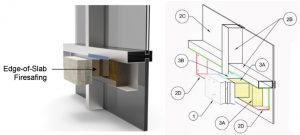
Illustration courtesy Specified Technologies Inc.
Another important design consideration for spandrel assemblies which extend past the slab edge (e.g. continuous curtain wall systems) include accommodation for fire safing the gap between the edge of the slab and the back of the curtain wall system (Figure 10). Installing a tested joint fire safing system (e.g. in accordance with ASTM E2307, Standard Test Method for Determining Fire Resistance of Perimeter Fire Barriers Using Intermediate-scale, Multistory Test Apparatus) is required to prevent the passage of smoke and flames from one floor to the next.
Fire safing systems typically include filling the gap with mineral wool insulation and covering the top with a smoke seal; fire safing systems can also include additional components like sheet metal depending on the design. In addition to the fire safing system, the performance of the system is also dependent on the details of the construction of the curtain wall’s spandrel assembly. This includes items such as the height of the spandrel, details of the interior membrane/metal back-pan (e.g. metal gauge, stiffeners, anchorage), and insulation type and thickness within the spandrel assembly. Often, engineering judgements based on tested assemblies (or project-specific testing) are required to demonstrate code compliance of unique glass spandrel assemblies.
Perhaps one of the most important considerations in glass spandrel design is the method of construction. In general, factory-glazed spandrel assemblies—unitized curtain wall or window wall—are preferred over field-assembled systems, such as stick-built curtain wall thanks to improved quality control and the ambient environment offered by factory conditions. This is particularly true for vented shadow box assemblies which use a metal back-pan that functions as the system’s primary air-water-vapor seal. Mullion frame joinery is typically sealed in unitized systems and, therefore, the primary air-water-vapor seal can be accommodated in various locations throughout the depth of the mullion, whereas with stick-built, the primary air-water-vapor seal is at the shoulder of the mullion. For these reasons, venting is common in unitized systems as it can easily be accommodated in the design. On the other hand, integrating venting into stick-built curtain walls can be more of a challenge as the system’s air-water-vapor seal design does not necessarily easily accommodate venting.
Further, proper installation of critical air-water-vapor seals in the field can be particularly challenging where access for installation is often limited at the slab edge. Field-glazing of spandrel assemblies can potentially trap moisture (e.g. on a warm humid day or a rainy day) and/or dust/debris (e.g. due to adjacent construction activities) within the assembly when glazing occurs. If the spandrel assemblies rely on foil-faced insulation as the interior vapor seal for preventing condensation, transportation, and installation, adjacent construction activities can easily damage the often-delicate foil-facers. This alone is often a good reason for using more robust metal back-pans instead. In addition, actively humidified buildings (e.g. museums, hospitals) in cold climates, present increased risks of wintertime condensation in the shadow box cavity (as well as on the interior surface of the vision glass). In these cases, well-sealed, thermally broken, robust metal back-pans in lieu of taped-foil facers are often required.
For factory-glazed assemblies, surfaces within the shadow box assemblies (e.g. interior surface of glass, metal panels) must be properly cleaned prior to glazing. In addition, exposed baffled vent/weep holes of bunked unitized panels must be properly protected during storage, transportation, and prior to installation on-site to prevent potential dust/debris and moisture (and potentially bulk water) from entering the cavity.