Technology boosts performance
By eliminating the need for physical paper and manual processing, mobile technology facilitates more efficient, cost-effective, and accurate delivery of materials to the site. An automated routing and scheduling system can accommodate highly variable construction environments with strict operational discipline and predictability.
Real-time delivery route planning
Conventional paper- and clipboard-based routing is highly inefficient and can cause many errors. A completely paperless, technology-based environment can make it easier for suppliers to plan deliveries, schedule appointments, optimize routes, dispatch orders, and communicate with drivers. Activities such as reassigning deliveries, responding to contractor changes, and managing exceptions tasks can be done virtually instantaneously with an electronic logistics management solution.
Real-time route planning benefits contractors by driving up the delivery performance of their suppliers. With more intelligent route planning and more reliable delivery environments, suppliers can improve on timeliness, capacity utilization, and contractor satisfaction. Efficient automated routing also reduces transportation costs, mileage, fuel consumption, and vehicle idle times—this last factor can be lowered to one hour per day per vehicle.
Dynamic appointment scheduling
Appointment scheduling is affected by many factors for which a supplier cannot plan, such as:
- changing contractor demands;
- crew and resource availability;
- weather; and
- inventory requirements.
Any of these elements can increase or decrease productivity and profitability for both contractors and suppliers; thus, efficient routing is impossible unless the system accounts for these types of scheduling variables.
Dynamic appointment scheduling gives suppliers not only unprecedented insight into the impact of unforeseen changes, but also the tools to exert more control over variables. Suppliers can use this technology to make on-the-fly adjustments and immediately communicate the details to all participants and stakeholders.
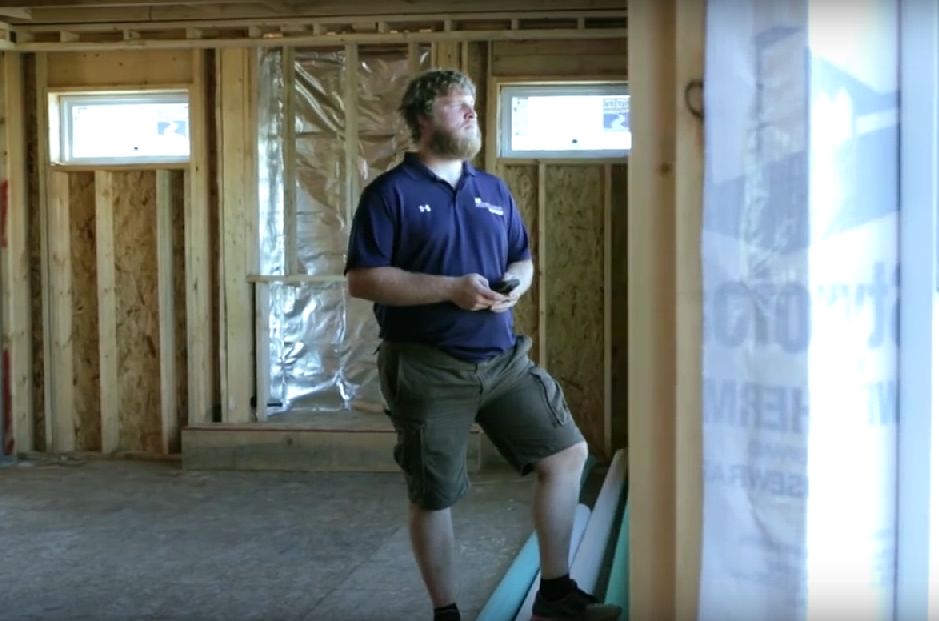
Real-time updates on mobile devices
Contractors need to know exactly when material is arriving at various worksites to efficiently manage crews. Leading companies are using mobile technology to provide contractors with accurate, extensive information on the details and timing of construction site deliveries. Drivers access their delivery schedules using a mobile device, while GPS information is received every few minutes to estimate travel time, monitor delivery appointments, and generally keep contractors updated. Contractors using mobile devices are also automatically notified when delivery schedules change.
Salespeople using mobile technology have easy access to relevant information, including which yard is shipping an order, where that load is coming from, the estimated time of delivery, and what material is on the load. The salesforce does not need to make numerous calls or send out urgent emails to get the necessary information. With one click, contractors can also call salespeople to place orders from an itemized list of materials.
Paperless proof of delivery
Paper-based proof of delivery (POD) can be fraught with illegible details, missing signatures, lost paperwork, and time-consuming disputes between suppliers and contractors. With mobile devices, drivers have everything they need to wirelessly confirm deliveries and other details, virtually eliminating paperwork. Drivers use electronic signature capture and digital pictures to verify that the right materials, in the right quantities, were delivered safely at the expected time. Paperless POD allows drivers to collect information faster, meaning they can get back on the road faster, meet other delivery windows, and even build up to more deliveries per day.
With electronic POD, invoicing, end-of-day reconciliation, and returns are processed faster. Customer calls and claims are reduced, the risk of fraudulent claims is mitigated, and claim resolution becomes much easier to achieve. POD technology also reduces costly or labor-intensive practices associated with paper, such as multiple-part invoicing and the use of resources dedicated to processing, imaging, and storing paper documents.
Affordable cloud-based deployment model
Given that advanced route planning and mobile solutions are available in cloud-based deployment models, cost is not a barrier to use of this technology, even for small- to medium-sized companies. Depending on the requirements, a routing system can be installed in a traditional desktop environment or implemented as a user-friendly web-based solution to minimize in-house IT management and upfront capital. For companies with multiple divisions and locations, these options allow for one route planning and mobile system to support all locations while accommodating differences in operating processes.
Mobile delivery management in action
By replacing paper-based logistics management with a mobile solution, one collection of building material distributors was able to improve its on-time delivery performance from 70 percent to 95 percent at many locations. Yard personnel are notified via text message 45 minutes before trucks return, which allows time to stage material. In New Jersey, one of the company’s biggest markets, this process allowed the team to reduce truck turnaround times to 25 minutes—a 30 percent decrease. These types of results on the supplier side improve contractor efficiency.
Delivery-related costs also decreased by more than 10 percent following the company’s switch to mobile technology, likely due to more efficient warehouse operations, reduced fuel usage, and fewer expedited deliveries. In addition, electronic POD helped the company save tens of thousands of dollars with better delivery claim resolution.
Conclusion
Paperless is possible! In a data-driven, mobile-focused world, the paperless supply chain is a new competitive weapon in home building and supply work. Switching from paper to mobile technology can help suppliers master their chains and reap benefits at all levels of construction.
Kenneth Edward Wood serves as executive vice president of product management at The Descartes Systems Group. Wood joined Descartes in July 2001, in connection with the company’s acquisition of Centricity. He provides leadership in defining company product strategy, developing roadmaps, and working with all aspects of product delivery. Wood can be contacted by e-mail at kwood@descartes.com.