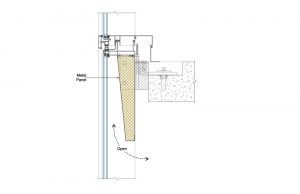
Illustration courtesy Simpson, Gumpertz & Heger and Oldcastle Building Envelope
Although the glass panel is required to be larger in a touch-mullion (compared to two smaller panels in a traditional shadow box), depending on the aspect ratio, the touch-mullion can provide additional structural support to the glass (e.g. under wind loads). The structural design of the glass, structural silicone, and touch-mullion need to be carefully considered with this type of shadow box.
Heat buildup in the cavity, condensation risks, and consequences of dust/debris/condensation marking the glass are similar in a touch-mullion shadow box. However, as the assembly uses a single glass panel additional challenges must be considered. For instance, a greater thermal stress gradient can occur within the glass panel (requiring heat-treated glass) and must designed accordingly. Further, the seal of the structural silicone at the touch mullion must be to the primary seal of the glass at the vertical mullions to prevent interior humidity (e.g. during cold winter months) from entering the cavity and potentially condensing within the shadow box. Should dust/debris and/or condensation/streaking happen or if glass breakage occurs, the entire glass panel must be deglazed to access for cleaning/replacement. In addition to the field reglazing challenges previously discussed, reglazing the entire glass lite is required at a touch-mullion, resulting in even greater complication such as requiring fall protection and a temporary weather enclosure—both of which can be disruptive to building occupants.
Open shadow box
An open shadow box (sometimes referred to as a ‘faux shadow box’), takes the design one step further by simply eliminating the touch-mullion and allowing the cavity behind the glass to be open to the building interior (Figure 8). A metal closure panel is often installed as part of the glazing system to visually conceal the slab edge and ceiling plenum behind.
As the structural support of a touch-mullion no longer exists, the span of the glass panel is greater and, therefore, may need to be thicker compared to other glass spandrel types.
Risks of heat buildup within the cavity, glass differential thermal stress, and risks of condensation are greatly diminished with the open shadow box as the cavity is fully open to the building interior. This also allows more natural daylight into the space, while at the same time introduces more solar heat gain into the building (which may be beneficial in colder climates). The additional solar heat gain will need to be managed by the building’s mechanical system.
Depending on a variety of factors (e.g. depth/height/geometry of the cavity, color of metal panel, and thickness of insulation), the building’s mechanical system (e.g. diffuser location relative to the open shadow box cavity), presence of interior blinds (e.g. in the down position can preclude beneficial heat resulting in increased risk of condensation in the open cavity; it can also trap solar heat in the cavity) and exterior climate/solar orientation, heat and condensation can still buildup in the cavity.
Generally, with this design, the interior surface of the glass can be more readily accessed from the building interior for maintenance and cleaning activities, if the cavity dimension/geometry are adequate for access. In addition to access for routine cleaning, cavity dimension/geometry must be carefully considered for interior access (e.g. to remove and reinstall structural silicone) for glass replacement.
Other considerations
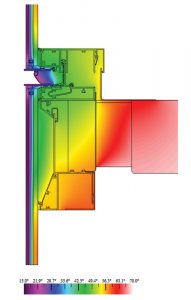
Illustration courtesy Simpson, Gumpertz & Heger and Oldcastle Building Envelope
In addition to the considerations of the various glass spandrel assemblies discussed, additional design and construction considerations include thermal performance, edge-of-slab fire safing, glazing system selection, and construction methodology.
In hot climates solar heat gain (or lack thereof) through glass spandrels (e.g. opaque spandrel glass versus open shadow box) can have a greater influence on overall building energy performance compared to spandrel thermal performance (i.e. U-factor), whereas in cold climates, the reverse can be the case.
The U-factor of glass spandrels can vary depending on the details of the spandrel assembly construction. The primary influences which affect the spandrel system’s thermal performance include the overall size of the spandrel (larger spandrels with less framing generally improve thermal performance), the glass type (i.e. IGU versus non-insulating), insulation thickness, details of the interior membrane/back-pan (i.e. foil-facer versus metal back-pan, including back-pan anchorage details/thermal breaks to the perimeter framing), and the types of thermal break (if any) in the mullion framing (Figure 9). Determination of U-factor performance of spandrel assemblies are calculated as an area-weighted average of system components (typically in general accordance with National Fenestration Rating Council [NFRC] 100, Procedure for Determining Fenestration Product U-factors). Due to the unique nature of glass spandrel assemblies (compared to vision glass), determination of spandrel U-factors can be challenging for some design teams as many of the codes and standards have several shortcomings, and can often result in inaccurate (and often unconservative) calculations.1