by Jason Spangler
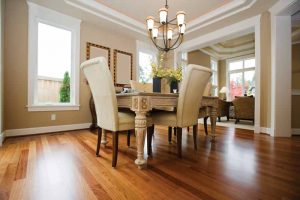
The visual appeal of a wood floor is hard to match. Most people experience a certain joy when entering a building where wood has been used generously. They may not be able to put their finger on exactly why they react favorably to wood—it may be the touch of elegance or the warm glow they sense, but whatever it is, the positive impression is indisputable.
Wood’s advantages are more than skin deep
Wood flooring offers more advantages than just aesthetic appeal in both homes and commercial settings. It is easy to clean and is significantly more stain-resistant than carpeting. Wood is also strong and durable, and if properly cared for, its hard surface can last for decades. When a wood floor shows signs of wear from years of regular use, many can simply be refinished rather than replaced entirely. Wood floors also add value to any building, increasing the resale value by as much as 10 percent or more.
A wood floor also contributes to better indoor air quality (IAQ). Unlike carpeting, or even the grout lines of a tile floor, wood floors do not trap dust, pollen, particulate matter, or other common allergens. Wood floors can even improve acoustics. For example, hardwood floors can produce a clean, clear, crisp sound as opposed to other types of flooring that may soften or deaden sound, which is one reason why hardwood gets used frequently in dance or music studios. When choosing flooring material, one should consider what type of effect they are trying to produce.
Beware of subfloor moisture
On any commercial flooring project where wood is going to be used, it is important to consider in advance how moisture could play havoc with the design goals. It is crucial to address all possible sources for excess moisture. The National Wood Flooring Association (NWFA) has estimated at least 75 percent of all flooring failures are the result of moisture issues.
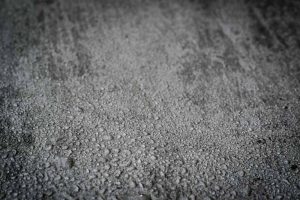
One of the most common, but sometimes overlooked, sources of moisture is in the subflooring.
In commercial settings, wood flooring is typically installed over a concrete floor slab. Concrete slabs may look perfectly solid and feel dry to the touch, suggesting they hold very little water inside. In reality, water is always an essential ingredient in the concrete mixture, and all concrete slabs, whether freshly poured or even decades old, will harbor surprising amounts of moisture.
It is important to note, the manufacturer’s specification (if applicable) for the wood product should be the guide regarding what is an acceptable moisture condition for the concrete slab. However, the typical limit for wood and wood-based products is about 75 percent relative humidity (RH) in the slab.
Indeed, without enough water, a concrete slab will not cure properly and attain its characteristic hardness. Curing takes relatively little time. Generally, concrete sets in 24 to 48 hours allowing one to walk on it. Within seven days, one can expect the slab to cure to about 70 percent of full strength, and in about 28 days, the concrete should be approaching full strength.
This curing process should never be confused with concrete drying. While curing happens rather quickly, concrete drying does not. Once a slab is poured, moisture begins leaving the slab from the ‘inside out.’ What this means is moisture within the slab migrates to the surface over time and then evaporates. Ambient conditions will affect the speed at which this process occurs, but it is never particularly fast. For a 127-mm (5-in.) concrete slab, it may take five months or more for the slab to dry sufficiently. This would be after the building is enclosed and an environment conducive for drying is established. The concrete must be fully dry before one can successfully install a finished floor product.
Failure to build this drying time into the overall project and conduct an accurate moisture assessment of the concrete floor slab may mean scrambling later to address one or more serious moisture-related problems. The initial excitement over the beauty of a project’s wood flooring may rapidly wane and turn to frustration and headache instead.
Visible signs of a hidden moisture problem
Since wood is a hygroscopic material, wood flooring naturally expands when moisture is present and shrinks when moisture is absent. Excessive moisture in wood flooring can present itself in several different and problematic ways.
…the in-situ RH specification is available for free download.
This link leads to an error message: SORRY…Page Not Found
Hi
The broken link has been fixed.
Regards,
Nithya
House is 50 years old .there was hardwood flooring we took it up can I float new solid hardwood ?