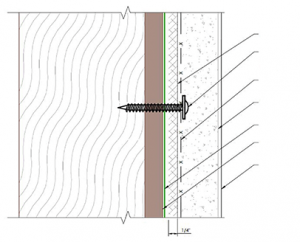
The resulting air space creates a functional capillary break between the back side of the stucco rendering and the WRB, even at fastener locations (Figure 9). This gap provides an easy, unobstructed path for moisture to travel vertically down the face of the WRB (within the media). In combination with through-wall flashing vents and drainage weeps at the stucco base, the air gap also prompts ventilation within the cavity that prompts drying of moisture.
Control the installation force and depth of fasteners
This can be achieved by reducing the air pressure for pneumatic tools, but is most effectively completed by use of pan-head screws, which have installation depths that can be easily controlled and adjusted (Figure 10). The use of screws also inherently reduces the number of penetrations through the WRB by half, when compared to staples that have two shanks. Further, the cross-sectional diameter of the screw is greater than that of a staple shank, rendering it less vulnerable to corrosion over time. (The drainage system anticipates water to drain across the unprotected fastener shank.)
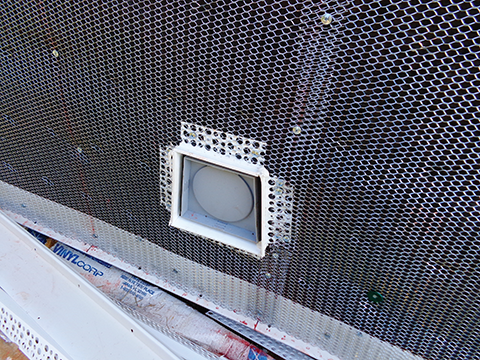
Use fluid-applied weather barriers.
Fluid-applied weather barriers cannot be torn; they create a ‘gasket’ effect around penetrating fasteners. However, these products’ detailing and reinforcing requirements demand a more skilled and conscientious craftsman to properly install. Designers should also recognize fluid-applied barriers are typically vapor-impermeable, which should be a consideration in the envelope design.
Conclusion
The recommendations in this article are an additional step to prevent water intrusion through stucco-veneered walls and to prompt drying beyond current code requirements. Of course, these suggestions are no guarantee against water penetration—after all, one still has thousands of un-gasketed holes through the sheet-good water-resistive barrier. However, with proper WRB installation, appropriate flashings and drains, incorporation of drainage media, and controlled depth fasteners, a stucco veneer has a much better chance at providing long-term performance.
Brett Newkirk, PE, is a practicing structural engineer with Alta Engineering Company in Jacksonville, Florida. He specializes in the diagnosis and repair of moisture-affected structures, and is a recognized author and leader in the building envelope repair industry in the southeastern United States. Newkirk is an associate member of the American Society of Civil Engineers (ASCE) and sits on ASTM committees for wood and gypsum. He can be reached at brett@altaengineeringco.com.
I really like the look of stucco houses, but I have noticed a lot of cracks in some of the homes on my street. It is good to know that there are ways to avoid this. When we start construction on our home, I’ll be sure to ask what sort of water barrier I should use behind the stucco.
These measures aren’t to keep stucco from cracking, but how install stucco so that when it does crack the layers behind it still keep the moisture away from the structure.
Strong article focused on the components that really matter. I would add that full embedment of the Lathing reinforcement (that is 1/4″ furred from surface) via the stucco scratch-coat is essential to a successful installation and service life as well.
Build with masonry (concrete block) and you eliminate nearly all of these concerns and get the stucco system applied for 1/4 to 1/6 of the cost.